Knit fabric and sportswear maker The Yeh Group is launching a new range of fabrics that use a waterless dyeing process and should save the company millions of litres of fresh water use each year.
The Bangkok-based company plans to introduce the DryDye fabrics later this year and believes it will be the first textile mill to implement a new process developed by DyeCoo Textile Systems.
Instead of current aqueous dyeing systems, DryDye fabrics will be dyed using supercritical carbon dioxide in a stainless steel chamber developed and tested by DyeCoo.
Already use in extraction processes in the food industry and apparel dry cleaning, supercritical fluid CO2 enables polyester and other synthetics to be dyed with modified disperse dyes. It causes the polymer fibre to swell, allowing the disperse dye to diffuse and penetrate the pore and capillary structure of the fibres.
The viscosity of the dye solution is lower, making the circulation of the dye solutions easier and less energy intensive. This deep penetration also provides effective coloration of polymers. Furthermore, dyeing and removing excess dye can be done in the same vessel; and residue dye is minimal and may be extracted and recycled.
The Yeh Group says DryDye fabrics have the same dye qualities and durability as conventionally-dyed fabrics.
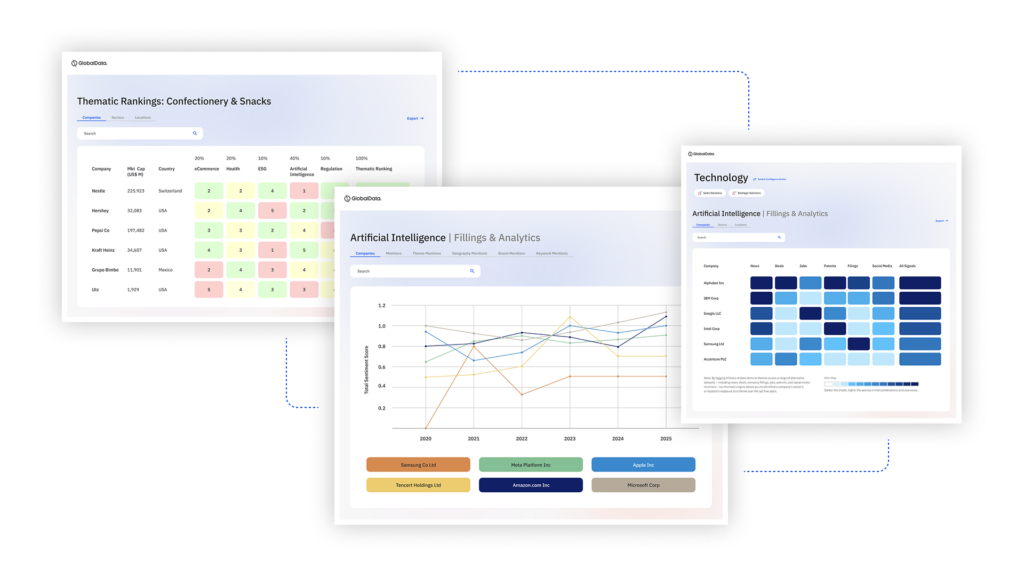
US Tariffs are shifting - will you react or anticipate?
Don’t let policy changes catch you off guard. Stay proactive with real-time data and expert analysis.
By GlobalDataConventional textile dyeing is very water and energy intensive in all stages from pre-treatment, to dyeing and post-treatment (drying). The supercritical CO2 process uses less energy than conventional processes during last two stages; while the pre-treatment process is essentially the same for both.
The textile industry is believed to be one of the biggest consumers of water, using large amounts of fresh water which then is disposed as waste water containing dyestuff chemicals.
On average, an estimated 100-150 litres of water are needed to process 1kg of textile material. Water is also used as a solvent in many pre-treatment and finishing processes, such as washing, scouring, bleaching, dyeing, rinsing and finishing.
The contaminated water must then be handled and treated prior to disposal or recycling.
The Yeh Group makes performance fabrics and garments for sportswear and intimate apparel customers such as Adidas, The North Face, Puma, Mizuno and Victoria’s Secret . It has sales offices in Europe and North America.