Singapore-based dye manufacturer Dystar has launched an extension to its Cadira concept that it says will considerably reduce process costs, water, waste and energy consumption and machine utilisation in the dyeing process.
Cadira Reactive/Disperse Continuous is a modified pad-dry-thermosol-pad-steam (PDTPS) dyeing process for open width polyester and cotton fabrics. In contrast to the standard PDTPS process, Cadira Reactive/Disperse Continuous does not require a separate reduction clearing process and thus saves more than 40% chemicals, water and energy, the company says.
This effect is obtained by using a special dye choice of Dianix XF/XF2 and SF disperse dyes in combination with selected Levafix and Remazol reactive dyes and a modified steaming and wash-off process with Sera auxiliaries.
“Cadira supports brands and retailers and their production partners in their effort to save valuable resources and to reduce the carbon footprint of their textile goods,” Dystar says.
The first Cadira module was developed in 2016. Since then DyStar has launched Cadira concepts for various substrates and applications. Cadira Reactive/Disperse Continuous is the seventh concept of the company’s ‘Resource Efficiency Program’ to help companies save valuable resources, to reduce the carbon footprint of their textile goods and to increase productivity by improving the utilisation of machinery.
In November, Dystar launched Cadira Denim to allow salt-free dyeing with a strong effluent load reduction using a combination of its pre-reduced liquid indigo dyes and its reducing agent Sera Con C-RDA.
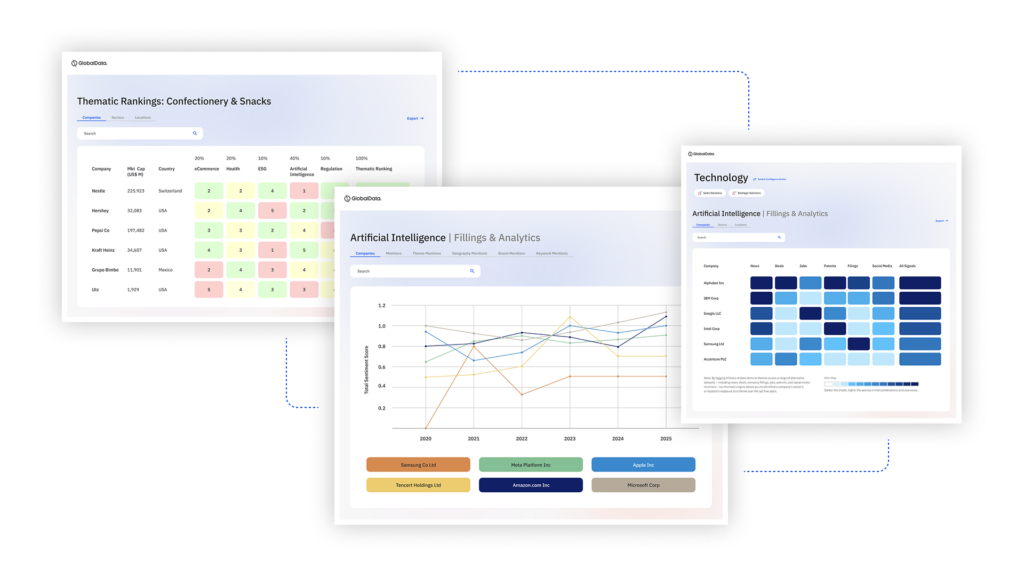
US Tariffs are shifting - will you react or anticipate?
Don’t let policy changes catch you off guard. Stay proactive with real-time data and expert analysis.
By GlobalDataOther Cadira concepts include Polyester Recycled Polyester, Vat, Reactive, Procion PX, and Wool.