
As new data released by the International Labour Organization (ILO) shows some 2.78m workers die from occupational accidents and work-related diseases every year, the agency’s Better Work programme is calling for safe and healthy working conditions across the garment industry.
Better Work operates in seven countries (Bangladesh, Cambodia, Haiti, Indonesia, Jordan, Nicaragua and Vietnam) working with about 1,600 factories that employ some 2.2m workers.
In light of the ILO’s recent ‘Safety and Health at the Heart of the Future of Work’ report, Better Factories Cambodia (BFC) says effective factory policies and procedures are key to worker safety.
BFC carries out annual assessments on how local garment factories meet legal requirements on Occupational Safety and Health (OSH) across the country.
The programme looks at a string of compliance points spanning the use of chemicals and hazardous substances, emergency preparedness, health services, OSH management systems, and worker protection.
A challenging issue across the global garment industry, OSH also continues to be a stumbling block for Cambodia’s garment manufacturing industry, Better Work says. A lack of proper policies and division of management roles and responsibilities on OSH affect many factories, it adds.
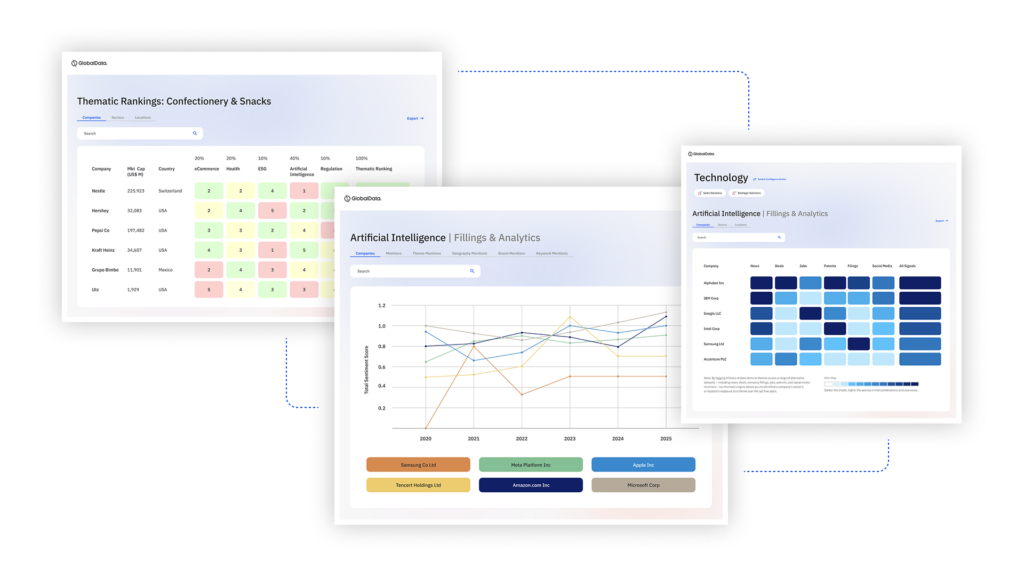
US Tariffs are shifting - will you react or anticipate?
Don’t let policy changes catch you off guard. Stay proactive with real-time data and expert analysis.
By GlobalDataBFC’s Annual Report 2018 shows that even though workplace processes, policies and procedures on safety and health are not legal requirements, there is a strong correlation between effective OSH management systems and overall OSH standards.
“Having the best policy in place is not enough unless it has been communicated to workers and management, and adopted in practice,” says Sara Park, BFC’s acting programme manager. “Establishing responsibilities and accountability are important to promoting a practical and harmonised working environment. Good OSH management systems not only improve working conditions for workers, they also have a positive impact on business through increased productivity, fewer accidents and lower staff turnover.”
BFC’s analysis on the link between OSH management systems, non-compliance on OSH and overall non-compliance of factories, shows that the better factories do on their prevention systems, the lower their non-compliance rates on OSH and overall non-compliance.
It follows that factories need to have the right capacity and skills in their teams to guarantee that proper systems are developed, and that workers and factory staff have been trained to use the systems and to continuously measure their effectiveness through a cycle of ‘plan-do-check-act.’
Examples on the ground show this is possible, the organisation says.
Better Work-affiliated Sabrina Garment Manufacturing Corporation is a factory employing almost 6,000 workers in the Cambodian province of Kampong Speu.
“Our OSH management system is based on provision of a safe and healthy workplace and the prevention, reduction of illness and injury for employees,” says Nicole Chu, Sabrina’s head of sustainability. “We continue to monitor OSH procedures to ensure our OSH programme is implemented effectively and accelerating employees’ ownership of safety and health workplace.”
Bringing the implementation of OSH measures and systems to the next level in Cambodia needs a concerted effort from all parties.
Spurred by Better Factories Cambodia, an unprecedented collaboration among the country’s garment stakeholders kicked off last year. Under the programme’s Building Bridges initiative, Ministry of Labour and Vocational Training (MoLVT) OSH inspectors, Garment Manufacturers Association in Cambodia (GMAC) representatives, union and factories managers gathered for discussions and training on OSH management systems, workplace cooperation and social dialogue. The initiative will continue throughout 2019.
Meanwhile, Better Factories Cambodia has already began working with its 557 affiliated factories through its advisory services, supporting the strengthening of their OSH management systems. A joint action plan with MoLVT to help improve working conditions in factories and workplaces across the country is also on the horizon.