Today’s supply chains bring many challenges for fashion, textile and clothing companies. Distance, complexity and scale within the context of complex international networks make supply chain management particularly resource-intensive for businesses. The garment industry alone employs upwards of 60 million people worldwide, with roughly 80% being women.
Alongside managing overseas suppliers, maintaining the flow of goods and upholding sustainable practices across global fashion supply chains, businesses are also expected to meet the requirements of an increasing number of supply chain laws.
In January 2023 a new German law, the “Supply Chain Due Diligence Act”, will become effective. The law introduces a legal requirement for large businesses operating in Germany to manage social and environmental issues in their supply chains. Companies must show that they are carrying out activities to identify and address any negative impacts on people and the planet that they may have contributed to.
The legislation is a welcome step forward in creating a level playing field for sustainable business practices.
Failing to comply with it could come at a significant cost, with the Act including fines of up to 2% of global turnover and potential bans from companies accessing public contracts in Germany for up to three years.
Understanding what to do next can be tricky for businesses to navigate. Having the right tools, data and steps forward, will help businesses pivot effectively.
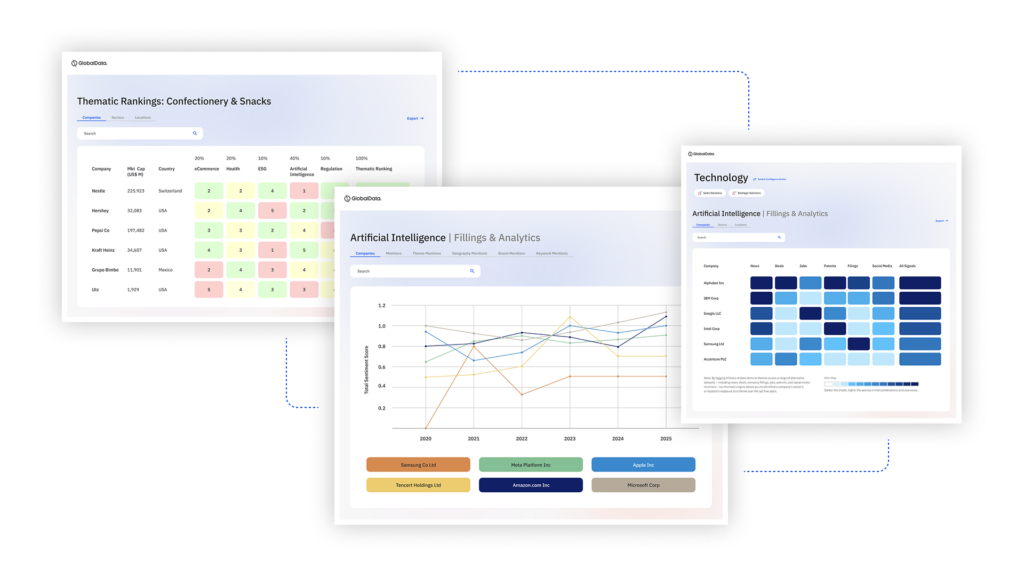
US Tariffs are shifting - will you react or anticipate?
Don’t let policy changes catch you off guard. Stay proactive with real-time data and expert analysis.
By GlobalDataHow to prepare your fashion business for the supply chain act
1. Check if your company falls under the scope of the Act
This law applies to any UK business operating with over 3,000 employees in Germany. This includes employees of all subsidiaries and businesses belonging to a parent company who work in Germany, including employees working abroad, and temporary workers with contracts of over six months. From 2024, the law will also apply to businesses with more than 1,000 employees in Germany.
2. Carry out risk and impact assessments on suppliers, focusing on specific issues
Fashion companies can start assessing their supply chains to identify the social and environmental risks and impacts they need to manage. These assessments are an important part of supply chain due diligence. The German Act lists the issues companies need to look for, and requires that companies look at both their own operations and entire supply chain – including producers of raw materials.
Environmental issues include the production and use of organic pollutants, how hazardous waste is handled, and how businesses use products that contain mercury. Hazardous waste is a particularly relevant issue to consider for textile, apparel, and fashion companies – it’s estimated that textile mills account for 20% of the world’s industrial water pollution.
Social issues include child labour, forced labour, and health and safety. Discrimination, inequality, and barriers to freedom of association are also mentioned, along with wage theft and whether wages are paid in line with relevant laws. These issues are based on international standards, such as the International Labour Organization’s list of core labour rights (the “fundamental conventions”).
Risks in supply chains change constantly, so companies should aim to risk assess at least once a year. Technology provides powerful tools to support this, such as data-led risk assessment solutions that enable a business to analyse and compare risks easily across a global supply chain. These tools use information on suppliers’ locations, operations and workforces to highlight social and environmental concerns. For example, Sedex’s risk tool shows that apparel and textile manufacturing industries globally are at higher risk of insufficient wages than of business corruption. Companies can also seek external support, such as working with a specialist consultant to help identify the issues they need to look at and develop a supply chain programme.
3. Start to carry out other due diligence activities
As well as regular risk assessment, the Act outlines other activities businesses need to carry out to avoid or reduce negative impacts. Companies should make these activities part of their regular operations and report on them annually, including how effective they have been and what impacts they identified. These activities include:
- Risk management: Having a system in place to evaluate and manage the social and environmental concerns that businesses identify in their risk and impact assessments.
- Preventive measures: Taking steps to prevent and reduce these risks. This could include embedding responsible procurement practices, training on labour rights for company staff, or monitoring suppliers to confirm that they also meet the requirements of all relevant laws.
- Grievance mechanisms: Providing an internal complaints system for a business’s workforce and suppliers’ workers, where people can share feedback safely and confidentially. For example, a mobile app can capture anonymous feedback from employees all over the world. These grievance mechanisms should support people to report social and environmental issues or incidents linked to the actions of any business in a company’s supply chain, including indirect suppliers.
- Documenting, monitoring and evaluation: Recording all these due diligence activities and keeping records on file for at least seven years.
4. Prepare a due diligence report
Businesses will need to prepare an annual report showing how they manage social and environmental issues in their supply chains. This should cover issues identified, processes implemented, and activities undertaken in the previous financial year. It should also include how the business assessed the effectiveness of its activities and lessons learned.
Companies need to submit the report to the German Federal Office for Economic Affairs and Export Control (BAFA) within four months of their financial year-end, and publish the report on their business website.
5. Look out for additional requirements
The German government is yet to share all the details of the Act, so there are still some unknowns. For instance, it’s not yet clear whether businesses will have to explicitly state in their annual reports that they’ve considered a risk and concluded it’s not relevant to their supply chain.
Preparing for a new law can feel like an overwhelming task. But with Germany being a priority growth market for many UK businesses, UK fashion and textile companies will be keen to meet the German Act’s requirements.
Businesses can get ahead by collecting data on their direct and indirect suppliers, harnessing the right tools to analyse this data, and building even more visibility of their supply chains. This visibility brings businesses long-term benefits and is a crucial foundation of sustainable business operations for long-term success.
About the author: Jessica McGoverne joined Sedex in 2018 and is responsible for its corporate communications, public relations and public policy. She has over 10 years’ experience working in public affairs crisis communications and stakeholder engagement and has led a number of development campaigns for multinational organisations.