The apparel and footwear industry must respond to the coronavirus crisis by doubling-down on efforts to create more stable, sustainable and humane supply chains for the future, writes Doug Cahn.
Since the coronavirus pandemic began to unfold, many of us have fallen into a new routine: making back-to-back Zoom calls from home offices, exchanging emails full of disheartening updates, and confronting an exhausting array of management dilemmas arising from unprecedented circumstances.
The virus’s impact has devastated brand and retailer sales, supply chain partners and – importantly – the workers who contribute their labour. Terms like game-changing, tragic, disruptive and catastrophic are no less true for having become clichés.
Brands and retailers are attempting to salvage their businesses in the face of shuttered stores and online demand weakened by record high unemployment. More than 40% of retailers have resorted to layoffs and many more to furloughing segments of their workforce. They are slashing budgets, cutting orders and delaying payments to vendors.
“Unless the pain faced by manufacturers can be eased, the supply chain relationships that have been responsible for more than 30 years of sustained industry growth are at risk”
As cancelled orders mount, suppliers still face the obligation to pay for materials and labour already committed. If large numbers of factories go bankrupt, where will brands and retailers source their goods when demand returns? What will be the impact of millions of impoverished semi-skilled factory workers on the social and political stability of producing countries? Unless the pain faced by manufacturers can be eased, the supply chain relationships that have been responsible for more than 30 years of sustained industry growth are at risk.
Civil society organisations will continue to press reputationally sensitive brands to honour commitments to suppliers and ensure that workers are paid. ReMake, Clean Clothes Campaign, Worker Rights Consortium, global unions and others are stepping up the pressure on high profile brands to pay for work-in-process and cancelled orders.
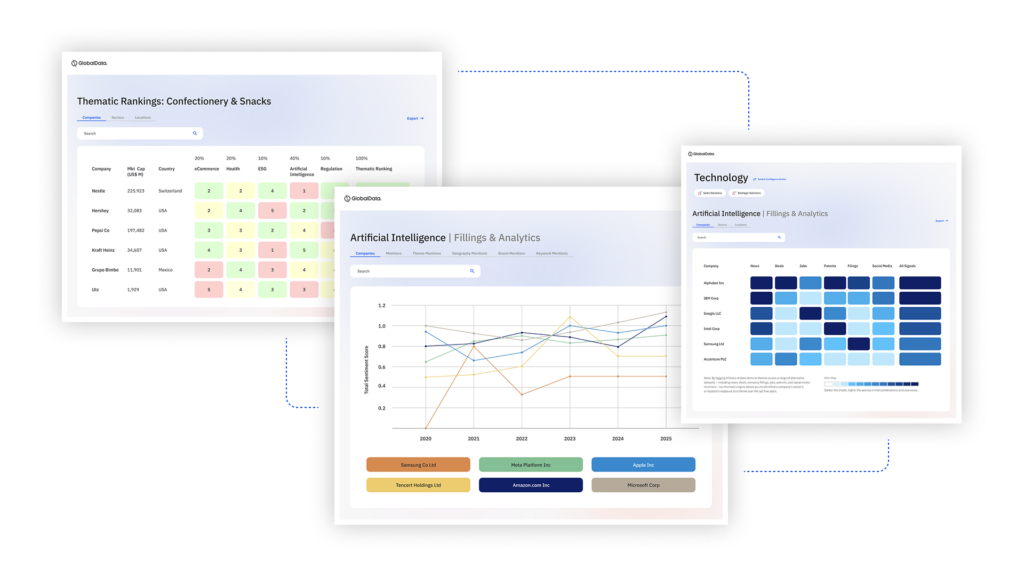
US Tariffs are shifting - will you react or anticipate?
Don’t let policy changes catch you off guard. Stay proactive with real-time data and expert analysis.
By GlobalDataBut will a new, more stable, sustainable, and humane supply chain be the result?
The apparel and footwear industries have a history of identifying areas of needed improvement, targeting resources to address them, and then failing to deliver fully on the promise for reform. Creating an effective approach to ensuring decent working conditions is a case in point.
Since the first codes of conduct for factory conditions were established in 1991 – whether to protect brand reputation and/or workers’ well-being – there has been no shortage of company-specific and multi-stakeholder initiatives, supported by a robust industry that monitors factory workplace conditions, trains workers and managers, and assesses risk across a range of human rights issues.
Yet today the corporate responsibility agenda is fuller than ever. Much more must be done to address human trafficking and the need for living wages, to name only two challenges. So how can this moment of crisis be used for good advantage?
The industry needs to double-down on efforts to collaborate. With few exceptions, factories and their labour forces are not dedicated to a single buyer. To leverage industry efforts for lasting change, country-wide or sector-wide approaches are needed. Witness how the Accord and the Alliance in Bangladesh have dramatically improved factory safety conditions. Implementing standards across the nation’s entire readymade garment sector erased any incentive to cut corners. Workers can switch factories with greater confidence that safety is assured.
The worldwide movement to harmonise workplace standards and systems for implementing them needs to be strengthened, without diluting in any way internationally recognised standards set by the International Labour Organization (ILO). Barriers to success must be swept away by intensive consultation and committed action. Government intervention may be necessary.
Global standards for responsible purchasing practices with clearly defined metrics for success must be established and followed. The current crisis has exposed the flaws in a system that puts great risk on suppliers. It will surely contribute to factory bankruptcies and great hardship for workers. An excellent starting point for devising new standards is the Better Buying’s guidelines for better purchasing practices, which was based on a survey of 294 suppliers in March.
Essential to success is winning the trust of sceptical – even angry – stakeholders. New standards for transparency must be established in collaboration with civil society organisations that advocate for workers. Companies should take comfort in the fact that recent innovations in transparency, such as factory level reporting of safety conditions in Bangladesh and brand disclosure of factories, have not resulted in supply chain disruption. On the contrary, in many cases, they have resulted in workplace improvements, more trusted relationships with stakeholders, and better brand and retailer oversight of production. New standards for transparency can become a routine part of corporate reporting and accountability.
The industry’s response to this crisis creates an opportunity to strengthen the position of all supply chain stakeholders. If it fails to do so, it invites major long-run problems. This is a time for an urgent, intensive reimagination of supply chain relationships and mechanisms of accountability. Let’s add that to the “to do” list the next time we sit down in our virtual offices.