As garment factories in Bangladesh come under pressure to reopen, Dorothée Baumann-Pauly and Natasja Sheriff from the NYU Stern Center for Business and Human Rights set out three ways fashion brands can offer practical assistance to suppliers to ensure the safety of the millions of workers who make the goods they sell.
Even as the global coronavirus pandemic continues, the economic imperative to reopen businesses is being felt in every part of the world and nowhere more so than in countries like Bangladesh, where the impact of Covid-19 could roll back more than a decade of gains in poverty reduction.
Bangladesh’s garment sector, second only to China in global clothing exports, is the country’s economic powerhouse. Its revival poses crucial and urgent questions: How can factories reopen safely, without risking the lives of millions of workers and their families, even as cases of Covid-19 surge? And what should global brands, whose demand for low-cost apparel fuels the industry, do to help?
Bangladesh confirmed its first coronavirus case on 8 March, but ominous numbers are rising, reaching over 13,000 confirmed cases and 206 deaths last week, with the likelihood of many unreported cases as well. Since factories began reopening on 26 April, 50 cases have been detected in these workplaces, according to one labour group.
Despite the health risks, pressure has increased on the garment industry to resume apparel production. “Under the present circumstances, I think it is much too soon to open factories, but the pressure on us is immense and the government has instructed us to reopen,” Nazma Akter, a prominent labour leader and president of Sommilito Garments Sramik Federation, wrote in the Daily Star. “Brands are also pushing as some stores in America and Europe are starting to reopen and they want us to go back to work as well.”
The reopening of factories is welcome and bitter at the same time. Many garment workers, mostly young women, need the income that their factory work provides and are fearful of losing their jobs. But they also know the risk to their lives and their loved ones if they return to work and contract the virus. “This job is our only hope if we are to survive with the children. So we are risking our lives,” one worker told bdnews24 as he returned to his job in Dhaka.
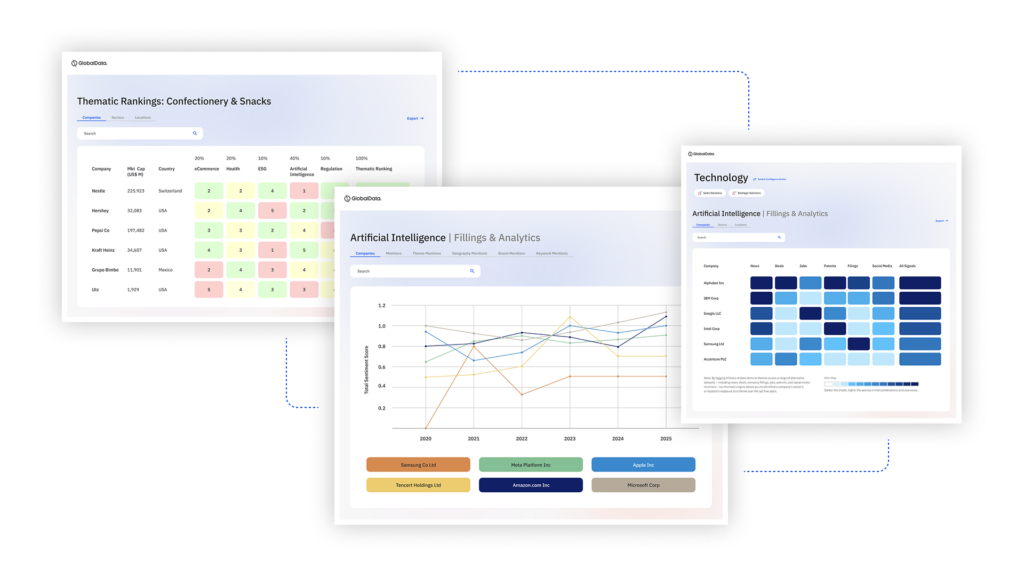
US Tariffs are shifting - will you react or anticipate?
Don’t let policy changes catch you off guard. Stay proactive with real-time data and expert analysis.
By GlobalDataSupport for suppliers
In order to make the necessary workplace changes and retrofits to keep workers safe, suppliers in Bangladesh face substantial financial and practical hurdles. And while their clients – mostly Western brands and retailers – are experiencing massive financial losses, these global companies must not turn their backs on their suppliers and the millions of workers who make the goods they sell.
#1: First and foremost, brands should ensure that their contracts with suppliers are honoured and existing orders are paid in full.
This will give suppliers a stable financial base from which additional investments in factory safety become feasible. Brands should pay for all goods received and goods in progress, as well as the costs of raw material, which suppliers generally cover in the first instance.
As the financial impact of Covid-19 has taken its toll, apparel brands and retailers cancelled orders worth billions of dollars, leaving factory owners unable to pay workers who have no idea if or when they might be paid again. Many major brands like H&M, Uniqlo, Under Armour and New Balance have now made commitments to pay for goods received and under production. This is critical. More brands should follow their example.
#2: Brands need to work with Bangladeshi factory owners to implement guidance on how to keep workers safe.
This advice needs to be practical and developed in close consultation with these local business partners.
Organisations like the International Labour Organization (ILO) outlined recommendations relating to air purifiers, hand-washing stations, temperature checks, disinfection of shoes, a split shift schedule to reduce the number of people in the factory at one time, and the reorganisation of workspaces and dining areas to keep workers six feet apart.
Although these proposals sound reasonable, Mostafiz Uddin, owner and managing director of Denim Expert Ltd, told the NYU Center for Business and Human Rights that safety measures put forward by the government, industry bodies, and international organisations are very difficult to implement in Bangladesh.
Unlike hundreds of other factory owners, Uddin has not yet reopened his factory. “I am responsible for 2,000 workers. I cannot assure their safety right now,” he said. The safety guides, he added, were drafted without consultation with manufacturers. “Everybody puts out nice instructional guides but nobody asks: is this possible in the given context? Can it be easily maintained?”
One common recommendation is that factory owners provide hand-washing stations placed six feet apart at the factory gate. Each station can accommodate about 120 workers an hour. Yet if ten hand-washing stations were provided, it would take almost an hour for just half of Uddin’s staff to enter the factory building, while workers would form a socially-distanced line stretching for over a mile. With input from manufacturers describing the local context and materials available to them, guidance could perhaps offer more practical advice on how hand-washing stations could be constructed in different settings.
Given the scale of many production facilities, and their frequent location in dense urban and residential areas, figuring out the practicalities of complying with the health and safety guidance is no easy feat. Manufacturers must have a voice in discussing the reality of implementing health and safety guidelines at the time they are defined.
#3: Brands should ensure safety measures are actually implemented, by providing technical assistance and, where needed, financial support.
This implies regular check-ins from brands with suppliers to assess their individual needs. Such collaborations will come more easily to those brands that already have established a strong relationship and regular communication with their suppliers.
Going forward, this lesson should not be lost as the garment industry moves beyond the pandemic. It’s clear that brands with a sourcing model that prioritises direct and longer-term business relationships are better able to respond in a crisis by continually re-adjusting strategies for coping that are acceptable to both parties.
The global pandemic affects everyone, but none have been harder hit than low-wage workers. These workers should not be forced to make the brutal choice between their health and their livelihood.
Brands bear responsibility to support garment manufacturers and ensure the safety of workers and their families. This support needs to go beyond well-meaning guidance documents to offer practical, collaborative assistance that carefully balances safety concerns and economic opportunities. Leaving suppliers to carry the burden of a growing list of safety requirements should not be an option for brands that have committed to partnerships with suppliers and to respecting human rights.