The media is currently awash with predictions that the Covid-19 outbreak marks the end of multinational sourcing. Professional clothing buyers certainly need to review how they source – but it’s resilience, not re-shoring, they should be seeking.
A month ago, I predicted that by Easter, China’s Covid-19 outbreak would be petering out. That seems to be justified.
- The number of new cases a day in China has fallen from 2,500 in mid-February to below 50.
- On 3 March, Apple phone assembler Foxconn (China’s largest private-sector employer) announced it expected full production to be resumed by the end of March – with all staff back at work.
Since then, though, the clothing industry has hit two other important hurdles.
- The spread of Covid-19 outside China. On 10 March, China accounted for about 20 of the world’s 4,000 new Covid-19 cases that day. But per head of population, Italy has had over three times more cases – and more Covid-19 related deaths – than China.
- Global disruption from preventive measures. Thousands of cruise passengers stranded on ships that can’t dock, Italy’s entire population in quarantine, sports events cancelled, stock and commodity markets collapsing.
That disruption isn’t the direct effect of the virus itself, but of the measures governments have taken to contain it. They’re working: around 4,500 people have died from Covid-19 so far this year, while approximately 21 million have died of something else.
Mini-plagues: the curse of the 21st century?
Since 2000, SARS, H5N1 Avian Flu, Zika virus, Middle East Respiratory Syndrome (MERS), H1N1 (swine flu) and Covid-19 have each emerged, travelled round the world, and killed thousands, or tens of thousands, of people.
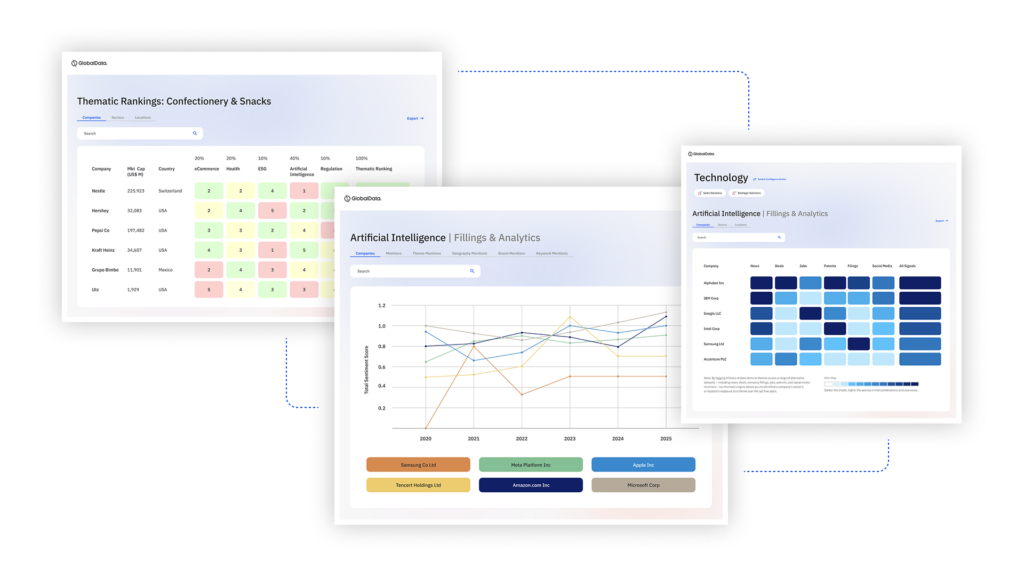
US Tariffs are shifting - will you react or anticipate?
Don’t let policy changes catch you off guard. Stay proactive with real-time data and expert analysis.
By GlobalDataThey have been more frequent than the monster plagues of the past century. But the 1968 Hong Kong flu (at least 1m deaths) killed far more people than all the 21st Century’s mini-plagues combined. This in turn was dwarfed by the Spanish flu of 1918 (25-50m deaths) and Asian flu in 1957 (2m deaths).
Poor countries making more of the world’s manufactured goods aren’t causing these epidemics: they result from the world’s growing connectedness about more than shared kitten Instagrams. They are also harming fewer people because strategies to deal with them have been developed even if drugs to cure them haven’t. We rely on countries enforcing strict containment measures – and on victims’ own immune systems, which are in much better shape today than a century ago.
Experts seem always to err on the side of exaggeration when estimating the severity of mini-plagues. The UK’s chief medical officer predicted the 2009 H1N1 virus (swine flu) would cause a minimum of 3,500 UK deaths – but in the worst likely case, possibly 65,000. Most authorities now agree “just” 210 people died of it in the UK, and around 12,000 in the US.
Shouldn’t we be making things at home?
With most production for Western markets now moved to Asia, each new mini-plague has been accompanied by claims there would be far less disruption if we abandoned complex supply chains and brought production home.
Not a practical proposition in the near future: there simply isn’t the manufacturing capacity or trained workforce in any Western country. But shouldn’t businesses or governments start planning to repatriate production? In my view, this is the wrong question:
- Relative to its population, the developed world’s largest clothing industry is in Italy. Where at this moment, Covid-19 has killed more of the population than anywhere else (7.6 deaths per million people compared to China’s 2.4).
- By value of garments produced, the developed world’s largest clothing industry is in the US – where no-one has the faintest idea how widespread Covid-19 might become. The State governors in New York and California (the country’s two major garment production centres) have been forced to declare states of emergency, while the President seems more interested in publicly demeaning the country’s health professionals than providing leadership in fighting a killer disease
- Meanwhile, the world’s major non-Chinese clothing production centres outside China, like Bangladesh and Vietnam, appear to be almost unaffected, while daily life in the US, Japan and Western Europe is close to being put on hold.
We’re only three months into Covid-19. But already there’s evidence its growth in Japan and South Korea might be slowing as fast as it is in China, and growth in Europe looks likely to slow in a similar way very soon. But we won’t know until we’ve seen:
- The timing and extent of the epidemic’s progress in Europe.
- The path the virus will take in the US and the rest of Asia: the first cases in Vietnam and Bangladesh are now being reported.
- The spill-over into the global economy and daily life.
- Whether the virus will evolve into something more deadly or tougher to contain.
What’s certainly clear, though, is that many affluent countries are going to be as badly hit by this virus as China – and in some cases hit a lot worse. The knee-jerk reaction of under-informed pundits to call for more localised production of clothes, electronics and household goods is wrong-headed.
In our industry, Chinese factories make about one-third of the clothes that developed countries consume. Switching orders from China to other foreign countries is tricky (a lot of components come from China) – but easier than switching to local production in Italy, Japan, Korea or (probably soon) the US.
The priority for buyers in an era of mini-plagues isn’t deluding themselves that rich-country manufacturing can somehow be magicked into existence. It’s establishing greater resilience in their sourcing networks, for example, by:
- Avoiding dependence on any one country – including the one hosting their head office.
- Identifying vulnerable parts of their supply system – like component availability – and developing alternative sources.
- Pressurising host governments (including their own) to review and upgrade their contingency planning.
Resilience has rarely featured in supply chain reviews. Now’s the time to start insisting it does.