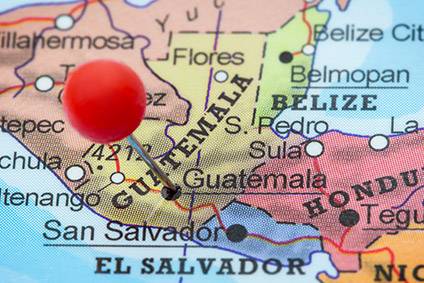
The growing coronavirus epidemic continues to cast a shadow on Central America’s garment export and deliveries, with Nicaragua now forecasting a full-year export decline and Guatemala also acknowledging its apparel shipments face delays.
“We won’t grow that much,” says Dean Garcia, executive director of the Nicaraguan textile and clothing industry association Anitec (Asociación Nicaragüense de la Industria Textil y de Confección), just as the global epidemic’s first Central American case surfaced in Costa Rica.
“If the virus is not contained and we continue to have political instability, we could see [export] declines from zero to minus 5%. Conversely, if the disease becomes more manageable, potentially avoiding a global recession, we may grow up to 5%.”
Garcia notes the rest of Central America, tied into a free-trade corridor with the US under DR-CAFTA, could see losses as US consumers drop apparel purchases in lieu of basic necessities.
The novel coronavirus (Covid-19) has killed over 3,500 people and infected roughly 105,000 globally. In the world’s fashion capital New York, frantic consumers were broadcast panic buying virtually everything except clothing, sending an ominous signal to factories south of the border that a production slowdown is inevitable.
Weakening exports
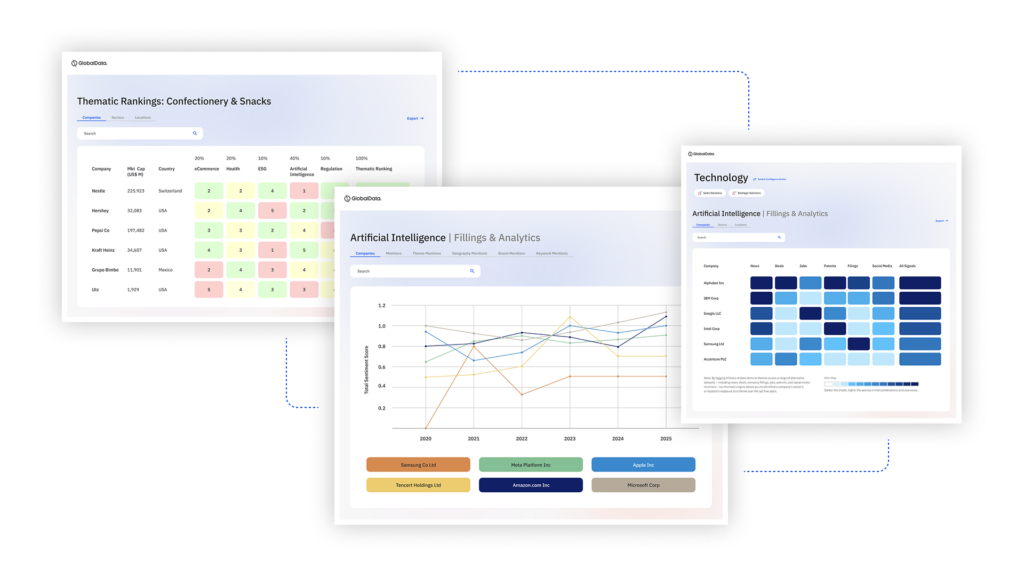
US Tariffs are shifting - will you react or anticipate?
Don’t let policy changes catch you off guard. Stay proactive with real-time data and expert analysis.
By GlobalDataEven before the virus began spreading globally, exports from the region comprising Guatemala, Honduras, El Salvador, Nicaragua, Costa Rica and Dominican Republic were undercutting expectations.
Nicaragua’s garment shipments to the US last year were mixed, after jumping 10% to US$1.8bn in value in 2019 but declining 2% to 700m square metres equivalent (SME) in volume. Falling sourcing contracts from Under Armour and Nike, as well as Levis Strauss’s decision to move its Dockers’ sewing facility to Cambodia and Vietnam amid political volatility, dented the industry’s fortunes.
Guatemala’s US shipments also slipped last year, down 3.08% to US$1.41bn, and declining 6.8% in volume terms to 360m SME. While Honduras and El Salvador saw declines due to political instability, even though US demand remained relatively healthy (up 9.85% to US$2.82bn and down 2.4% to US$1.86bn respectively).
Chinese investment, which has soared in Central and Latin America in the past few years and not just in apparel, will likely decline too, Garcia adds.
Hong Kong-based Texhong Textile Group, one of the world’s top core spun yarn suppliers, is constructing a woven fabric factory in Nicaragua’s capital city Managua, as well as working to modernise a fabric dyeing and finishing facility it bought from an unnamed Taiwanese firm. Further projects include plans for a yarn spinning site in the complex, as well as another yarn and denim production plant to be erected in 2021. The final phase could see the Chinese firm build a sewing facility, but its schedule and completion will depend on market demand.
Several other Chinese players are also understood to have been looking to put capital to work in Guatemala, but it remains unclear whether those commitments materialised, observers say.
Guatemalan postponements
The coronavirus, which is rattling both ends of the global supply chain as it hits major consumer markets in the US – where over 500 cases and 21 deaths forced New York to declare a state of emergency over the weekend – and garment factories in China, is also hurting makers in Guatemala.
Alejandro Ceballos, president of the country’s apparel and textile industry association Vestex (Asociación de la industria del Vestuario y Textiles), says feedstock shortages could lead to delays on up to 70% of apparel shipments within the next 30 days.
“This is getting very serious,” he warns, adding that the situation seems more critical in Guatemala than in other regional producers. Clothing containers to US brands such as Walmart, Target, Gap or Macy’s could be late 20% this week, 40% next and up to 70% in a month, he adds, calling for American customers to incorporate more flexible sourcing policies to help the country’s producers cope with the crisis.
“All factories we talk to are having problems,” Ceballos says. “They are missing product labels, yarn, thread, buttons and dyes, etc.”
Factory owners are also worried about a growing dearth of machinery parts sitting at Chinese ports – a major issue if a plant suddenly needs a key, faulty component, to keep lines operating smoothly.
Worker shortage concerns
Meanwhile, China’s factories remain largely understaffed as many operators have been unable to return to their posts due to transport restrictions, according to Vestex.
Specifically, 54% of manufacturers say less than 50% of workers have returned to posts, according to a recent survey of 294 firms by the China Garment Association. The lack of workers is even more of a problem for small companies, 80% of which have 50% of workers that have not returned.
Over 68% of garment manufacturers have resumed production and expect output to reach 50% capacity later this month, completely recovering by April if the situation stabilises, the survey adds.
Mobility issues are also springing up elsewhere. VF Corp, which makes garments in Guatemala for US sale, is reported to have banned employees from travelling to the country, fuelling new logistics challenges. Amid the growing chaos, Guatemala may be forced to cancel its annual Apparel Sourcing Show, which typically takes place in spring, Ceballos notes. VF Corp representatives did not return messages seeking comment.
Honduras claims no impact
In Honduras, executives insist the crisis has not yet hit its shores, even though Central America’s supply chain has become increasingly integrated.
“There are no delays, at least not until now,” claims Guillermo Matamoros, president of Hondura’s Maquila Association (AHM). He adds that the largest T-shirt supplier to the US relies on its cotton and synthetic fabrics – of which it buys around $1bn annually – to send back apparel north of the border.
“Guatemala has yarn spinning facilities. We don’t have that much of that,” Matamoros says, adding that the main textiles centre located in San Pedro Sula purchases yarn directly from US suppliers to meet DR-CAFTA origin rules.
Matamoros says the sector is “monitoring the situation” and that garment investments should total $400m this year – a target some economists and observers say looks overly optimistic.
The industry seems to be getting things done, at least when viewed by this month’s inauguration of the San Juan Innovation Park in San Pedro Sula on the Caribbean coast.
Boasting a $240m initial investment, the facility will house a cotton yarn and blends spinning site, a textiles factory and a 57MW energy plant, according to reports. Eventually it is expected to attract investments worth $600-$700m and generate 15,000 jobs, AHM executives claimed during a presentation, without providing output targets.
NCTO to hold meetings
To tackle the negative impact of the coronavirus on US and Central American supply chains, the US-based National Council of Textile Organizations (NCTO) has summoned Central American industry leaders and top executives for a meeting later this month.
One coping strategy under discussion is having US cotton and yarn makers sharply boost production, but at prices Central American producers can afford.
“We need to look at how they can reconvert and produce more and at what price,” says Garcia, adding that US feedstock prices are at least 40% higher than China’s.
Even though Nicaragua, which churns out apparel for the likes of Under Armour, Adidas or Walt Disney, relies on polyester fabric purchases from China, it has enough reserve stocks to offset current shortages, Garcia claims. The nation imports less cotton fabric to make knits than its Guatemala or other Central American neighbours, he adds. The bulk of Nicaragua’s key woven and twill fabric inputs also come from Cambodia, Pakistan and Singapore, he adds.
Brazilian makers take orders
In South America, where US and European labels rely on Colombia, Peru and Brazil to make apparel, executives also insist Covid-19 has not yet hit their manufacturing sectors. Fernando Pimentel, president at the Brazilian Association of Textile and Clothing Industry (ABIT), reiterates that Brazilian exporters are not delaying product shipments. “We don’t have raw material shortages,” he says. “But if this crisis continues, we could start seeing problems in two or three months.”
An ABIT insider adds global brands are rushing to enquire about sourcing opportunities in the country, which can step up output of high-end fabrics such as synthetic yarn or polyester to help fashion labels replace missing Chinese product, albeit at a much higher cost.
Shipments will be late
Ilse Metchek, president of the California Fashion Association, says that despite country and brand efforts to paint a brighter picture of the virus’s impact, “there are going to be delays, no question. And we will have a very difficult back-to-school season, at least in the US,” where she notes brands are working to figure out how and from where they will fill next year’s clothing racks amid the disruptions in China where major sourcing fairs have been cancelled.
She adds, however, that South and Central American supply chains should be able to replace China’s gap. “Clothing can easily be shifted to South America and other countries,” Metchek notes, adding that Colombia, for instance, has a great denim offer. US yarn and cotton producers are already moving to supply Central America with the fabric it needs to finish assembling garments.
Return to natural fabrics
The health crisis could also provide a boon for makers of natural fabrics such as cotton, linen and silk as their products are seeing rising demand from firms looking for alternatives to China’s synthetic feedstocks.
Echoing similar views, Metchek says Covid-19 should provide a valuable lesson to US and global brands that diversifying their sourcing is paramount. “We have been lazy because China has been easy,” Metchek remarks. “They understand our tech packs and quality. We have taught them for 30 years.”
California fashion labels are working to figure out “what do we do now and what do we do next year,” according to Metchek. “There is definitely a lesson here about not putting all your eggs in one basket.”
See also:
- Central America makers face delays due to coronavirus
- Is coronavirus a threat to the clothing industry?