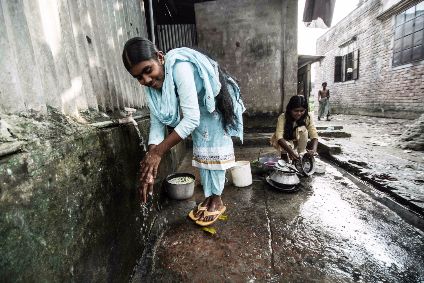
Many fashion brands and retailers have codes of conducts that their suppliers should follow – yet one of the key areas that needs urgent reform is how they do business across their supply chains, a new report asserts.
Brands that put relentless pressure on suppliers to drive down prices or produce faster, without taking into account the cost of social and labor compliance, or the capacity of a factory to produce within short periods, drive labour abuses in factories, according to research from Human Rights Watch.
Its report ‘Paying for a Bus Ticket and Expecting to fly: How Apparel Brand Purchasing Practices Drive Labour Abuses‘ has been released to coincide with the sixth anniversary of the Rana Plaza tragedy in Bangladesh, where an eight-story building collapsed on the outskirts of Dhaka, killing 1,138 workers and injuring over 2,000.
It suggests that pressure on suppliers to drive down prices or produce faster are among the biggest issues.
“Apparel brands typically have their products made in a broad array of factories across multiple countries,” explains Aruna Kashyap, senior counsel, women’s rights division at HRW. “This makes their efforts to monitor conditions in those factories inherently daunting and complicated. Complex purchasing decisions underpin the production of every branded product. Every one of these decisions can have an impact – positive or negative – on how suppliers treat their workers.
“Factories respond to poor practices by clothing brands with abusive cost-cutting methods, including illicit subcontracts with facilities with rampant workplace abuses. The other abuses include wage violations, requiring workers to work faster and without adequate breaks, and dangerous or unhealthy work conditions.”
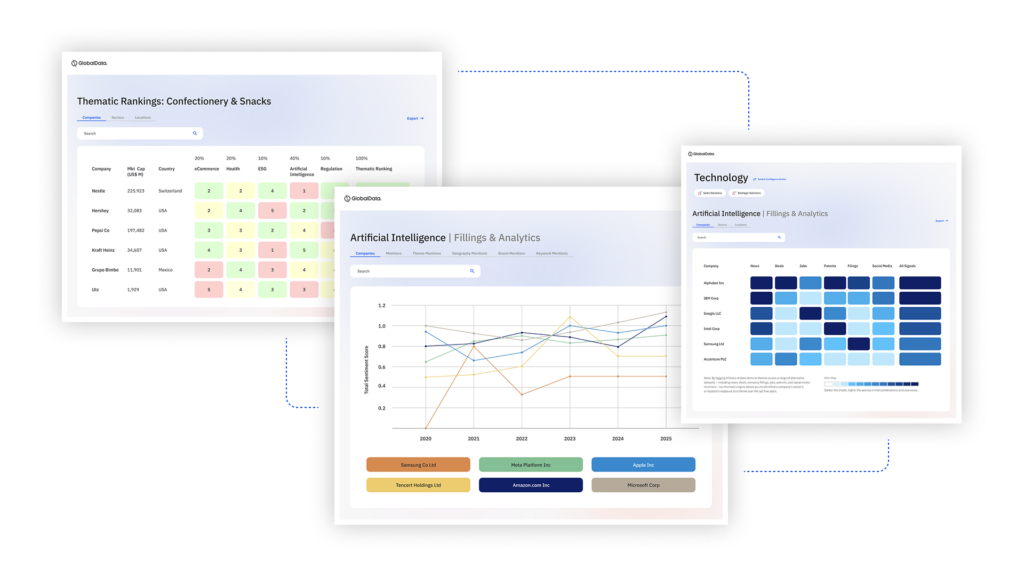
US Tariffs are shifting - will you react or anticipate?
Don’t let policy changes catch you off guard. Stay proactive with real-time data and expert analysis.
By GlobalDataThe report interviewed workers in Bangladesh, Cambodia, India, Myanmar and Pakistan as well as garment suppliers from South and Southeast Asia.
One worker described the atmosphere in the factory she works at as “jail-like” with pressure to produce faster leading to bathroom break bans and a half-hour break as opposed to the full hour she is supposed to get.
A supplier told interviewers they are getting pushed more and more to reduce our lead times. “Sometimes we have to confirm some short lead times without any security [buffer] in sight or any tolerance by the brand. If we don’t agree to the lead times, we might lose the order.”
HRW points out that changing market demands now require clothing brands to produce and sell goods faster than ever. But they risk fuelling labour abuses if they shrink the time available to workers to make their products without adequately monitoring the factory’s capacity or giving workers enough time that factors in national holidays and weekly rest days.
“Brands that do not have written contracts, or use one-sided contracts without allowing for flexible delivery dates and waiving financial penalties in cases where brands contribute to delays, significantly heighten risks to workers. Where contracts are one-sided, brands seek to transfer the costs of their own mistakes entirely to factories, heightening the use of abusive cost-cutting methods by factories.
“Companies that do not pay their suppliers on time risk delays for workers in receiving their wages and benefits, and hamper factories’ abilities to take loans to finance fire and building safety measures.”
The report highlights some of the key factors fuelling labour abuses in factory and threatening worker safety. These include not only a “dramatic shrinking” of lead times, but also brands delaying a factory’s ability to start bulk production without readjusting delivery dates – which put additional pressure on the factory – and penalties and costs imposed on suppliers that miss deadlines, as well as delayed payments.
It says brands, stakeholders and governments can take steps to correct poor purchasing practices and mitigate the risks of supply chain abuses.
Recommendations for apparel brands
- Take steps to map out the supply chain, consolidate the tail end of the supply chain, ensure full visibility over supplier factories, and publish a list of these in accordance with the Transparency Pledge [a minimum standard developed in 2016 by a coalition of labour and human rights organisations].
- Evaluate the use of buying agents and put in place additional due diligence mechanisms tailored to monitoring buying agents.
- Create and publish a policy on responsible purchasing practices in consultation with relevant stakeholders and aligned with UN Guiding Principles on Business and Human Rights and the OECD Guidance on Due Diligence on Responsible Supply Chains in the Garment and Footwear Sector. Embed the policy within all departments of the brand through job descriptions, performance assessments, incentives, training programs, and periodically report progress on adherence. In particular, integrate key performance indicators (KPIs) regarding social and labour compliance, especially adherence to workers’ freedom of association and collective bargaining agreements, into the overall assessment framework of sourcing teams.
- Institute contractual reform to develop fair purchasing agreements as part of the company’s efforts to prevent and mitigate labour rights risks to workers from unfair purchasing practices. These agreements should explicitly account for the costs of labour and of broader human rights compliance.
- Integrate suppliers’ anonymous feedback on purchasing practices through third-party surveys like Better Buying to improve accuracy of data by mitigating suppliers’ fear of providing feedback; seek customised individual brand reports to monitor and rectify purchasing practices; and disclose periodic progress by summarising the rankings received through Better Buying Purchasing Practices Index scores over time.
- Join initiatives that combine collective brand reform on purchasing practices with sectoral collective bargaining like the Action, Collaboration, and Transformation (ACT). Until such initiatives conclude collective bargaining agreements and costing models, supplement joining them with at least the following measures: Ensure that prices explicitly factor in labour costs and encourage suppliers to use country-specific labour costing tools like those being developed by the Fair Wear Foundation; Publicly report on the number of collective bargaining agreements in supplier factories (especially where there are no sectoral agreements), the impact of such agreements on factory working conditions, and how brand purchasing practices incentivise adherence to such collective bargaining agreements.
Recommendations for multi-stakeholder and industry initiatives
- Make publishing supplier factories in accordance with the Transparency Pledge a mandatory condition of membership.
- Encourage member brands to seek anonymous feedback through supplier surveys like Better Buying survey reports tailored to them and disclose the summary of the scores publicly.
- Encourage member brands to join collective initiatives like the ACT Initiative in its priority countries and take other interim measures until ACT Initiative’s industry-wide collective bargaining agreements are negotiated and have demonstrable impact.
- Develop a set of key indicators on purchasing practices that informs monitoring efforts to assess brand purchasing practices and publicly report progress using these indicators. These indicators should be developed in consultation with industry experts, unions, labour advocates, and draw on the OECD Due Diligence Guidance on Garments and indicators developed by the NYU Stern Center for Business and Human Rights and the Fair Wear Foundation.
Recommendations for governments
- Develop legislation requiring mandatory global supply chain human rights due diligence by companies, including their sourcing and purchasing practices.
- Ensure that all public procurement integrates mandatory human rights due diligence measures, including on sourcing and purchasing practices.
- Ratify all ILO core labour conventions and reform labour laws to fully comply with these international labour standards.
- Governments of apparel producing countries should publicly and regularly disclose (e.g. every four months) the number of factories inspected, key labour rights violations found, and enforcement actions taken. The terms of disclosure should be finalised in consultation with various actors, including labour rights advocates, independent unions, and the ILO.