
Best-known as one of the world’s leading suppliers of narrow fabrics and elastics for end-uses including lingerie, intimate apparel, sports and activewear, Stretchline is joining the fight against coronavirus by switching its production to elastics that can be used in medical face masks.
The global fashion industry has seen dramatic changes in recent months as the global coronavirus outbreak causes chaos throughout retail markets and their supply chains.
But as clothing sales have plummeted, demand for personal protective equipment (PPE) including face masks has surged as citizens and healthcare workers try to protect themselves. Fashion companies from H&M and Zara to sportswear brands like Nike, and luxury firms including LVMH Kering have all pitched in by offering to share their expertise and production facilities to make masks, which are in short supply.
Joining the charge is Stretchline, a manufacturer of elastic to the global clothing industry, with clients from Victoria’s Secret to Nike.
The company operates out of three factories in the UK and has other factories in China, Sri Lanka, Indonesia, Mexico, Honduras and North America. In a normal – pre-Covid-19 – year, Stretchline produces on average 1.2bn metres across all of its locations, with China alone producing 250m metres.
Barry Head, European sales and marketing director for Stretchline Holdings, explains that at the start of the outbreak, the company’s China production was halted for more than four weeks as part of enforced shut-downs to try to contain the spread of the virus.
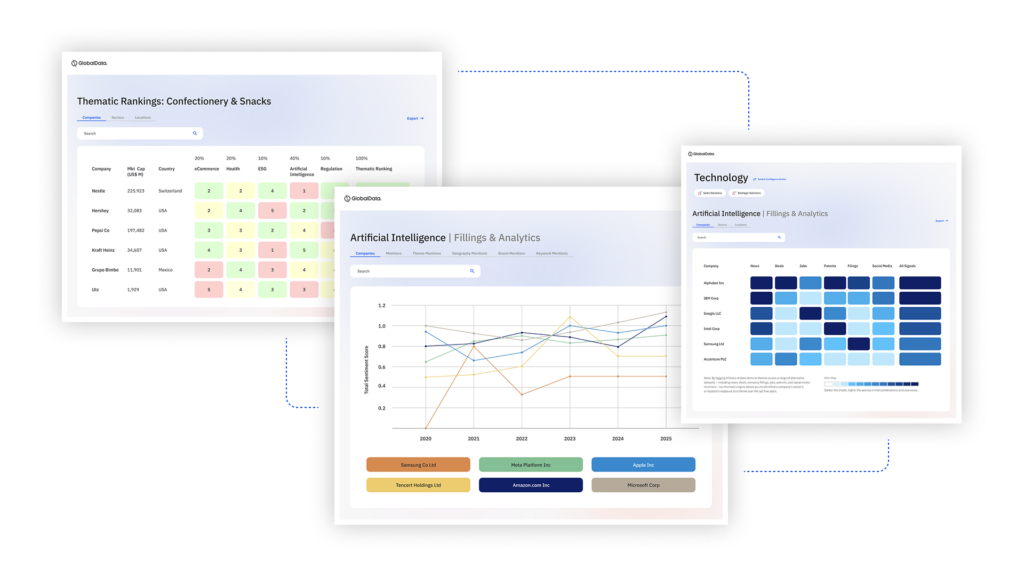
US Tariffs are shifting - will you react or anticipate?
Don’t let policy changes catch you off guard. Stay proactive with real-time data and expert analysis.
By GlobalDataStaff were then gradually permitted to return to work; but just one staff member for one hour a day.
“Thankfully things are returning to some sense of normal there now. We’re being told the factories are running at around 80% capacity,” says Head.
“We’re just doing our bit in the fight against the virus. It’s helpful to have something to produce when the regular business has slowed”
One of the group’s advantages is that it operates out of multiple locations – so with China temporarily down, production could still take place elsewhere. “Stretchline being global [meant] we could redirect orders to Sri Lanka, Indonesia and so on.”
With Covid-19 spreading rapidly across the world, Stretchline’s other locations are now being impacted by temporary shutdowns. Additionally, the group has seen orders cancelled “left, right and centre” as brands and retailers in North America and Europe try to overcome falling shopper footfall, store closures and mountains of unsold stock.
So like many in the sector it is switching its focus to help in the production of personal protective gear including face masks, which are in short supply as demand has spiked.
With elastic a key component, Stretchline’s China factory has in recent weeks received an order of 4m metres of elastic solely for use in medical face masks.
The elastic used in face masks is often of a much narrower width compared to those in garment use. The shift in requirements does not mean machinery needs to be changed or upgraded in any way, nor do workers need to be trained specifically for this type of production. It simply is a realigning of yarns to the ones for mask elastic production.
“It takes around three to four days to set up [the machines] and then they can be running again.”
In terms of raw materials, the UK facilities are supplied with yarns from Europe – predominantly Italy – while the South East Asia locations are supplied by China.
“We’ve not seen a real issue in terms of raw material delays as yet,” says Head.
But while the China factories are back up-and-running for yarn production, many of the receiving facilities in other global locations that produce the elastic have been closed on government direction, which could result in some delays.
“We are getting requests for 100,000 metres tomorrow…It’s just not do-able because we don’t have the stock.From a logistics point of view, Head says much of the company’s elastic is in stock and a lot is on the water. The challenge for Stretchline is that while most of the elastic it produces is on a made-to-order basis, the fast-moving nature of the Covid-19 situation means elastic is needed far more urgently.
“Manufacturing something like knicker-pack elastics, we make great stocks of those as you know the orders will continue, and then when the order comes in you just dye to match. Something like face mask elastic, we don’t keep a lot of stock of.”
Head says the production of face mask elastic has been done at cost or just above cost. He believes it is the same situation for many of the companies that have been tasked with actually producing the masks.
“We’re just doing our bit in the fight against the virus,” he says. “Many of the governments in most locations have called upon the industry to help in producing face masks. I don’t think it will in any way help them recover the loss of their mainstay business,” he asserts. “But for many, like us, it’s just helpful to have something to produce when their regular business has slowed.”
Click here for additional insight on the coronavirus outbreak: How coronavirus is impacting the global clothing industry