Shifting skill sets due to the introduction of advanced technologies, the misperception of manufacturing jobs, and the retirement of baby boomers have all combined to create a widening skills gap in the American manufacturing industry, a new survey has found.
The search for skilled talent – ranked as the number one driver of manufacturing competitiveness by global manufacturing executives – appears to be at a critical level, according to the latest skills gap study by Deloitte and The Manufacturing Institute. It reveals that an unprecedented majority (89%) of executives agree there is a talent shortage in the US manufacturing sector – 5% higher than in 2015.
As recently as August 2018, there were 508,000 open jobs in US manufacturing, part of the best annual job sector gain in more than 20 years. But while the job gains are positive indications the industry continues to recover from the Great Recession and reflect strong production levels, Deloitte believes this also means that finding talent with the right skills to fill the open jobs could reach crisis proportions.
Based on the analysis, US manufacturing employment will grow at an average rate of 1.5% per year by 2028. This implies that as a baseline, the sector would need to employ around 1.96m additional workers between 2017 and 2028 to produce the goods the growing economy could demand.
However, the lack of skills identified by manufacturing industry executives and impending retirements suggest the reality instead will be employment bottlenecks, leading to a potential 2.4m jobs going unfilled, with the risk of limiting production below these projections. By 2028, in the base case, the report estimates that additional manufacturing value added of US$454bn could be at risk if qualified workers cannot be found to fill the open jobs, which could account for about 17% of the total US forecasted manufacturing GDP of $2.67trn.
Advanced technology and automation
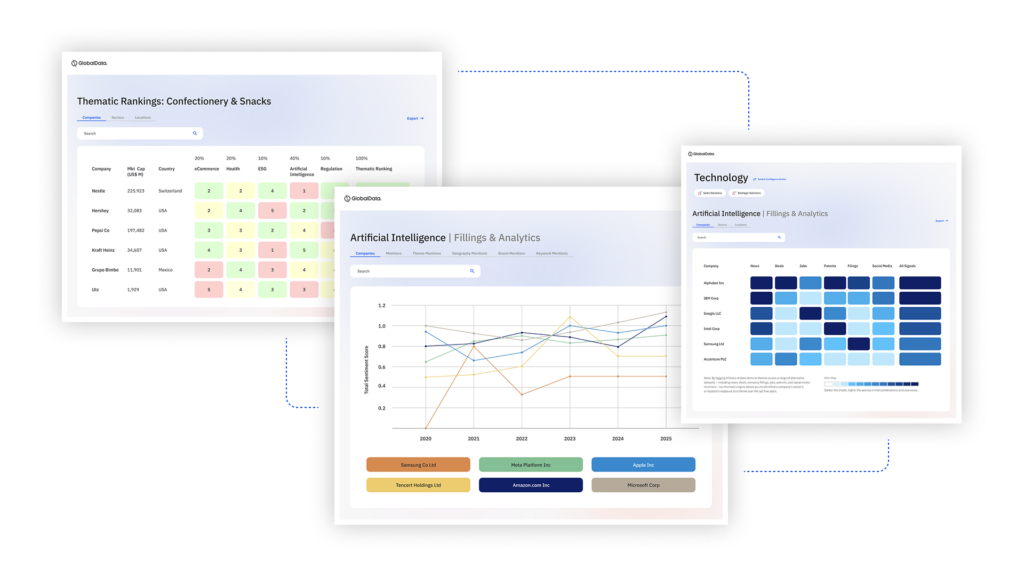
US Tariffs are shifting - will you react or anticipate?
Don’t let policy changes catch you off guard. Stay proactive with real-time data and expert analysis.
By GlobalDataThe study reveals that most manufacturers believe that the number one cause of the skills shortage is the shifting skill set due to the introduction of new advanced technology and automation.
Half of the manufacturers in the study say they have already adopted technologies such as robots, cobots, machine learning, and artificial intelligence (AI). In the presence of increased human-machine teaming and access to insights surfaced via the Internet of Things (IoT), the types of skills that employees need to possess are rapidly evolving, and it seems increasingly difficult for the workforce to keep pace.
“Today, the early stages of digital transformation seem to already be creating a mismatch between the available workers and the skills necessary to fill open jobs,” the report notes. “Increasingly, employers are looking for extended computer skills that enable core production workers to program a CNC (computer numeric control) machine for a new job, or interact with CAD/CAM (computer-aided design/computer-aided manufacturing) and other engineering or manufacturing software.”
According to the report, many manufacturers find themselves forced to take more aggressive measures to fill open jobs in the short term. The 2018 study identified a 15% increase in the number of companies offering higher pay to skilled workers compared with 2015.
Today, 83% of executives offer higher pay to attract and/or retain skilled workers. But, on the flip side, while this gets skilled workers in the door, it does not guarantee they will stay. In fact, the study shows that 66% of executives see skilled workers leave to accept outside positions that offer higher pay. In addition to higher pay and signing bonuses, some manufacturers have also relaxed certain hiring requirements and moved production to domestic job shops to keep pace with the rising orders many are seeing. Unfortunately, Deloitte believes none of these approaches will likely solve the industry’s skills shortage in the longer term.
The report suggests a number of strategic approaches manufacturers could take to address the expected skills gap:
- Taking advantage of the emerging workforce ecosystem. The traditional employer-employee relationship is being replaced by the emergence of a diverse workforce ecosystem – a varied portfolio of employees, talent networks, gig workers, and service providers that offers employers flexibility, capabilities, and the potential for exploring different economic models in sourcing talent.
- Turning towards automation to supplement human jobs. In its future of jobs report, the World Economic Forum highlighted that by 2022, machines and algorithms will contribute 42% of total task hours, compared to 29% in 2018. Initially thought to present a danger to human jobs by replacing them, many manufacturers today are turning toward automation to supplement the low-skilled jobs they cannot fill and instead focus their existing workers on jobs that are either higher skilled or require uniquely human skills.
- Tapping into the resources from the retiring generation of baby boomers. Manufacturers should think carefully about the potential impact a wave of retirements could have on their organisation and seize any opportunities to hold on to their proven, committed, and experienced workforce and leverage them as a competitive advantage.
- Developing in-house training that engages a multi-generation workforce. Manufacturers should consider increasing investment in training programmes and integrating digital technologies to add relevance, helping employees move ahead on the digital curve.
- Creating public-private partnerships. Only two in ten manufacturers indicated they partner with government and just over three in ten indicated they partner with private education/ training institutes to train their workforce. The path forward includes manufacturing organisations forging long-term partnerships with public education, industry associations, and agencies to develop programems that build a strong connection with the industry, creating a skilled talent pool for tomorrow’s manufacturing environment.
- Bolstering apprenticeship programmes. Exposure to a skilled trade through an apprenticeship has shown to be a promising pathway for filling many of the skilled jobs that lie open in the manufacturing industry. The government and manufacturers together can fund such education and apprenticeship programmes to develop a job-ready stream of qualified workers.