Pakistan fashion brand Khaadi says it has eliminated paper pattern-making from product design and development after implementing technology solutions from fashion technology provider Tukatech.
The company, which is based in Karachi, operates a team of about 60 fashion and textile designers who use TUKAcad for digital pattern-making, grading, and marker-making; TUKA3D for virtual sample-making; and TUKAcloud for web-based design collaboration and communication.
Discover B2B Marketing That Performs
Combine business intelligence and editorial excellence to reach engaged professionals across 36 leading media platforms.
Prior to the implementation, the Khaadi design team worked manually, drafting patterns by hand on paper and assessed design and fit with physical samples.
“There was a lot of human error. When it went into production, we saw a lot of fit and grading issues,” explains Saira Shamoon, chief design officer for Khaadi.
With a vision to expand Khaadi into new global markets, the IT team also saw a need for more robust infrastructure in the design department.
“Growing globally requires scalability,” says Rehan Qadri, Khaadi’s chief technology officer. “Scalability requires lower lead times, higher levels of technology, and higher levels of automation.”
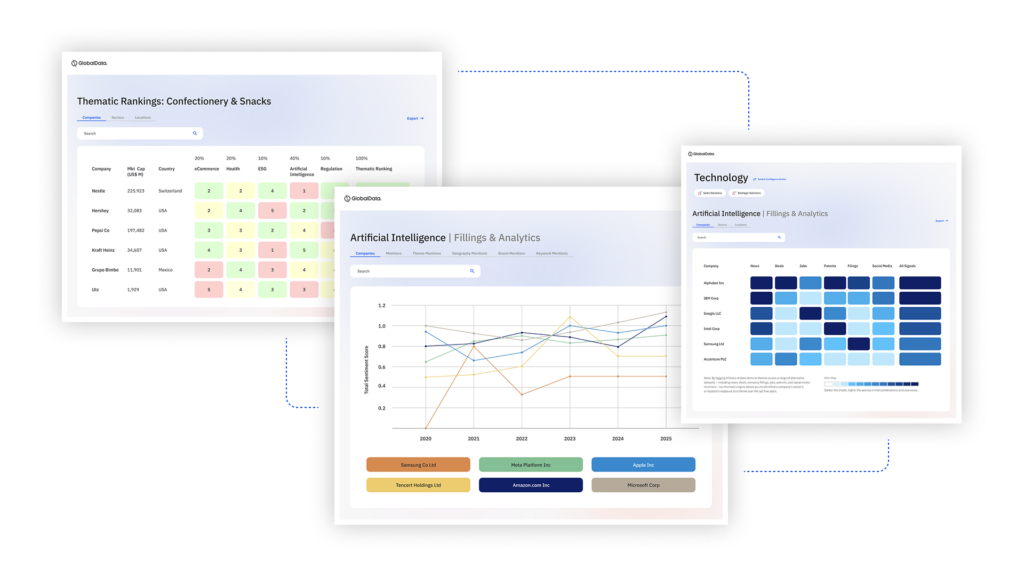
US Tariffs are shifting - will you react or anticipate?
Don’t let policy changes catch you off guard. Stay proactive with real-time data and expert analysis.
By GlobalDataAs a result, Khaadi initiated a digital transformation in its design studio in a move which now sees fashion designers work from graded digital pattern blocks in TUKAcad.
This frees them to make style line changes without disturbing the fit as every style comes from the same blocks, meaning fit is more consistent between styles. In addition, fashion designers simulate their styles in TUKA3D which enables them to understand how each garment will drape and fit with real-time motion simulation.
The draped silhouettes become like digital “blanks” for Khaadi’s textile designers to visualise their artwork, with repeats, placement prints, and embroideries arranged on the 3D sample, allowing each department to review the full collection digitally on TUKAcloud, before any physical samples are made.
Since design evaluations now happen virtually, the team makes decisions quickly without wasting resources.
“We’ve reduced the army of people we had to hire to do pattern-making, cutting, sewing, printing, and embroidery just to see a sample,” Shamoon says.