Subscribe to Just Style for just £1 for 1 month
Stay ahead with unbiased news, expert commentary, and in-depth features on global topics.
As a trusted provider of data and insights, Just Style collaborates closely with industry leaders and professionals to offer unique thought leadership and analysis. Gain a deeper understanding of the apparel industry’s trajectory and the priorities shaping the profession.
Ready to stay informed?
Subscribe to unlock exclusive content.
Already a subscriber? Sign in to access your account.
Pleasecomplete this form to request more information, and a representative will be in touch shortly.
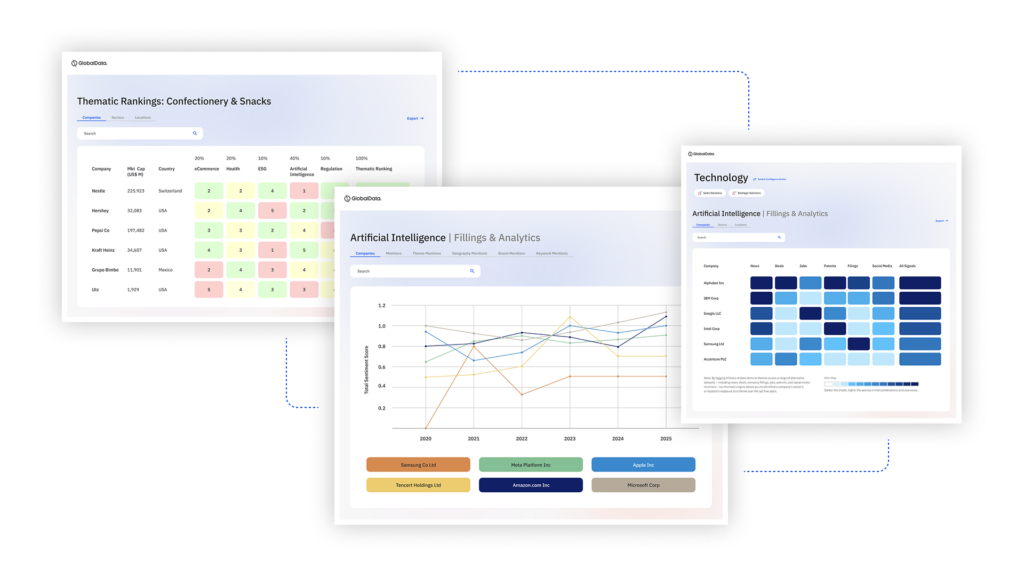
GlobalData Strategic Intelligence
US Tariffs are shifting - will you react or anticipate?
Don’t let policy changes catch you off guard. Stay proactive with real-time data and expert analysis.
By GlobalData