Ease of use, reliability, durability and,of course, increased productivity are all driving developments in sewing machinery. Inthis special feature we look at some of the latest innovations coming on to the market.
Automated Jeans production
Mitsubishi Electric Europe BV, the Hertfordshire based electronics giant, has released twonew machines designed to automate the production of jeans back pockets and labels. Themachines are the latest in a stream of innovations that the company has introduced for thejeans market, and both utilise the Mitsubishi PLK-B 1006.
In the first case the PLK-B 1006 CET, adevelopment of an earlier model with a sewing area of 100mm x 60mm, has been adapted toautomate the sewing of jeans labels. And although it still uses an automated sewingprogramme to fix the label to the garment, the company has now added a label feeder thatcompletely de-skills the entire operation. As long as the label holder is kept full andthe finished garments are replaced with new ones, there is no sewing skill required.
Paul Braun, department manager atMitsubishi, claims that the machine is capable of 2,400 labels per 8 hour shift. “Theaddition of the label stacker has dramatically improved the performance of this model. Itis already on the production lines of some of the biggest names in jeans and we expect itspopularity to increase”.
The second machine is the Mitsubishi PLK-B1006 BBT-1 which is designed to process both the hemming and embroidery of a jeans backpocket in one operation. It uses the PLK-B1006 to first apply the embroidery pattern andthen automatically move the piece to the next sewing head which completes the hemming.Again, an automated sewing programme is used so that the operator simply has to keep themachine supplied with new cut pieces.
Paul Braun feels that there are numerousadvantages for manufacturers with these new machines. “In addition to the savings inlabour on the hemming operation, there are also improvements in the consistency of qualityand speed of production. Manufacturers have also reported that changes in garmentspecifications can be more easily accommodated as there is no need to re-trainstaff”.
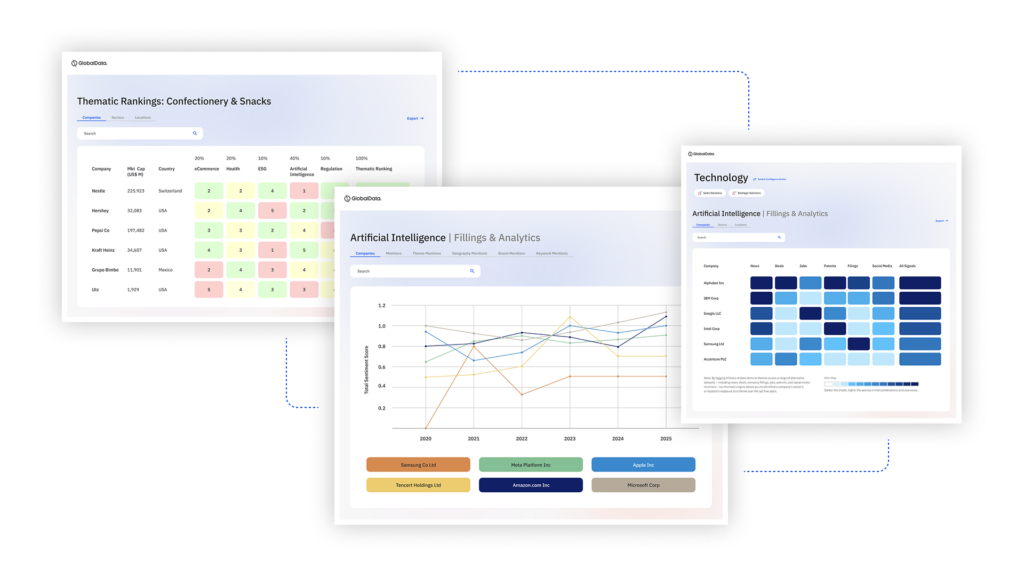
US Tariffs are shifting - will you react or anticipate?
Don’t let policy changes catch you off guard. Stay proactive with real-time data and expert analysis.
By GlobalDataPaul has also hinted at further newmachines for the jeans market which will possibly be released in the autumn, and a seriesof Mitsubishi Roadshows which will bring the new machines within easy reach of customersacross the UK.
Advances in automatic stitching
A century after introducing its first automatic buttonhole stitcher, AMF Reece remains aleading supplier of straight and eyelet-end buttonhole machines. The introduction lastyear of its new S.2000 series straight buttonholer was obviously an important event and,as the successor to the Reece S2 machine, its design is said to depart fundamentally fromtraditional sewing machine engineering in the interests of greater simplicity, reliabilityand productivity.
Several patented features help reduceinertial stresses during high-speed operation, permitting not only higher sewing speedsbut also faster acceleration and deceleration. These improvements are said to combine tomake the S.2000 buttonholer 20 per cent more productive than other models. Other benefitsinclude better feed control; easier and more consistent clamping of the workpiece, withoutadjustment; and the ability to remove each of the 8 major mechanisms separately forservice, without dismantling other parts of the machine.
AMF Reece has also announced theavailability of several new variants of the basic S.2000 buttonholer — notably, thehigh speed S.2000 tacker which now offers manufacturers greater productivity andserviceability.
Another S.2000 variant is the ISBHimitation sleeve buttonholer for jacket and coat sleeves. The fully-programmable newindexer complements the speed and reliability of the basic S.2000 sewing head, and is nowclaimed to be one of the fastest and most affordable machines in its field. A third, soonto be launched variant, the S.2000 CAED cut-after edger, will have wide application forfinishing waistbands, bra straps and the like.
AMF Reece is also introducing a newcord-trim variant of the S.100 eyelet-end buttonholer. With automatic trimming of theunderthreads as well as the top thread, this version is said to be ideal for all fixedlength buttonholing applications, especially for trousers and jeans.
Still in the field of eyelet-endbuttonholing, the S.104-400 buttonholers now feature separate motors for the feed driveand the needle drive. This has made it possible to optimise the sequence of operations,increasing productivity by 10 per cent without increasing operating speed. Eliminating theconventional stop-mechanism has further enhanced the machine’s durability and reliability.
Originally introduced as an ultra-flexiblepatch pocket setting system, the 84-71 Autojig profile stitcher has increasingly been usedfor assembling components of complex shape, such as bow ties and one-piece collars. Thelatest version is equipped with a vacuum table and laser location lamps which assist inpositioning the cloth components more quickly and accurately in the sewing template. Animportant application of the improved machine has been in the assembly of mock two-piececollars for shirts and blouses.
New BAS-300E series
In response to requests from apparel manufacturers throughout the world, Brotherhas refined the basic functions of its BAS-300A series of programmable electronic sewingmachines with the development of the BAS-300E series. This is said to be faster, moreaccurate, and has the ability to create more attractive finishes. The sewing machines inthis new series utilise what is described as “revolutionary new technology” tooffer greater performance and productivity, and higher finished quality, in addition toease of use and reliability.
The series consists of three machines, eachwith different sewing areas, making it possible for manufacturers to select the modelsthat best meet their needs. The BAS-311E is recommended for decorative stitching of breastpockets, one-point pattern embroidery, attaching labels, emblems and buttons, basting, andbar tacking. The BAS-311EL can be used for decorative stitching on jeans hip pockets,breast pockets, and one-point pattern embroidery. And the BAS-326E is for sewing theopenings of slacks pockets, decorative stitching of breast pockets, and attaching labelsand emblems.
The maximum sewing speed has been increasedto 2,500 spm (from a previous speed of 2,000 spm), and the feed time from the end of onesewing operation to the start of the next has been reduced by half. This allows theoperator to move on quickly to the next work-piece and greatly reduces handling time.
Ample stitch capacity means that a patterncontaining up to 20,000 stitches, and a maximum of 100 patterns (360,000 stitches), can bestored on a single disk. The E series can also read embroidery data and up to 50,000stitches can be sewn per pattern.
The range of applications for electroniceyelet buttonholers has now become even greater, and Brother emphasises that ease-of-useis customary with its B980 series. The operator can sew eyelet buttonholes quickly andeasily and is subject to fewer maintenance operations and mechanical adjustments. TheB-980 is available in a variety of different designs and sizes, and 9 different shapes canbe programmed and retrieved at the touch of a button.
Brother’s jeans sewing machine line-uphas been augmented by a new bottom hemmer for jeans — the new DB3-B776 single needlecylinder bed needle feed lockstitcher with thread trimmer. A vertical roller feedmechanism helps to eliminate material slippages, thread tangling, and material puckering.The cylinder bed makes operation easy; the lower shaft cam drive mechanism ensures thatthe thread is trimmed accurately; and because thread trimming is carried out continuously,cycle time is reduced.
Enhanced flexibility andproductivity
Juki’s product range includes the LK 1900 electronic bar tacking machineseries which boasts a sewing speed of 2,700 stitches per minute, according to themanufacturer. Computer-controlled, the LK 1900 has 30 standard swing patterns, adirect-driven machine head, upgraded stop accuracy, and a newly developed high torque,high precision feed mechanism. The feed mechanism also reduces vibration and noise, evenduring high speed operation, ensuring a more comfortable working environment.
The MB 3771/BR-10 hopper feed chainstitchbutton sewer incorporates a newly developed knot-tying mechanism which ties tight, secureknots at the last stitch on the seam. It is claimed that finished seams hardly ever comeundone when sewn on this machine, even if the trailing thread is drawn, furtherguaranteeing high quality seams.
The newly developed APW 196 automaticpocket welt machine is the successor of the APW 240 Series. Equipped with an organisedsplit needle bar which permits flexible setting of welting angles and a turret-type cornerknife which allows quick, single-motion selection and switch over between seven differenttypes, the machine promises enhanced seam quality, flexibility, and productivity. Featuresinclude a machine head which achieves a normal sewing speed of 2,500 spm, automatic cornerlength adjustment, and storage of up to 10 sewing patterns and 5 cycle sewing patterns.
Generally, jeans and chinos have their ownspecific style of hip pockets. Since the finished quality of the pockets is a key featurein the quality of the garments themselves, the pocket setting process is one of the mostimportant in their making-up. The Juki AVP 875 pocket setter automates a series ofprocesses — from folding the creases in the pocket cloth, placing the folded cloth,and setting it onto the garment body, sewing it in place, and stacking the finishedproduct. The pocket setter responds to various kinds of materials, from medium weight to16oz denim, and allows for the easy changeover of pocket patterns and sizes, addingflexibility for small-lot production.
Davis introduces treasure machines
J Davis and Company (Machines) Ltd has been appointed as sole UK distributor forthe Japanese-made Treasure Industrial Sewing Machine range following a visit by thecompany’s president and members of the research and development division to the Davisheadquarters in Tottenham, north London.
For the first time in the UK, managingdirector Peter Davis has introduced the new model BS-1180 bluff edge blindstitch fellingmachine. This has been specifically designed for the UK market following the closecollaboration of the two companies, and the ‘pilot’ machine has undergone rigorous testingin UK factory conditions.
Two sub-classes are available — onefor medium to thick materials and one for lightweight fabrics. It has two independentplungers and the stitching and seams are invisible on the top and underside of thematerial.
The new machine spearheads the range ofblindstitch machines that is available with automatic thread cutting and knee liftdropping devices, as well as a stitch condenser that encompasses all the functionsrequired such as movable cylinder arm, long arm lockstitch and differential feed. Evenmodel BM-500, which is a new compact machine with a built-in motor, incorporates all thesefeatures.
Echoing the quality and robustness of theTreasure brand there is also an extensive line-up of hand operated chainstitch embroiderymachines, where braiding, moss stitch, and tape attaching can all be performed. Disk feedoverseaming machines are available too, in both single and two thread versions, and theycan stitch items ranging from extremely fine furs and skins to heavyweight wetsuits andeven stuffed toys.
Tailormade technology
The broad spectrum of technology from Dürkopp Adler has been individuallytailored to meet the needs of manufacturers of men’s, women’s and boys’ outergarments, shirts and jeans.
Reflecting an increasing requirement formore flexibility even in highly specialised products, the 745-28 F, for example, is apiped-pocket sewing unit that can sew all the pockets of a jacket in cycle — withoutany adjustment.
The company is also meeting the growingdemand for automated production methods from low-wage countries with sewing units andengineered sewing stations that offer interesting alternatives to labour-intensivemanufacturing.
For the production of trousers and skirts,550-2-1 is an optimised sewing station for processing trouser fly pieces. Fitted with anotching device and special feeding equipment, this workplace is specially designed forfelling the left fly piece, felling the right fly lining, and attaching the right flypiece with zipper. All work sequences can be completed without converting the machine. Thecompany estimates that in 8 hours, 500-600 pairs of trousers can be processed.
The 743-461 sewing unit for automatic topstitching of the left fly piece enables the seam end to either lie exactly under the edgeof the waistband or on the waistband itself. The operator positions the material with theaid of laser marking, and all subsequent steps are automated. The fully overlapped workingmethod allows a daily output of approximately 3000 pressed fly pieces.
For jacket and coat production, the 745-24is for the pre-sewing of straight and slanted piped pockets, giving accurate seam lengthsand corner incisions. The additional features of the 745-28A for pre-sewing straight andslanted piped pockets with automatic flap shape recognition mean that once the flap isloaded, the sewing unit adjusts the functions automatically.
Long life reliability
A number of new developments to the company’s product line have been announced by Rimoldi.
The first is the Mizar series, a range ofnew mini cylinder bed machines for 2 or 3 needle interlock stitch (with and without topcover), and single needle chain stitch. A prototype of this innovative machine was shownat IMB in Cologne last June, but it has now been officially launched onto the market. Witha cylinder bed circumference of just 160mm, Mizar is described as the smallest cylinderbed machine currently available. This feature enables small size tubular garments to besewn, and all these models are particularly suitable for children’s wear. All Mizarmechanical characters have been designed to meet the operator’s need for an ergonomicworkplace and the manufacturer’s requirements for reliable and flexible production.With a large area to the right of the needle, and the small area on the left of theneedle, loading and handling of the tubular garments is made as easy as possible.
Another new model is the overlock head withtop feed. This product completes the Vega line-up which was previously unavailable withtop feed. In comparison with the 600 series, the new units have been completely redesignedin terms of mechanical parts, transportation and performance. This new release is aimed atmanufacturers who work with slippery or difficult to feed fabrics yet still requirequality seams.
Together with its new top feed overlockheads, Rimoldi has also updated and upgraded the standard line of Vega safety stitch F29overlock machines. The models now take advantage of a new feeding mechanism which enhancesefficiency even in the most critical sewing conditions and with heavy duty fabrics. Thesemachines can cross over pre-existing seams and fabric of different thickness whilst sewingat maximum speed. For garment manufacturers, this innovative transportation system is saidto improve the efficiency of feeding, facilitates the correct pairing of plies whilesewing, and increases the differential effect.