
China’s clothing and textile makers are struggling to get back on track amid the continuing novel coronavirus epidemic – telling just-style that quarantined workers, travel restrictions and material delays are disrupting production and causing ongoing uncertainty.
For apparel brands and retailers with supply chains linked to China, the implications of the novel coronavirus (now formally known as Covid-19) outbreak continue to reverberate.
Companies with manufacturing operations in the country have told just-style they are closely monitoring developments, are taking steps to tackle production delays, and that their customers have so far been supportive.
Yet they are also resigned to the fact business disruption is inevitable, with signs global supply chains are already facing delays and inventory shortages.
“This will have a major negative impact on our business,” one executive told just-style.
As well as delays of up to two or three months on the delivery of summer fashion collections, there is also the warning of a potential knock-on impact later in the year on autumn, back-to-school and even holiday goods
Concerns are numerous. “Their factories are not in operation, and they won’t have the ability to ship product; they’re not getting raw materials in so there will be delays and they’re going to miss shipments; and they’re not going to be able to send their QCs to visit factories and check out production, so therefore they might see an increase in quality defects because they’re not getting quality inspections.”
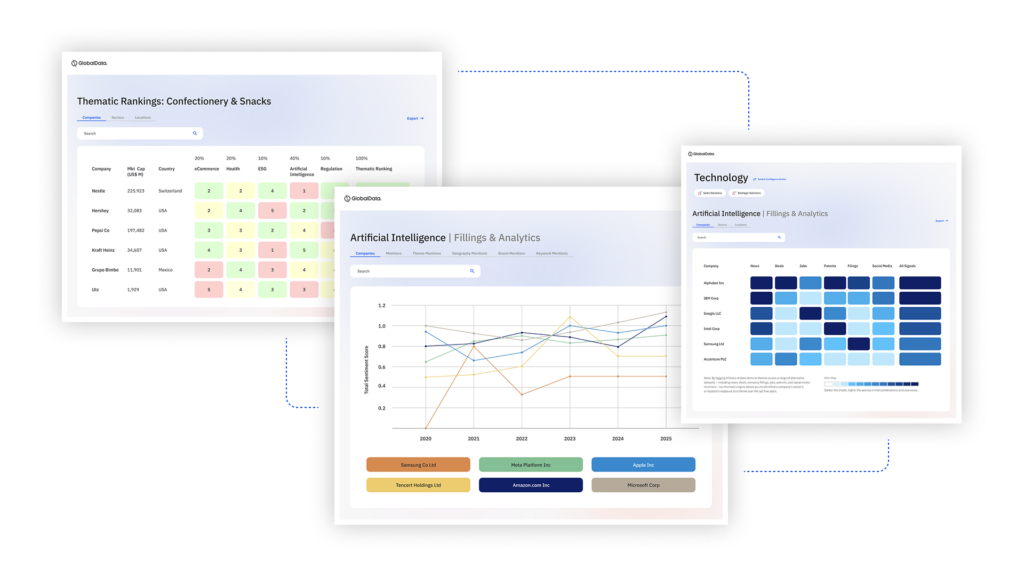
US Tariffs are shifting - will you react or anticipate?
Don’t let policy changes catch you off guard. Stay proactive with real-time data and expert analysis.
By GlobalDataAs well as delays of up to two or three months on the delivery of summer fashion collections, there is also the warning of a potential knock-on impact later in the year on autumn, back-to-school and even holiday goods.
“Christmas might still be a long way off, but the orders have to be placed, which means the samples have to be in…all of these things. So we’re going to have a lot of challenges come May and June where people aren’t able to start production because of all the delays in the months of February through to April.”
And there’s more. “If factories are struggling and they can’t meet the payroll, do they go into bankruptcy? Does it lead to a larger economic recession that will impact consumers in Europe and the United States? That’s the gamut of things that we’re hearing.”
Restarting production
Manufacturers in the world’s second-largest economy have already endured an enforced three-week shut-down over the extended Chinese New Year holiday as part of efforts to contain the spread of the virus.
Restarting stalled production is easier said than done, with strict travel restrictions still in place and precautionary measures to protect workers in crowded environments such as factories
But restarting stalled production is easier said than done, with strict travel restrictions still in place and precautionary measures to protect workers in crowded environments such as factories.
“Local government officials are very cautious about letting people go back to work,” explains Stanley Szeto executive chairman of Hong Kong based fashion supplier Lever Style, whose main hub is in Shenzhen in China.
“My office, for example, was given permission to open only on Friday (14 February), with only 20% of the staff allowed on premise. The second batch will be allowed entry a week later, with a third batch to be allowed entry even later. And staff from Hubei and other lockdown areas have no timetable for returning.”
Not surprisingly, many of the factories that have reopened are operating well below capacity. “Production is starting very slowly,” confirms Szeto, whose business offers end-to-end solutions from design to delivery but does not own production facilities. “Factories have difficulty starting up and getting their staff back from other provinces.”
Even offshore production is not exempt, “because most of these factories make garments using Chinese fabrics and accessories, and these raw materials are not being made nor shipped from China.”
Indeed, while China had a 31.3% share of world apparel exports by value in 2018, many of the raw materials needed in the global supply chain such as textiles, trims, packaging and labels are also likely to come from China.
According to World Trade Organization (WTO) data, 37.6% of world textile exports in 2018 came from China – a record high – with the country supplying almost two-thirds of the textiles used by manufacturers across Southeast Asia.
Cancellations to inbound and outbound air cargo shipments from Europe, the US and the Middle East to China and Hong Kong are also causing havoc to supply lines.
Even offshore production is not exempt, because most of these factories use Chinese fabrics and accessories – and these raw materials are not being made nor shipped from China
“We have tailoring fabrics supposed to be air-freighted from Italy to China for garment production,” says Szeto. “We now need work-around solutions because Italy banned flights to and from China.”
When factories eventually start running normally again, “there will be a bottleneck with logistics, as everybody will fight to ship out goods that are late” – with forecasts also pointing to elevated freight rates as carriers accommodate both the backlog of shipments and new orders placed as factories reopen. Limited shipping capacity and disruptions could also cause some cancellations.
And looking further ahead, Szeto also warns “even more severe disruption could come if factories don’t have the cash flow to survive, when it becomes a matter of cancelled production rather than delayed production.”
Contingency plans
High-end performance clothing maker KTC, whose main production base is in Heshan City in China, has “decided to remain closed for the time-being, until we can ensure that we are able to provide a safe working environment for our colleagues,” its CEO, Gerhard Flatz, tells just-style. He adds: “We’ve informed our customers and so far no negative reaction at all.”
Angie Lau, CEO at lingerie maker Clover Group International, says that while its factories in Dongguan resumed work on 10 February, this was with just half its workforce.
“Workers are gradually returning from their hometowns [following the New Year break] but we have enforced the 14 day quarantine protocol to ensure we have a clean and non-contaminated environment,” she explains.
“We are currently trying to catch up with the production time lost during the compulsory shut down.”
With the majority of its staff prevented from travelling both within China and overseas, the company is turning to technology to keep things moving. “We have been actively utilising software tools such as 3D virtualisation [Browzwear] to connect with our customers. This not only saves time but is extremely environmentally friendly.”
But Lau also cautions: “The whole supply chain has been disrupted for supplies pertaining to our March and April production. The snowball effect will be a much bigger issue.”
Nevertheless she adds: “All our customers are vigilantly working through this crisis with us as they fully understand the severity of the virus and the stance taken by the Chinese government. We have not had any cancellations.”
Clover Group also hopes it will face less of an impact from the disruption in China since it has already diversified its supply base to mitigate the effect of US tariffs. “We have been shifting our production orders to our factories overseas in Thailand, India and Cambodia,” Lau confirms.
Travel restrictions have also made it harder to conduct factory audits, visits and inspections, including factory approval or new factory onboarding
The CEO at another vertically-integrated multi-country manufacturing giant also tells just-style “things are moving along in spite of the current challenges. Two of our four factories have started production…and some of our fabric mills have started production.
“Our customers are overall very sympathetic to the situation and we are working out our production plans with them.”
Compliance issues
Travel restrictions have also made it harder to conduct factory audits, visits and inspections, including factory approval or new factory onboarding, according to Hong Kong based sustainability and supply chain services provider Elevate.
The company says it expects to resume audits and onsite factory consulting visits in China from next week (24 February), but has suspended operations in Hubei Province until further notice.
“Over half of Elevate’s key customers sourcing in China are rescheduling audits, and have expressed concern about workers’ ability to return, compliance issues and delivery schedules,” it says.
Even so, while “contingency plans are in development, most key customers are not changing their sourcing strategy as a result of supply chain disruptions resulting from the coronavirus.”
Feedback from a factory survey carried out by the company – the majority of whose respondents are based in China and operate in textiles (32.9%) and fashion (25%) – suggests most will have re-started at least some production this week (17 February) and envisage a return to full production (barring any further challenges) between the end of February and mid-March.
Factories are also taking numerous safety and protective measures against the coronavirus, such as the use of masks, temperature checks, regular disinfection, hand washing and sanitiser use, travel history checks, separate lunch areas, and an increase in the distance between workers on the production line.
The concern is that if Covid-19 is found on-site, then the entire operation will have to be suspended for 14 days.
Anecdotal feedback shared by Elevate also suggests that “so far, facilities have not indicated a need for financial aid from customers but are hoping customers will not cancel orders, will be understanding of delays, and will consider waiving any penalties for delayed delivery of goods.
“We are finding that many global brands, retailers and vendors are still in strategic meetings to understand and model the supply chain disruption. Subsequent to this, they will be putting together mitigation/contingency plans and sourcing and CSR decisions are expected to follow.
“We’re discussing with many customers the advantages of advancing audit programmes in sourcing destinations outside of China – such as Latin America, South Asia, and Southeast Asia.”
Click on the following link for more just-style coverage: Is coronavirus a threat to the clothing industry?