Faced with demands for shorter and shorterlead times, escalating flexibility requirements, and intensified competition from offshoremanufacturers, UK company Debfor Ltd has invested to increase throughput and costeffectiveness in its cutting room.
With a customer base that includes many ofthe major high street stores and mail order catalogues, Debfor manufactures lingerie andswimwear garments at its five sewing units in Long Eaton, Ilkeston, Heanor, Leek and atCumbernauld in Scotland.
As part of the Sherwood Group, the companyemploys in the region of 600 people and has, over the past few years, managed to achievean impressive year-on-year growth.
But success on this scale brings with itthe pressure for continuous improvement – a fact that is not lost on Debfor’s cutting roommanager Andy Kingston. He notes: “With swimwear and lingerie you are producing somany short runs in a wide range of colours that you must be very flexible in servicing themarket. You have always got to keep looking to improve on what you’ve got. We need toprovide a quick response service to our customers and, by utilising the capacity of thecutting room to best effect, we are able to ensure consistently high quality productionand maintain a regular flow of work to the sewing rooms”.
Cutting room investment
Since joining the company in 1993 Andy has overseen a £0.5 million investment atthe cutting centre in Long Eaton – coupled with a reorganisation of its layout to achievea more efficient work flow and further reduced handling. The outcome of this has been anincrease in both throughput and cost effectiveness.
Behind the achievement also lies theinstallation of two Rimoldi 928 Matic spreading systems and a S-5200 cutter from GerberTechnology to replace the previous manual spreading and eight band knife operations thatwere struggling to keep up with demand from the sewing units.
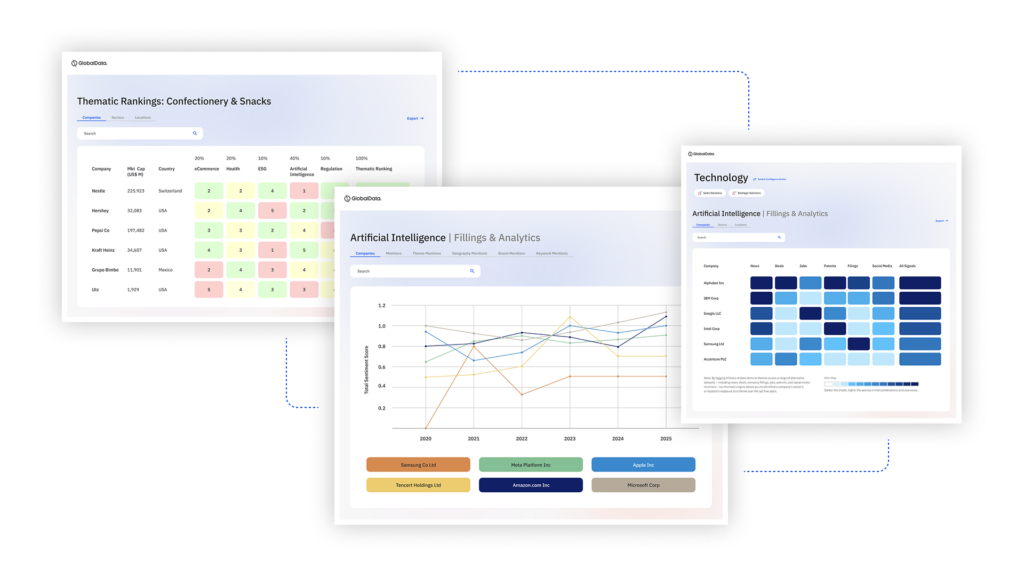
US Tariffs are shifting - will you react or anticipate?
Don’t let policy changes catch you off guard. Stay proactive with real-time data and expert analysis.
By GlobalDataGarments are getting more and moretechnical too, and prior to the automation of the spreading and cutting operations thesheer volume of the workload presented additional problems in the cutting room. Andy says:”Some items can have as many as 29 cut parts, and this increases when you addcomponents such as bows, underwires, hook and eyes, foam and pads”.
Fabrics are also getting more advanced andthe microfibres, Tactel, Lycra and laces that are a regular feature in today’s lingerieand swimwear garments are all very difficult to handle. Any tensions in these fabrics willbe magnified as they progress along the production pipeline, and working to a tolerance ona bra of just 0.5cm does not allow much room for errors. So savings that can be achievedin the cutting room considerably help the quality achieved at the sewing stage.
Tension-free spreading
This is where the Matic 928 comes into its own for Debfor, since it has beenspecifically designed to lay tension-free. In his previous role at Speedo (Europe) Ltd,Andy had seen first hand the benefits that the 928 Matics could bring. “Beforepurchasing the 928 Matic we evaluated spreaders throughout Europe”, he explains,”and found the Rimoldi range to be by far the best”.
The machine features a conveyorised singlecradle designed to unroll the fabric and, using a lazy loop system, detect the fabrictension and automatically adjust the cradle speed in order to maintain the correct fabricfeed. Whilst spreading, the machine will even compensate for different fabric tensions,particularly as the fabric roll reduces in diameter. This is particularly important whenhandling difficult fabrics, such as those containing Lycra.
For additional flexibility, the 928 Maticoperates without the use of any clamps, and can therefore start a lay at any point on thetable. It also offers a wide range of spreading modes, one of which – one way laying – isproving to be very useful for Debfor at the moment since it has a lot of velvet and pilefabrics passing through the factory.
The two Rimoldi 928 Matics run on 3spreading tables, and spread all the fabrics passing through the cutting room. Thisequates to around 10,000 metres a week on each machine. This would be higher were it notfor the fact that the company is dealing with a high number of short lays and has to copewith numerous stops and starts.
Over the last few years savings of around 5per cent have been achieved on material costs. Much of this is put down to the fact thatthe fabric is properly and consistently relaxed – firstly, when it is presented to thespreading system and, secondly, when it moves to the cutting equipment. “Spreaderscan’t take the tension out of a fabric – but they can certainly put tension in”,comments Andy, “and this is where the 928 Matic from Rimoldi comes into its own. Thesavings we have been able to achieve can be directly related to the improved presentationof work to the sewing unit”.
A 6-8 week turnaround on styles can now beachieved by Debfor Ltd, and this ensures that the company has a leading edge in the marketplace.
Constant improvement
In its drive for continual improvements to the system, Rimoldi has launched a newon-board computer control for its spreading machines.
Bill Brealey, Rimoldi’s regional managerfor the Midlands and south east, explains that the CM98 can directly control all set-upparameters – including speed adjustment, deceleration and acceleration – as well as beingable to regulate fabric tension. The computer can also retain in its memory the differentspreading parameters for various fabrics, which will offer considerable time savings inmanually entering the parameters. The CM98 is self-diagnostic, and in the unlikely eventof machine breakdown it will automatically locate any faults that might occur within theunit, making troubleshooting and repair a much easier task.