
The Covid-19 pandemic has had an unparalleled impact on the apparel industry, causing drastic changes in the way it manages supply chains. Consequently, digitalisation and technology have moved from being a competitive advantage to a practical necessity as businesses adapt to new ways of working.
“We’ve seen the rapid acceleration in automation and the digitalisation of work,” Susan Hayter, senior specialist, labour relations, International Labour Organization (ILO), said on a webinar for the recent CFS+ event, the new digital concept of the physical Copenhagen Fashion Summit.
“Companies have had to ramp up their deployment of digital technology at a time when it’s simply not possible to travel around the world for product development. And work patterns, work practices and work places have changed. In my mind, the need for action to shape a human-centred future of work is more pressing than ever.”
In the apparel industry, digital technology is centred around designers and office workers to maintain work and income continuity. However, machine operators do not have the luxury to work remotely. Apart from the risks to their own health, their incomes were immediately affected by declines in retail activity, falling demand, the cancellation of orders and the reconfiguration of supply chains, Hayter explains.
In Bangladesh, only 49% of garment workers were working in the month of April, according to figures from the ILO. This rebounded to 88% in May but with average income reductions of 42% per month because of working hour reductions.
“The fact is, the countries with low tech infrastructure are far less able to reap the benefits of technology and digitalisation to give them the resilience that is needed. A human-centred future of work for these suppliers and workers is going to require joint action to address the devastating impacts of the pandemic and the economic crisis.”
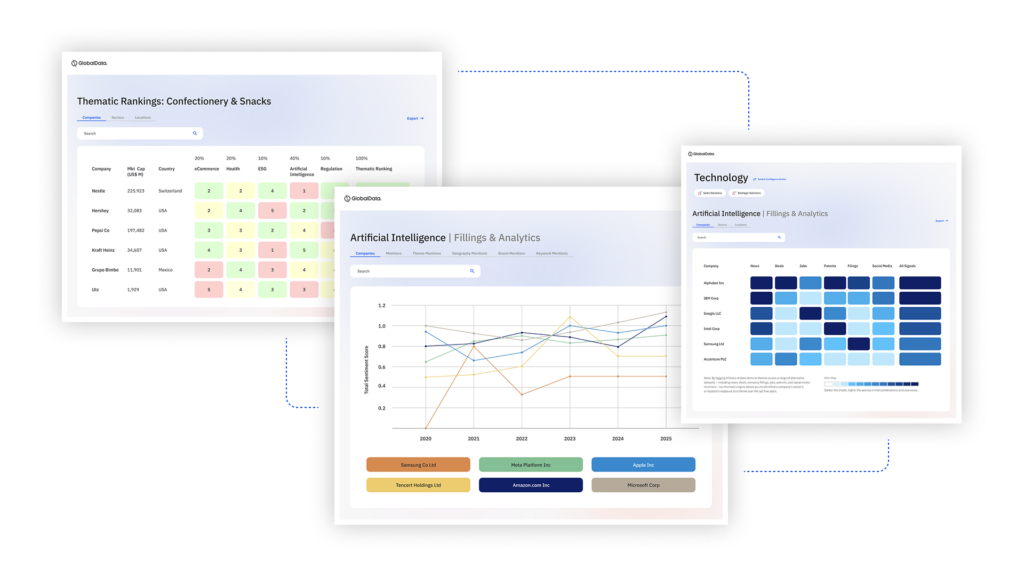
US Tariffs are shifting - will you react or anticipate?
Don’t let policy changes catch you off guard. Stay proactive with real-time data and expert analysis.
By GlobalDataHayter says this will also mean ensuring pricing structures cover the cost of decent work, and that the predictability and timely payment of orders and adequate wage protection is secured. Safe working conditions, which may require factories to make adjustments for social distancing, also needs to become acceptable.
“Digital technology can of course help us in all of these areas, because it can track who is doing what. Accurate forecasting and calendar management enabled by digital technologies can impact positively on excessive overtime. And we’re seeing an encouraging uptick in the digitalisation of pay with better compliance and wage protection.”
The ILO recently created a Transformative Tech for Decent Work Innovation Facility. It brings together ILO experts, worker and employment organisations, regulators and enterprises, universities civil society and technologists to ideate, pilot and scale solutions to advance decent work.
Projects have included the scaling of digital payments to enhance access to social protection, the use of geo-location and supply chain mapping to enhance traceability, VR and sensor technology to enhance the detection of hazards and help mitigate Covid transmission, and predictive analytics and machine learning to help public regulators and inspectors better target interventions at likely non-compliant enterprises.
“We are not necessarily talking about cutting-edge technologies, but really about seeking to leverage existing technologies in new ways to deliver a human-centred future of work,” Hayter says.
Moving upstream
As well as more basic ways of improving and implementing digitalisation, larger companies are making substantial investments into digitalising their processes.
Li & Fung is one of those. Four years ago the sourcing giant unveiled a new strategy focused on innovation and digitalisation, which, at the time was intended to allow the company and its customers to react quickly to changes in the retail environment, as well as quickly to any disruption or any requirement of business resilience that might happen.
“At that time, we could not have anticipated how critical and important these capabilities would become for business continuity, environmental resilience and the human impact of our supply chain,” says Deepika Rana, Li & Fung, CCO and president of supply chain solutions. “We’ve all experienced disruption due to Covid-19 but in the apparel trade, the product development process has been particularly disrupted.
“Without the ability of the designers to travel they’ve actually been handcuffed, and their usual sources of inspiration; the product development trips, the fairs for design and product development have all been completely reduced and stopped under the lockdown.
“None of these options exist today, so now without the design teams having access to physical samples, digital samples and digitalisation of the supply chain becomes of critical importance to enable designers and retailers to review their lines, see the product they’re buying and also visit suppliers virtually while sitting at the other end of the world.”
In addition, Rana says unprecedented lockdowns also meant they don’t have access to all of their data, and are therefore relying more on digital tools.
“All of the challenges require that the digital solutions we put into place earlier had to be completely enhanced and speeded up. We had to react very quickly. While the supply chain and the retailers were loathed to really accept digitalisation very quickly, right now it isn’t a choice and it is the only tool that not only helps environment but also helps continuity of the business and also helps us provide our customers, who are shopping more and more online, the images and product they really want.”
Rana adds, the accelerated adoption of its digital solutions has also helped its efforts to reduce the environmental footprint of the production process. This has led to more responsive, demand-driven supply chains that reduce waste, more accurate decisions, fewer markdowns and reduced rates of return.
“Digital product development eliminates the need for physical sampling and the associated material waste, material sourcing, transportation, carbon emissions, shipments or air-shipping of samples to reach retailers on time, is also greatly enhanced. This reduces the environmental impact of the sampling process by almost 50% on average, with the potential to reduce it by over 90% in the coming years,” she explains.
“Through the development of our digital platforms we’ve witnessed not just positive environmental impacts but also social positive impacts. For example, there are clear impacts for workers when development practices are better managed. As a result, we find that key labour issues such as working hours, overtime are all greatly reduced or almost eliminated.”
Capitalising on capabilities
For the ILO, connecting labour administration, such as inspectors, with data collected in the monitoring of supply chains is crucial from a social perspective.
Hayter says this will help support inspectors and allow them to better place their resources. “There is work being done, and not very sophisticated in terms of data analytics, but some work being done to support, in Brazil for example, labour inspectors to target places that are more likely to have forced labour. For example, there is work to allow workers to report anonymously.
From a transparency perspective, Hayter says this opens up opportunities for companies to share their sourcing data, and then to benefit from the planning, the predictability, and sustainability of supply chains, not only for the environment but also for workers.