The need for control in productdevelopment and pre-production work
To further understand this, we must consider the product flow in the supplychain. Figure 1 is a simplified diagram.
Figure 1. The product flow
The area of product development lies between the range planand manufacturing. Turning the range plan into a fully designed range of garments is acomplex and time consuming business. This is traditionally not closely controlled, andfurthermore has, on average, a 90 percent fall out between concept and order. Naturally,this all takes a lot of time, It also places a limit on the rate at which new collectionscan be produced. Figure 2 shows the relative times taken on the main processes needed totake a product from concept to store.
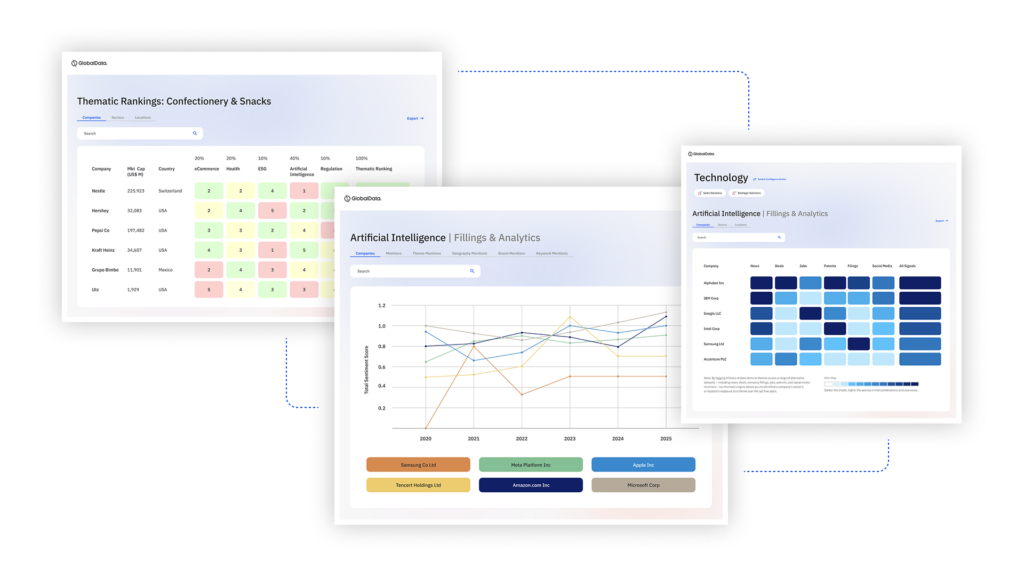
US Tariffs are shifting - will you react or anticipate?
Don’t let policy changes catch you off guard. Stay proactive with real-time data and expert analysis.
By GlobalDataFigure 2. The time factor
|
|
It can be seen clearly that product development is by farthe most time consuming task. A system is needed that:
- reduces time spent in product development
- co-ordinates global development
- produces a high quality specification for manufacturing and quality control purposes
How computer systems can assist in productdevelopment
Design starts with an idea and ends with products being purchased at full priceby a consumer who is happy with the bargain and will return to buy again. What is neededto achieve this ideal situation?
Early selection of “winners and losers”
It is vital to identify the products that are likely to be successful. At a very early stage in the process, producers must avoid doing unnecessary work on the 90 percent that will not be adopted. Frequently, this is governed by financial considerations. In turn this leads to a need for an early “flash costing” to determine the viability of a product.This provides a “gate” near the start of the development process. This gate either demands revision or rejection of a product that cannot be sold at the projected price point and show a sufficient margin. This, in turn, means that less styles are passing through a development path already overloaded with the increasing variety of product. This enables a reduction in the time from concept to store.
Conformity to a strict timetable with constant reference to a critical path
When a fast turn of collections is required, time is of the essence and meeting the in-store date is critical. Late shipments inevitably mean lost sales. In these circumstances, the development process must conform to a strict timetable. Keeping track of this process and taking corrective action, demands a live critical path system which constantly reports on the progress of each product and identifies potential bottlenecks.
Production and refinement of a detailed and accurate product specification
With manufacturing moving offshore, the quality of the manufacturing specification must be very high. Also, to counter language problems, it must be multi-lingual and rich in diagrams, pictures and even video clips. Conversely, visuals of the product coming off the line must be readily visible in the home office to assist in the detection of problems before shipment.
Communication and agreement of changes on a worldwide basis
During both the design phase and the production phase of a product, constant changes in detail are made. These must be communicated rapidly on a global basis to all who must know. In direct contrast to paper systems, people must be sure that the data appearing on their screens is both correct and up to date.
Link design, pattern making, marker making, Management Information Systems (MIS) and retail systems seamlessly
No single computer system can provide all the information needed to manage a sewn products enterprise. There are the tools used in the design and manufacture of the product, such as concept and pattern design, marker making and synthetic data systems. Then there are the MIS, which reports on the manufacture, shipping, stock control and sales performance of each product. All these must be linked seamlessly together to provide the consolidated reporting to manage a fast moving consumer product.
In practice
Once the range plan is complete, rather than start completely from scratch, thedesigner uses sales information stored in MIS to identify “winners”. The systemcan drill down into the pattern design system and retrieve the patterns used as a basisfor the new style. When the costing point is reached, all the production markers madepreviously are available for viewing and comparison, (as are the trim and labor costfigures). Seamless access to this bank of proven data makes the task of productdevelopment quicker and more accurate.
As development proceeds, a full product specification isprepared. Once the style is adopted, all details about the style, Bill of Material (BOM),labor cost analysis and size charts are downloaded to the MIS for the sourcing,manufacturing, shipping and sales processes. As these progress, summary data onmanufacture and sales performance is fed back into the production development system forfuture use.
When looking at the cycle of a product, the followingquestions can be answered –
- What was the estimated cost at the design stage?
- What did it actually cost to make?
- How did it sell?
- What was the actual margin?
- How much profit is attributable to the product?
This data is invaluable when starting a new productdevelopment. If we consider the supply chain once more, the relationship of the systemscan be seen in Figure 3.
Figure 3. The product flow
The requirements and the rewards
The installation of a computerized product developmentmanagement system demands similar disciplines. The potential rewards, however, areconsiderable:
- shorter time from concept to store that enables collections to be rolled more frequently
- a higher design quality can be achieved due to concentrating design work on likely “winners”
- better quality specifications mean better quality product
- critical path control means better delivery performance
All these mean better sales performance. It is likely thatthose enterprises, which adopt these advanced computer systems quickly, will enjoy acompetitive advantage over those who are slower to do so.