In this part:
- Introduction
- Popular Planning Functionality
- Proposed planning system processes
- Combination of processing stages
In part 2:
- Remove need for re-runs
- Cater for sourcing
- Utilizing EDI and the internet
- Finite capacity scheduling
- Automatic presentation of exceptions
- Automate all communications
- Conclusion
Introduction
Change in the Apparel& Footwear business is constant. There is intense pressure to:
- reduce the length of time between conception to delivery
- move from local manufacturing to global sourcing
- change the way we plan for seasonality
A large number of companies have moved awayfrom manufacturing products to sourcing from other suppliers. This has meant that the usefor production control systems has dipped dramatically. The need to plan and have suppliervisibility has increased tremendously. Care must be taken not to expend too much effortand cost in improving production control IT systems. Companies must be careful as thesavings gained will be small in comparison to those made when improving planning systems.
Traditional Manufacturing Resource Planning(MRP II) systems do not provide the right level of support for these changes. This followsthe concept that a master production schedule is created first. Afterwards the lower levelmanufacturing items and raw materials plan are built. This two level structure is notrequired, as it is common (although not 100 percent true) for Bills of Material (BOM) inApparel & Footwear Industries to be flat (i.e. finished goods made from rawmaterials).
How can the MRP II system effectively copewith the planning and re-planning of global sources? The time involved in running a numberof large processing jobs reduces the amount of time available to make the manualadjustments. This article examines the current planning systems, looks at what can beimproved, and then attempts to describe the ideal planning system.
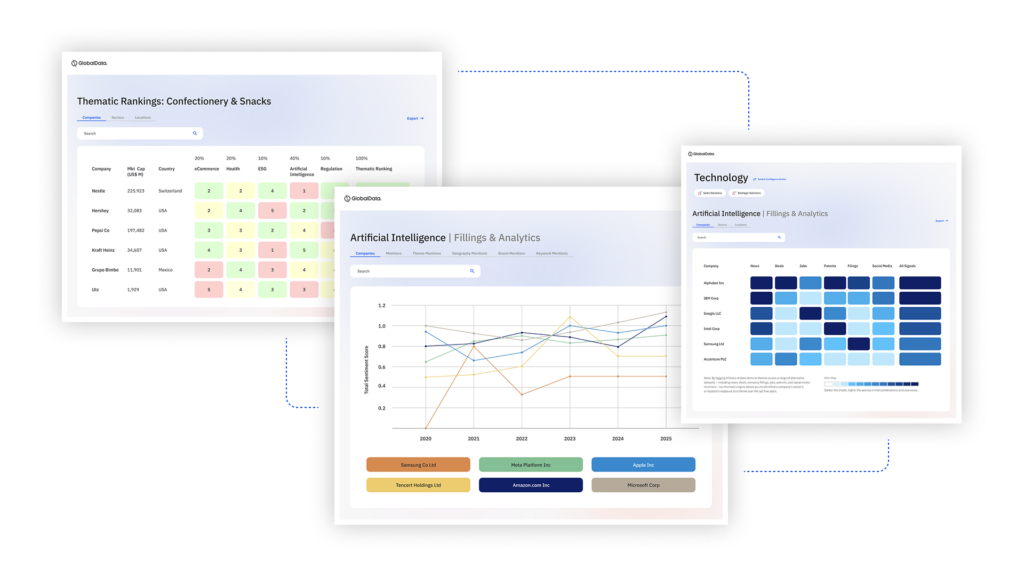
US Tariffs are shifting - will you react or anticipate?
Don’t let policy changes catch you off guard. Stay proactive with real-time data and expert analysis.
By GlobalDataCurrent planning systems do not meet the requirements of the Apparel & FootwearIndustries. In order to explore the reasons why, this section will look at the systems inmore detail. A typical system (see Figure 1) is made up of a number of modules. Itrequires a number of batch runs to determine production, resource and purchasingrequirements. The main problem is the need to revise the outputs from one batch run andthen re-run the same batch job to review the impact of those changes.
Figure 1: Typical planning process
This is a typical example of the steps required to achievethe plan every week:
1. Demand management.
Review difference between sales orders and forecasts to determine planned demand.
2. Master Production Scheduling.
The demand (sales orders and forecasts) for each item is compared with it’s existing supply and stock to determine a net requirement (e.g. new production order with quantity and due date).3. Rough-cut capacity planning.
The above production plan is converted into resource requirements. It is then compared to available capacity on an approximate fit (rough-cut) basis. The system has to read the rough-cut route for every production order to determine the resource requirements.4. Revise the master production scheduling output (MPS), because of imbalance of resources, by confirming orders on suggested and new dates.
As suggestions are re-generated by each MPS run, it is essential that they are confirmed either using the suggestions or changed date/factory. The process reruns through steps two and three. If the plan is acceptable then it continues to the next step. This is a manual process used to balance the master production plan in line with the available resources.5. Materials Requirements Planning
(MRP) explodes the master production plan into part-finished product production and raw material requirements. It performs the same processing as MPS but for all items, including the MPS items, again. Additionally, MRP determines the demand for part-finished items and raw materials by reading through the BOM for each item.6. Capacity Requirements Planning.
This converts the detailed production plan (both finished goods and part-finished products) into a detailed resource load. It reads through the detailed routing for every production order (including those suggested by MPS) to determine the detailed resource requirements.7. The detailed production plan output is revised (because of imbalance of resources and materials).
Orders are suggested and new dates confirmed. The suggestions will be re-generated by each MRP run, so it is essential that they are confirmed either using the suggested date or changed. The process reruns through to steps five and six. If the plan is acceptable then it continues to the next step. This manual process is used to balance the master production plan in line with the available resources.8. This is the final step in the process and is used to confirm the whole production plan.
There are two main concerns here. Firstly, can this all be achieved within the working week? The timing of running the jobs can be critical, as they run in a dedicated mode (i.e. overnight). A problem with central systems in a 24-hour factory is that someone is always working, therefore, can the processing jobs be run?
Figure 2: Revised planning process
If a mistake is made then it will be a whole day before it can be corrected and the impact known. Once a plan is made that is not the end of it. There are changes to demand and problems with supply (both dates and quality). This means that the plan must be revised to meet the latest situation and the revision of the plan needs to be performed efficiently.
Secondly, the emphasis on the popular systems appears to be on planning for a company’s own production facilities, when the majority of Apparel & Footwear products are now sourced from suppliers. Can the capacity planning systems cater for suppliers’ capacity as well as owned factory capacities?
Proposedplanning system processes
Combinationof processing stages
The process needs to be streamlined by combining some of the steps and reducing thenumber of re-runs. The majority of these processes work by taking a ‘snap shot’ of thedata at a point in time. Therefore, the master file information will be copied intotemporary files for processing. This is required for every step. Consequently the samefiles are copied a number of times.
The main reason for separating out steps two and three(master production planning) from steps five and six (detailed production planning)appears to be related to traditional manufacturing systems. These have evolved forengineering companies who had multiple levels in their BOMs. Also, traditionally twoseparate departments (production and purchasing) performed these two functions. It is morecommon (although not 100 percent true) for BOMs in the Apparel & Footwear Industriesto be flat (i.e. no intermediate stocked sub-assemblies). This means that there should beno need to process manufactured items in MRP. Therefore, the need for separate rough-cutand detailed capacity requirements planning runs is removed.
To cut down the double processing of all the items, itmakes sense to combine the MPS (or as it should now be called, production scheduling) withcapacity requirements. Systems should also be flexible enough to generate either rough-cutor full detailed capacity requirements depending whether there is a short or long-termplan.