In this part:
- Remove need for re-runs
- Cater for sourcing
- Utilizing EDI and the internet
- Finite capacity scheduling
- Automatic presentation of exceptions
- Automate all communications
- Conclusion
Part 1 covered:
- Introduction
- Popular Planning Functionality
- Proposed planning system processes
- Combination of processing stages
Remove need forre-runs
Re-runs can only be removed by providing a facility to revise the output of a batchrun and reviewing the impact on-line. The existing facility – a production scheduling runcombined with capacity requirements planning – would require views of both the productionplan and resource plans. In order to have the facility to revise the plan – date or routechanges – with an immediate impact on both the production and resource requirements,recalculation is required. This function could be enhanced by the provision of pictorialrepresentations of the resource plan.
Cater for sourcing
The above improvements will definitely help those companies using their ownmanufacturing plants. If they source from supplier factories, then the ability to holdtheir capacity is essential to balance the plan. Additionally, the revision of the planshould allow for movement of work between different suppliers. If there is no requirementto plan capacity for supplier factories, then there is no need to run MPS and MRP as thereis only one type of item.
The flow of information between the company and their customers/suppliers needs to beimproved. EDI improves the timing and accuracy of sales order information from customersand purchase order information to suppliers by automating order entry and confirmation.Why not get the customer to directly enter the sales order through the internet?
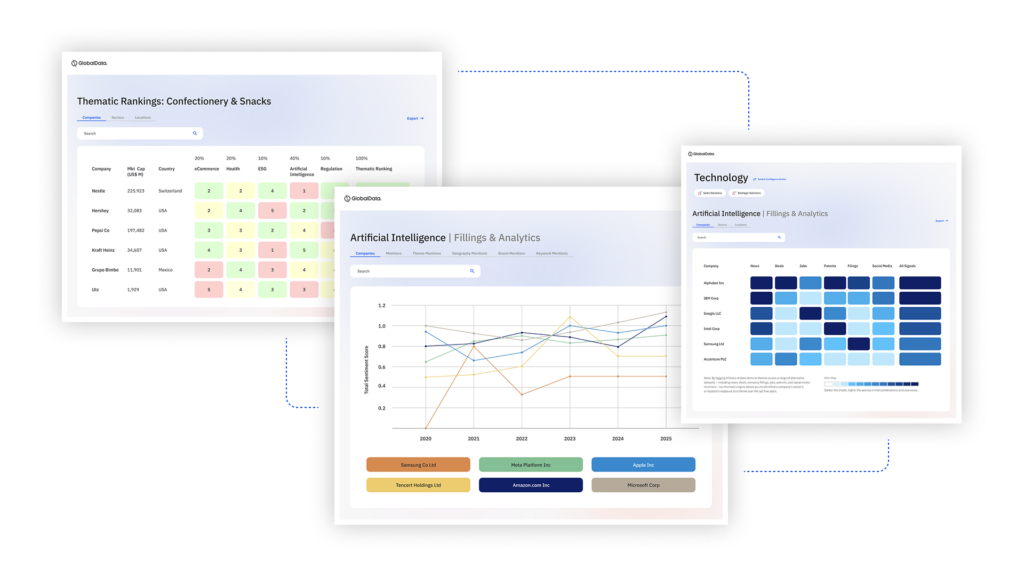
US Tariffs are shifting - will you react or anticipate?
Don’t let policy changes catch you off guard. Stay proactive with real-time data and expert analysis.
By GlobalDataAutomaticpresentation of exceptions
The problem could be that the job he or she wanted to starttomorrow was delayed due to a breakdown on the factory floor. This information can beobtained by the system from constant review of the planned versus actual in terms ofmaterial usage, expected date of completion, reported downtime and so on. This makes theplanners’ job much easier because he/she is presented with the exceptions rather thanhaving to search for them. This allows him/her more time to resolve the issues.
Automate allcommunications
All outside communication would be automated via a combination of e-mail and EDIfunctions. This includes feedback from progression sourcing (including manufacturing) ofgoods and materials. This information would be used to automatically re-plan based on aset of user defined rules. The customer would automatically be informed of the changesthat may affect delivery dates.
This means automating all communication and actions tovariations to the plan. It sounds good – the system makes all the decisions – but theability to define all the rules would be impossible because of the constant change in theway businesses work. This is not available today, but it will be some time in the future,as development work is in progress.
Conclusion
As we have seen, a lot of the old MRP principles still stand. Production plans stillneed to be determined based on supply and demand and resources and materials. However,some of the less mature systems are too rigid and cannot cater for the constant changingcustomer demands and supplier support. Globalization has meant that our suppliers’ factoryresources within the production plan must be included. Any changes in the plan must beeffectively and quickly communicated.
MRP systems for the Apparel & Footwear Industries arestill valid. However, care must be taken to ensure that the system is flexible enough tocater for the issues surrounding global sourcing and reaction to current and futurechanges.