The ability to respond to the customer with the right product, quantity, priceand location at minimum cost has been cited as the hallmark of the ‘world-class’manufacturing business. In the 1990s, this operating paradigm is called efficient customerresponse (ECR). Before, this had been associated mainly with the retail side ofdistribution. Retailers know that the product must be on the shelf when needed. Theyrealize the need to minimize shortages, they offer high quality and increase margins. Thismust be done while they search for ways to reduce the amount of stocked inventory. Forthem, slow delivery and product shortages cause customers to go elsewhere.
The customer can exist in many forms: individuals, smallbusinesses, multi-nationals, government agencies. All bring their own characteristicpressures to bear. In addition, the internal customer, also requires efficient servicingand quick response. The increasing high service levels demanded reflect producers’pressure to deliver a similar service level to their customers.
In complex manufacturing and distribution networks, allnodes in the supply chain must integrate ECR principles into their core activities. Inthis way the whole supply organism is oriented to world class customer service. Ratherthan the traditional philosophy focused narrowly on the point-of-sale, the concept of ECRshould be propagated throughout the entire supply chain. This originates with themanufacturing process or the manufacturer’s suppliers.
What is Rapid Customer Response
Rapid customer response is concerned with increasing the rate at which relevantinformation flows through the distribution pipeline. In this manner, it improves thequality and timeliness of the information. In turn, this accelerates the flow of productfrom the manufacturer to the point of demand. To increase these velocities, productsuppliers and distributors must focus on the entire supply chain (not just isolatedsegments). They must identify and minimize or eliminate all constraints. Also they mustdeploy effective planning and control systems. These systems provide planners withvisibility of changes in demand and supply, and the means to rapidly realign customerrequirements with supplier capabilities. As the flow of product increases through thetotal supply pipeline, manufacturers will enjoy higher customer satisfaction and lowerinventory and logistics costs.
The implementation of rapid response requires theproduction/distribution enterprise to move away from the view that it is an issue only atthe final distribution point (the customer). In practice, successful rapid response meansadopting a new approach to manufacturing and supply management. Manufacturers must payattention to quality, and integrate all manufacturing and distribution network components.Many rapid response techniques are similar to the well-understood principles ofjust-in-time (JIT). Rapid response requires every node in the network to be committed to:
- continuous improvement
- the elimination of waste
- total quality
- workforce empowerment
In addition, it requires techniques that; eliminate networkredundancy, improve production efficiency, and align supply capabilities with demandrequirements.
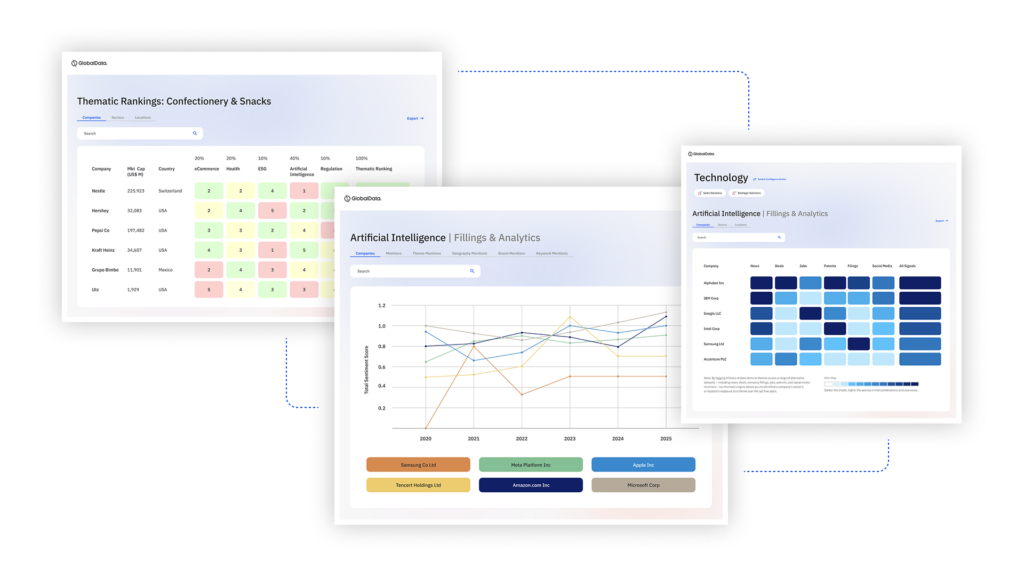
US Tariffs are shifting - will you react or anticipate?
Don’t let policy changes catch you off guard. Stay proactive with real-time data and expert analysis.
By GlobalDataThe rapid response model that emerges can be understood asa series of planning steps that provide continuous synchronization of both anticipated andreal customer demand with manufacturing and logistics capabilities. Effective systems arepossible only when comprehensive business information and knowledge of demand and supplyare meshed. Customer requirements, both forecasted and actual, must be available to themanufacturer. In turn, the manufacturer can plan production and logistics capacities intandem with the upstream supply network. The objective is to remove response uncertaintiesby establishing a closely coupled system. In this system, customer demand andprocess/logistics imbalances are aligned before demand and supply is dislocated andcustomer service is degraded.
Contemporary pressures on manufacturers typicallyinclude:
- highly aggressive delivery lead times
- smaller delivery time windows
- fast changing product call-offs against a schedule
- location specific deliveries
- pre-sequenced component delivery to the customer’s production line
- customer led product specification with frequent design changes
- legislative pressure i.e., environmental, packaging or material origin.
- customer purchasing power leading to price freezes and shrinking margins
All these pressures can be met to a greater or lesserextent by the imaginative use of enterprise resource planning (ERP) software.