
With manufacturing technology advancing at an ever-faster pace, sports apparel and footwear companies need to constantly look for ways to embrace new techniques to compete in an ever-changing landscape, an international industry meeting has been told.
Sustainability, blockchain and Industry 4.10 are three of the most important trends being considered by brands and their suppliers – and they were focal points at the sixth World Manufacturers Forum (WMF), organised by the World Federation of the Sporting Goods Industry (WFSGI) last week in Ho Chi Minh City, Vietnam.
Sean O’Hollaren, senior vice president for government & public affairs at Nike Inc, and WFSGI’s chairman of the board, highlighted how these issues informed the evolving relationship between producers and consumers. “This is not about just what we do, but how we do it,” he said. “Speed is driving everything. If you look at Amazon and Alibaba and others, consumer expectations on how quickly we’re getting products to them is evolving day-by-day and making all of us do our work a little bit differently.”
O’Hollaren also touched on sustainability, an increasingly prominent aspect of sporting goods production given deepening environmental awareness is forcing companies to work towards reducing their carbon emissions.
“Sustainability is not something that is an optional add-on to what we do, it is also a consumer expectation,” he shared. “It’s not an ‘or,’ it’s an ‘and.’ Our good labour practices, our environmental practices, are something that consumers expect from brands.”
And to demonstrate such quality work, brands must gather data and be able to show it to consumers in a credible and efficient manner. But how?
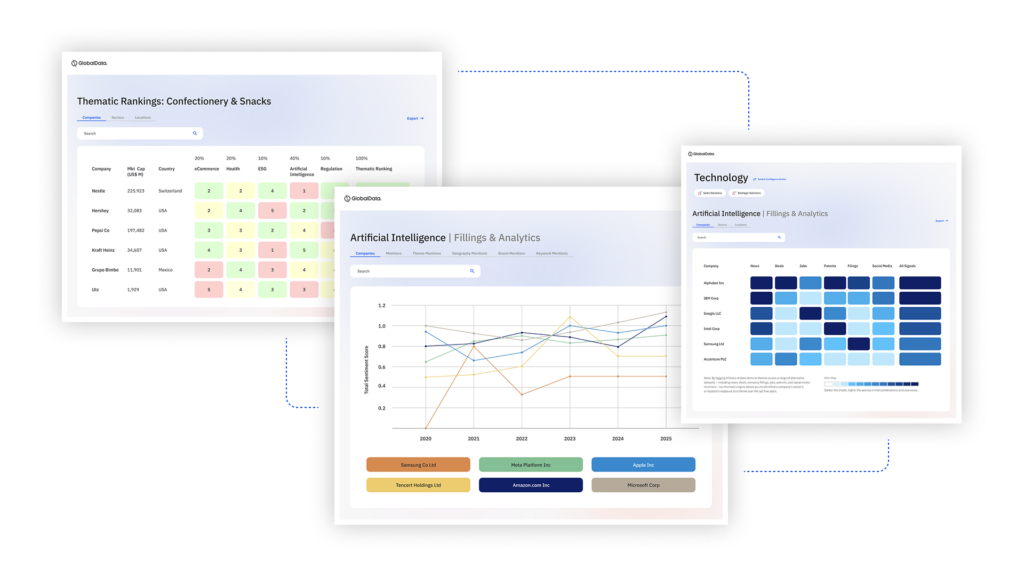
US Tariffs are shifting - will you react or anticipate?
Don’t let policy changes catch you off guard. Stay proactive with real-time data and expert analysis.
By GlobalDataBlockchain is one way forward
“Blockchain is one way forward to create environmental transparency – and it will be a truly transformative technology” – Nicholas Russell
Nicholas Russell, from the Centre for Blockchain Technologies (CBT) at University College London, argued that blockchain is one way forward to create environmental transparency – and it will be a truly transformative technology. “Every 10 years you get something where you see it, you look at it, and it takes a while to sink in – but you really feel like it’s going to be disruptive. The web browser, smartphones and now blockchain. The interesting thing about these moments is that they’re an opportunity to change the landscape.”
That opportunity, as regards blockchain, is in a very early stage, said Russell, who admitted that even experts in the field do not fully understand what blockchain can do even in the near future. However, he argued that it has the potential to someday create a unified global registry that can track all plastic being produced around the world in real-time, for instance.
And this, as regards the sporting goods sector, including apparel, is important. Globally, plastic has become a major environmental issue, with some countries banning plastic bags, and planning bans on other single-use plastics, as concern rises about plastic pollution in the ocean. Russell argued that given the prominence of such problems and the role companies play in them, businesses are now acting in spaces once solely occupied by nations.
“So, consumers are not only consumers, they’re actually expressing their citizenship via their brand purchases and what they choose to use, wear and be involved with,” he said. Companies, therefore, need to respond accordingly.
At present, the most practical blockchain application for most manufacturers is its potential utility as a ledger, or a digital space to note and track sourcing, production, shipping and delivery.
And some of the world’s biggest companies, including IBM and logistics major Maersk, have already created blockchain-based ledgers, while Amazon is working on one as well. The idea is that these systems will allow both producers and consumers to access vast amounts of data previously walled off in separate silos. However, it is still too soon to judge their success.
“The opportunity here is you don’t need to use your own database, while the threat is that actually you’re looking at a case where you don’t control your own database,” Russell said. “This is going to be massively efficient; however, nobody really knows what is going to happen. These are all in really early trials.”
Nonetheless, it is estimated that widespread implementation of blockchain could create US$2-3 trillion in business efficiency savings globally by 2030.
Next generation manufacturing tools
Much of the rest of the conference’s first day focused on Industry 4.0, with speakers discussing how companies will pivot to ensure their workforces are capable of handling changes associated with this next generation of manufacturing technology.
Martin Strommer, advisor to the board at nCinga Innovation, in Singapore, used information generated by the German government’s Industrie 4.0 programme technology promotion company as an example of one vision of the future of manufacturing.
“It is the ability of machines to talk to other machines, exchange information with systems, sensors and, in the end, also with people,” he said. “This ability to connect these elements together creates unprecedented levels of transparency…Human intervention will only be necessary when machines disagree.”
While this may sound appealing to forward-thinking companies, it is important to remember the human component of such advances, stressed two speakers discussing the convergence of technology and manpower.
“Huge challenges remain in terms of recruiting skilled staff able to work with technology in such a sophisticated way” – Rakhil Hirdaramani
Rakhil Hirdaramani, director of Hirdaramani International Exports, an apparel manufacturer based in Sri Lanka, explained how his firm has used RFID technology, combined with its workforce’s skills, to build a more efficient operation.
“When production lines are changing constantly, we need to know what machines are where, and when we talk about multi-site manufacturing at a large organisation, we need to know whether you need to rent a machine or whether you have it sitting at another facility,” he said.
After installing RFID devices on their machines, mechanics can now use a simple tool that quickly shows them when a given machine was last used, whether it is online or offline, and whether it is ready for production or in for repairs.
Lack of skills and experience
While this initiative has been a success, Hirdaramani added that huge challenges remain for both his company and its peers in terms of recruiting skilled staff able to work with technology in such a sophisticated way.
“The challenge we face today in our industry is that it is not sexy anymore,” he said. “There is this huge push to move manufacturing back to the United States, but no one has the technical skills. It’s the same whether it’s in the United Kingdom, Sri Lanka or India, those bona fide production specialists are no longer around.”
He argued for the need to create an automated knowledge base in response to this decline in human skills, which would give future workers access to the information needed to successfully operate advanced machinery.
“There’s just no pipeline of skills and experience, as we have a lot of retiring skills and expertise out there. We need a new blend of skills” – Catherine Cole
Catherine Cole, executive director of Hong Kong-based consultancy Alvanon, spoke further to the crucial need for skill and workforce development as the sporting goods and apparel sector moves into the era of Industry 4.0. Noting that every major industrial shift since the dawn of the Industrial Revolution has brought major disruption to skills and the workforce, she argued that an estimated 400 million workers will need new jobs by 2030 as a result of current technological shifts – about 14% of the global workforce. This figure includes roughly 100 million workers in China alone.
“There’s also a slowing labour force growth rate,” Cole said. “This is due to many factors, including ageing populations, migration and lower birth rates. We will potentially have a workforce issue because we just don’t have as many workers out there.”
That said, while the rise of automated production does not necessarily equate to massive job losses, it will lead to job restructuring. “There is the rise of collaborative robots, or co-bots, and these need people to build them, programme them and work alongside them,” Cole explained. “As these robots have gotten smarter we’ve been able to take them out of the cages they were in and work with them. There is still a human component to this.”
While there has been much apprehension surrounding the automation of production, only around 6% of total jobs are expected to be fully automated by 2030, although most jobs will have the potential for some level of automation by then, she said.
Accordingly, Cole pointed out five skills that will be absolutely necessary for Industry 4.0: technology and computer skills; programming skills; critical thinking; working tools and techniques; and digital skills.
“Do we have the right skill sets for the next 10 years?” she asked conference attendees. “The fact is, our labour force is being challenged.”
On this note, she echoed Hirdaramani’s concerns. “There’s just no pipeline of skills and experience, as we have a lot of retiring skills and expertise out there. We need a new blend of skills, and then there is a negative perception of manufacturing as a career path, and we’re definitely seeing this in the apparel industry. It’s just not attractive to younger generations.”
As a result, Cole argued that companies need to work together to upskill and educate workers in order for the industry to thrive in a new era.
“There has to be industry cooperation to upskill the industry,” she said. “It’s not something that any one company can do alone, so it’s very critical that there is some cooperative activities that happen.”