Etam’s rich pickings
The move from supplying branches withpredetermined bulk allocations of garments to a process whereby they re-order on a dailybasis to replenish sold stock has resulted in Etam Plc revolutionising its storage anddistribution process.
By introducing fundamental changes to itsdistribution process at the beginning of last year, Etam Plc, the UK arm of a majorinternational women’s and children’s garment retailing group, has had to totallyreorganise its 350,000 square foot UK warehousing and distribution centre at Boughton inNottinghamshire.
The complexity of the operation can bejudged from the fact that the centre receives around 580,000 units of hanging and boxedmerchandise each week from 300 suppliers delivered by around 400 truck-loads.
Planning for the changes began in December1997. The building’s merchandise handling system was completely dismantled, reorganised,extended and renewed in a very tight time-frame, with the new system becoming fullyoperational early in March 1998.
Describing the new approach to thewarehousing and distribution system as “revolutionary” for the centre, KeithSansom, distribution controller, explains that the company has moved from a”push” process – supplying branches with pre-determined bulk allocations ofgarments – to a “pull” process, whereby branches re-order garments on a dailybasis to replenish sold stock. Daily deliveries of replacement stocks to each shop fromthe distribution centre are planned to ensure that there will be a high certainty thatexamples of each style, size and colour of garment will be continuously available tocustomers throughout its selling season.
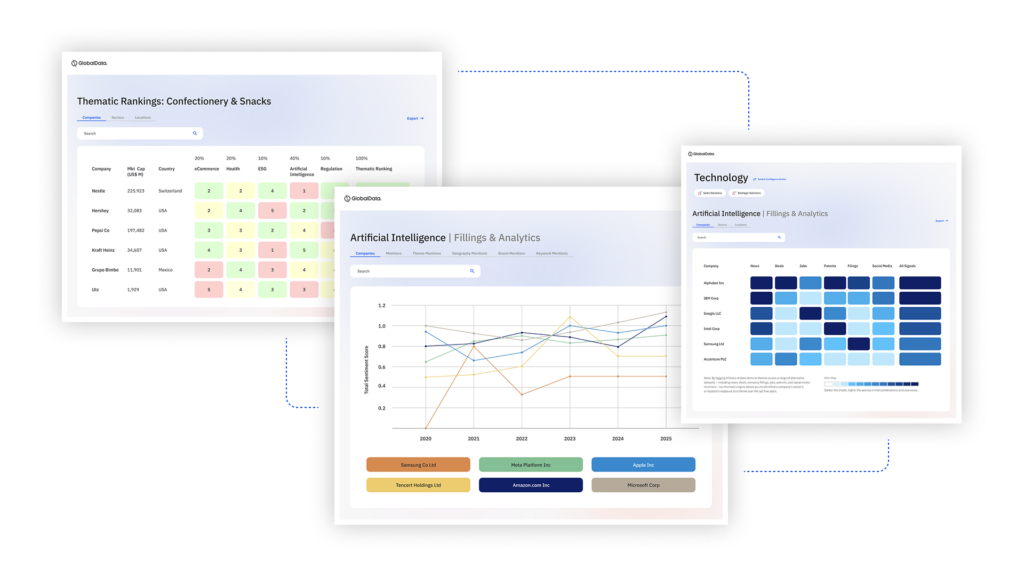
US Tariffs are shifting - will you react or anticipate?
Don’t let policy changes catch you off guard. Stay proactive with real-time data and expert analysis.
By GlobalDataAdvantages of this process includeminimising volumes of stock held at branches, so releasing space to permit a widercustomer “offer” at each branch, and minimising the need for unprofitable stockreduction sales. A relatively short period on the rail also helps ensure that the highquality of the garment can be maintained to the moment at which it is sold.
Integrated Activities
Etam, previously an independently operatedcompany in the UK, was acquired in 1997 by a Paris-based sister-company, which has furtheroperations in France, Spain, Belgium, Germany, Luxembourg, China and Italy. The Frenchcompany was already operating the “pull” system for stock replenishment, andcommonising the process was a logical step in integrating the two companies’ activities.This integration also means that the companies have ready access to each other’s mostpopular product lines to build an optimum customer choice.
In the previous “push” systememployed by Etam in the UK, garments were received in bulk and the complete shipment thendespatched to branches in volumes related to the estimated stock turnover of theindividual outlet. This created surpluses or shortages in certain sizes, colours orstyles, potentially reducing profit on the one hand or losing sales opportunities on theother.
The distribution centre was just that – aclearing house for the entire stock of each product line. Recognising the seasonal -“back to school” for example – nature and changing fashion trends of the garmentindustry, new lines are always in the pipeline, and it is important to be nimble injudging stock needs which could not be precisely controlled under the previous system.
With the new “pull” system,specific garments are replaced as the shops sell them. All branch sales and stockmovements are polled overnight, and fed into the company’s computer systems to generatestock replenishment orders ready for the distribution centre the next morning. The stockitem is replaced in the branch stock the following day. The object is to ensure that thebranch permanently retains an ideal stock level.
As a result, an intensive warehousingfunction has been added to the distribution role of the Boughton centre. Order pickershave a “shopping list” or, more correctly, picking sheet for each shop, set outin the precise order of stock location in the warehouse, and a logical progression is madedown the stock lines by the picker until the order is fulfilled.
Conveyors International carried out theinstallation of the original monorail storage system at the Boughton distribution centrenine years ago and, once a carefully developed plan for the changeover was approved earlylast year, CI needed to work to a very tight time schedule to completely strip-out theexisting equipment and build in the revised installation. In fact, stripping-out andrefitting the distribution centre took the company just four weeks, with no disruption ofsupplies to the company’s 216 retail outlets.
In the old system the warehouse wasequipped with a single-level overhead monorail transit system located on each of the twoupper floors of the three-floor warehouse to channel products from goods inwards throughbuffer storage to branch allocation and despatch.
To accommodate the warehousing functionunder the new scheme, the storage rails were installed as two-level systems, which doublesthe holding capacity of the rails.
Stock Flow
Stock flow under the new regime is asfollows:
Following quality inspection and checkingthat the specification of the garments matches the barcoded tag, and that quantities arecorrect, hanging garments are transferred to trolleys suspended from the monorail andmanually guided to their appropriate stock locations.
Following the receipt of each new garmentline, about 50 per cent goes direct to the branch allocation area where a sortationmachine sends the merchandise to channels dedicated to each of the 216 branches, providingthem with their basic allocation of the new line. This basic stock comprises one exampleof each size and colour for each store, though this would be varied on the basis of knowndemand history of a particular branch.
The balance of the new product shipmentwould be placed in its nominated stock area in the warehouse.
Stock pickers collect the picking sheet fora branch and, using the trolleys, move from location to location on the monorail to fulfilthe order. The rail passes the ends of aisles of hanging garments and the picker pauses atspecified aisles to collect the merchandise.
The computerised order system is”smart”, and if a store is submitting a regular order flow for a particular itemthen the system will automatically increase the requirement on the manifest. The pickingsheet is also compiled to represent a single “hanging set” – a recognisedshipping unit in the garment industry. Computer-generated data works out what mix ofgarments – from overcoat to blouse – constitutes a hanging set, the precise quantity thatwould fit the standard protective garment shipping bag. The sets are then transferred tothe despatch area for bagging and loading onto road transport vehicles.
Etam uses four transport companies, eachcovering defined regions of the country. They deliver the regional load to a depot wherethe loads are broken down for distribution by smaller vehicles to the individual shops.
Monorail System
Conveyors International supplied theCI-Meiko monorail system, supplementing where appropriate existing rail systems andinstalling the two-level hanging rails and re-organising the whole complex as awarehousing operation from a relatively simple transit system.
For direction changes the monorail systememploys manually operated universal switches and interchanges. To shift garments betweenfloors, powered incline conveyors are installed.
Commenting on this major reorganisation ofthe Etam distribution centre, distribution controller Keith Sansom says: “CI reactedvery quickly and helped minimise the disruption that is inevitable when stripping-out avast operation like this and rebuilding to the new specification in a period of just fourweeks. Their installation team worked very well with our people so that we could both meetour business objectives during the period”.
A further order placed with CI to extendthe conveyor installation has also been completed.
Operationally, a major amount of retrainingwas required for around 200 people to familiarise them with the vastly different functionof the warehousing and distribution operation and particularly in the order pickingactivity, which brought a large shift in the focus of the workforce. That these changeswere implemented so smoothly says much for the degree of co-operation between management,workforce and CI.
As a confident reflection of theintensified customer-orientated approach to its total business, Etam is progressivelyre-fitting and up-grading its shops – with about a third undergoing the transformationlast year alone.