In 1998, DAKS Simpson not only celebrated50 years of manufacturing at its Larkhall factory near Glasgow, but also the anniversaryof a working partnership which has lasted for more than half a century.
Coats Limited has been supplying thread tothe company since it moved into its current Scottish operation in 1948 – and today findsitself in the privileged position of supplying 100 per cent of the firm’s threadrequirements.
Both parties agree that the success oftheir relationship is down to many hours of hard work and an ongoing process ofimprovement which is set to continue well into the 21st century.
Coats supplies thread, zips and kicktape toDAKS’ factories in Larkhall and Polbeth where around 1,500 workers are employed in themanufacture of tailored garments for the DAKS retail brand and Marks & Spencer.
At a time when many companies are beingforced to transfer their manufacturing to offshore locations, DAKS has voiced itscommitment to UK based production. The firm sources the majority of its cloth from weaversin the UK and has pledged its long term support to many independents in this sector. Itwas this move towards consolidation of working relationships that led to the appointmentof a sole supplier two years ago.
LONG TERM PARTNER
“We selected Coats as our long term partner for a number of reasons”, says JimGlancy, general purchasing manager at DAKS. “What we were looking for was more thansimply a ‘thread supplier’, we were seeking a ‘thread manager’ who could work closely withour team, reduce the inventory and give us a ‘hassle free service’ which would leave usfree to concentrate on the management and development of our business”.
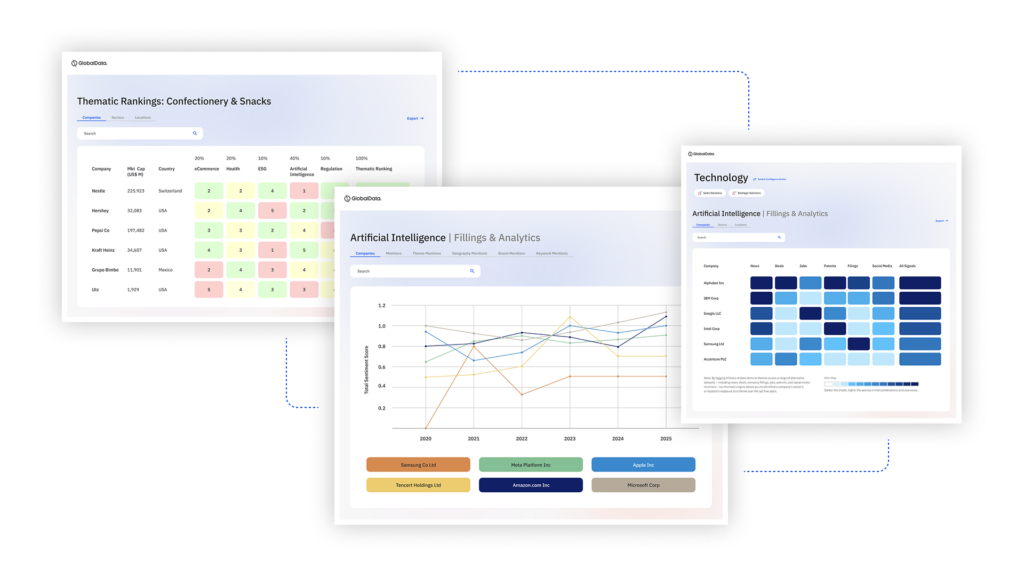
US Tariffs are shifting - will you react or anticipate?
Don’t let policy changes catch you off guard. Stay proactive with real-time data and expert analysis.
By GlobalDataDAKS is now in the final phase of anambitious three year, £4 million investment programme which has impacted across the wholeof its business, from management right through to planning, production and logistics.
One significant change emanating from thisprogramme was the company’s move from traditional flow line based manufacture with singlejob repetition, to a cellular manufacturing system where several tasks were doneconsecutively by the same operative. This development has enabled DAKS to offer a quickresponse service across its precision tailored men’s wear and ladies’ wear.
The change in manufacturing methods hasalso meant that Coats has had to consider the demands of DAKS’ highly flexible and oftenbespoke manufacturing approach when devising the most efficient solutions to its threadsupply management.
The company’s first step in ensuring asmooth interface between thread supply and manufacture has been to assign planner KarinMullen to the DAKS account.
Karin looks at the company’s threadrequirement on a week to week basis, receiving forecasts every Friday from the DAKSproduction team. From this she calculates the correct thread, zip and kicktape requirementto see the factories through the next 14 days.
“The key is to maintain the rightbalance so that products are available in the right quantities from accessible positionsand there is no dormant or dead stock”, explains Karin.
“The diversity of DAKS’ production andthe fact that they could be producing anything from a hundred garment run down to a singleitem means that the system must be flexible enough to cope yet ever mindful of the needfor thread efficiency”.
Karin’s close relationship with the companymeans that she has advanced knowledge of likely thread dye requirements which can bepassed on to the Coats dyeing operation at Newton Mearns.
Coats is also privy to an efficiency graphproduced by DAKS each month which charts how manufacturing is measuring up against keyperformance criteria. From this information areas where procedures may be streamlined andimprovements may be made can quickly be identified.
RATIONALISATION
With Coats’ help, DAKS has managed to rationalise dramatically its thread range from over600 shades down to just 110.
“DAKS are dealing with over 2000fabric types from delicate fine surfaced flannels to textured effect tweeds and richMerino wool, and the threads we are using have to complement the properties of thesefabrics perfectly”, says Jim Glancy.
“With Coats’ help we have been able tocover the whole spectrum of our thread requirements within 110 shades”.
The open working relationship also seesaccount manager Gordon Dowie liaising with contacts ranging from director through to shopfloor level.
“The supervisors on the productionlines respect Karin and my product knowledge and are able to approach us directly if theyhave a query. This is much more conducive to the prompt solving of problems than themhaving to liaise with us via one nominated contact within DAKS”, explains Gordon.
In addition to manpower support from Coats,DAKS also uses the company’s Stocklink and Metrelink efficiency systems, and its Kawabatatesting services. DAKS also has access to Coats’ technical team and can call upon itsservices if it encounters any problems which cannot be solved by its own internalengineering team.
“There is a real synergy between ourcompanies and this has helped us both to become more efficient in what we do”, saysJim Glancy. “Like Coats, we are receptive to constructive criticism and having suchan active two-way flow of information means that we can both become better equipped to getthe best out of the other party as a result.
“Over the last three years the wholedynamic of our business has changed and, thanks to the co-operation of Coats, we can nowcombine classic tailoring with quick turn around, enabling us to offer the best of bothworlds to our customers”, he concludes.