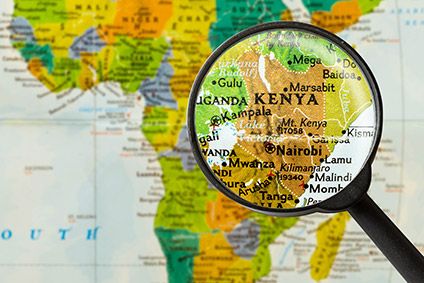
A reluctance by Africa’s clothing and textile industries to adopt new technology has not only slowed growth in the sector, but is also potentially pushing companies towards stagnation, an international conference has heard.
The three-day summit organised by the International Textile Manufacturers Federation (ITMF) took place last week in Nairobi – the first time the annual event has been staged in a sub-Saharan African country in the ITMF’s 114 years of existence.
The failure to embrace and adopt science and technology has led to African manufacturers being unable to compete with an incoming flood of second-hand clothes, many received from supposedly altruistic donor agencies, knocking African producers out of the sector and hindering efforts to revive the continent’s manufacturing base.
“Our markets still allow cheap second-hand clothes in. In most cases these clothes are dumped here in the name of charity. But most recipients or importers opt to make few coins from them, by putting them up for sale, choking the market and making the development of brand new clothes a hand sell. This distorts the demand supply chain of the new clothes,” says Jolly Sabune, managing director of the Uganda Cotton Development Organisation (CDO), calling for regulations to limit import of the second clothes.
The CDO is a government agency working under Uganda’s ministry of agriculture, animal industry and fisheries, charged with assisting with the production, processing and marketing of cotton in Uganda.
See Also:
A key problem is built-in inertia, following a lack of investment and evolution within the African clothing and textile sector from the independence decades of the 1960s to the 1990s
Navdeep Sodhi, a partner at the Zurich, Switzerland-based consultancy Gherzi Textil Organisation, says a key problem is built-in inertia, following a lack of investment and evolution within the African clothing and textile sector from the independence decades of the 1960s to the 1990s.
How well do you really know your competitors?
Access the most comprehensive Company Profiles on the market, powered by GlobalData. Save hours of research. Gain competitive edge.
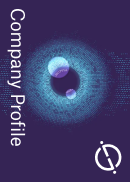
Thank you!
Your download email will arrive shortly
Not ready to buy yet? Download a free sample
We are confident about the unique quality of our Company Profiles. However, we want you to make the most beneficial decision for your business, so we offer a free sample that you can download by submitting the below form
By GlobalDataThat is a significant contrast to the changes that have taken place in other parts of the world, especially in Asia.
In a paper delivered at the conference, entitled ‘The Textile Industry in Africa: A contemporary perspective,’ Sodhi explains that even now the industry is still stuck with traditional operations and management practices that make African manufacturers uncompetitive.
Fragmented value chain
A major problem, the conference was told, is the continuing failure of African manufacturers to add value to basic fibre, notably cotton, which is produced in abundance on the continent.
Indeed, the Supply Chains and Business Models in Times of Rapid Change section of the conference was told that of the 2bn tonnes of cotton produced in Africa, the bulk is exported as a raw material. Only small shares are bought by sub-Saharan African textile manufacturers making traditional fabrics for local consumption.
“As a result, there is a fragmented value chain, with no integration with local economies,” says Sodhi.
For instance, African ring spinning capacity declined between 2010 and 2017, falling from 5.2m spindles in 2010 to 3.5m spindles in 2017, he says. China, by comparison, has 105m spindles, India operates 54m and Turkey some 8m spindles. African manufacturers have also been slow to acquire rotor spinning machinery.
He stresses that this supply chain disconnect can be addressed, especially as African cotton production is focused in West Africa, with two-thirds of output in French speaking countries such as Mali, Burkina Faso, Benin and the Ivory Coast.
Moreover, there has been some progress. “It hasn’t been all gloomy, as Africa’s shuttleless weaving and circular knitting capacity has shown some recovery from 14,000 weaving and knitting machines in 2011 to 19,000 weaving and knitting machines in 2017, even though investment is below the world average.”
Backward integration
Sunny Huang, group executive director of the Taiwan-based high performance fabric and garment supplier New Wide Group, says Africa’s role in the global textile and apparel supply chain is still negligible. This is because of low levels of innovation spurring production, as well as a failure to make and sell added-value finished products, he told delegates.
To remain relevant and grow the sector, Africa needs to learn lessons from regions that have developed fully established textile and apparel industries, with comprehensive backward integration, says Sun Ruizhe, vice president of the China National Textile and Apparel Council (CNTAC).
He explained the reforms that followed the death of Chairman Mao enabled China to become a key player in the global textile and apparel industry, but only because investments were made that enabled manufacturers to take advantage of the vision promoted by its leader Deng Xiaoping from 1978 to 1989.
“Thanks to innovation-driven developments, the textile industry has achieved remarkable results in technological innovation and transformation of scientific-technological achievements. Today, science and technology constitute the primary productive force in China,” Sun says.
African manufacturers need to follow the Chinese example by paying close attention to shifting trends in the apparel market, with consumers today having a “lack of patience and brief attention spans”
Moreover, African manufacturers need to follow the Chinese example by paying close attention to shifting trends in the apparel market, with consumers today having a “lack of patience and brief attention spans.”
“This means manufacturers and players in this sector need to think of how to satisfy fast-changing consumer needs.” And technology can help here too, he explains, with Internet-based marketing and research enabling smart manufacturers to tap trends and add value to their products.
Sun called on African players to be more flexible when planning output, and to integrate online and offline production, management and supply processes, adding that they need to make textiles with good design sense that are tailored to serve niche markets.
To do this, African manufacturers need to be more open to change: “Flexibility has enabled information technology penetration into every stage of the textile supply chain, including design, research and development, production, marketing and service,” he says.
“It has brought profound changes to the organisational mode, production mode and management mode of the textile industry, and significantly improved the ability of the textile supply chain to respond to the changing needs of consumers in China.”
And with structural changes taking place in the global value chain, with emerging markets becoming demand centres in their own right as well as production moving from higher-cost centres, he believes Africa, as a lower cost environment, is well positioned to take advantage. But only if it invests more industry and technology.
Sophisticated investment
Christian Schindler, director general of the ITMF, says such sophisticated investment in strategy and production equipment is needed to help the textile and clothing industry develop ‘mass customisation’ systems that allow major manufacturers to meet individual and often fast-shifting customer needs.
To achieve this requires a fourth industrial revolution, involving automation and data exchange in manufacturing technologies.
Manufacturers operating in Africa that adopt such smart systems can benefit in many ways he says, notably in saving energy, becoming more water efficient and hence environmentally sustainable.
Automated plants can work more quickly and reach markets faster with lower labour costs – with such disruptive technologies and innovations will be crucial to the future of Africa’s textile manufacturing
Automated plants can work more quickly and reach markets faster with lower labour costs, with Schindler adding such disruptive technologies and innovations will be crucial to the future of Africa’s textile manufacturing.
As a result, he expressed regret that shipments of spinning, texturing, weaving, circular knitting, flat knitting and finishing machines to Africa between 2008 and 2017 were still lower than other regions of the world.
And conservatism in African home markets does not help. Despite the emergence of e-commerce at the turn of the century, Africa continues to rely on store-based retailing for textile and apparel products.
“This means that sustainability is now in the form of a company’s share of e-commerce, which is enabled by new technologies that also permit the mass customisation of products,” he says. “The internet offers new potential here, and this is the trajectory that all of us must look towards.”
Automated worklines
Peter Santora, chief commercial officer of Atlanta, Georgia, US-based SoftWear Automation, warns that tight labour markets, rising wages and pressures to deliver short lead times with zero inventory is pushing textile and apparel manufacturers worldwide to automate. Companies that ignore this fact are at risk.
And real robotics are coming to the clothing sector. For instance, SoftWear’s Sewbot system enables one employee to produce more than 1,140 T-shirts a day. Previously, that work was done by 10 people who would produce less than 670 shirts, he says.
Indian manufacturers working with SoftWear have seen labour costs for producing a T-shirt tumble from US$0.40 with manual sewing to US$0.05 with its digital and robotic T-shirt workline, Santora explains.
“In China, it has come down from US$0.52 to US$0.09.” Moreover, the hourly labour cost of a robotised station is US$0.77 to US$0.33 per hour. “The expected global average labour cost in all major textile production countries is US$2.50 per hour. When you hear about automation or the use of robots, many people think of job losses, but the future of manufacturing is customised solutions,” Santora adds, stressing that because there “will also be human-machine interaction…there will need to be people to monitor interfaces.”
Given the reluctance within Africa’s clothing sector hitherto to adopt even more basic upgrades in technology and working methods, it may take years before such robotics to become widespread in the continent.
See also from this event: Experts point way ahead for African textile sector