
Istanbul Apparel Exporters Association (İstanbul Hazır Giyim ve Konfeksiyon İhracatçıları Birliği – IHKIB) is concentrating its efforts on the digital transformation of the apparel industry of Turkey during the unforeseen days of the pandemic.
Mustafa Gültepe, President of IHKIB, highlights the importance of IHKIB’s project called “From Design to Production: Digital Transformation of Apparel Sector in Turkey” in transforming the digital capacities of especially SME’s for the future. Gültepe says: “Apparel industry of Turkey is always capturing the correct ways and means of being competitive at all times, and digitalization, linked with sustainable fashion, became the key investment area for apparel companies of Turkey in these pandemic days”.
“The pandemic has changed everything, shaking the business from the top to the bottom. Digitalisation and 3D facilities for sampling to production to enable easy traceability and fast sampling has become essential due to the pandemic,” said Mehmet Kaya, Board member of IHKIB and General Manager of TYH Textiles.
Turkey’s apparel sector has understood the importance of digitalisation and e-commerce, with retailers selling more online over the past year, requiring quick deliveries to market, near-shoring, improved inventory management and innovation.
While Turkish investment in digitalisation has increased over the past year, the country’s apparel industry has long been investing in technology to retain its competitive edge as a more expensive garment producer, compared to Asian and African manufacturers.
German brand Hugo Boss has helped demonstrate how Turkey’s apparel sector can adopt the most sophisticated Industry 4.0 tech, with advanced factory in Izmir in Western Turkey being a high-profile example of good practice. Opened in 2015, it uses more than 1,600 tablets throughout the facility to track production in real-time, connected via artificial intelligence (AI) with semi- and fully-automated machines and robots.
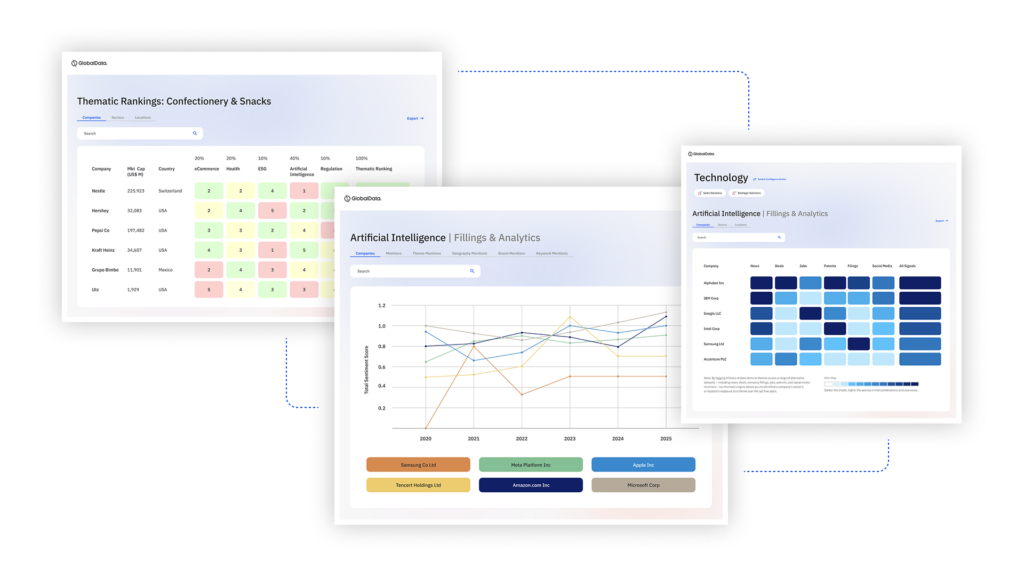
US Tariffs are shifting - will you react or anticipate?
Don’t let policy changes catch you off guard. Stay proactive with real-time data and expert analysis.
By GlobalData“The Hugo Boss facility is now the level Turkish manufacturers are increasingly at, as digitalisation gives speed and agility to the industry,” said Kaya.
He said fabric and textile producers across Turkey are also adopting Industry 4.0 technology “for high-tech fabrics and smarter products”.
The country’s educated and skilled workforce, strong ties with universities and technical colleges, and research institutions is further providing value-added advantages, from operating high-tech machinery to innovative designs.
“Turkey is focusing on value-added garments, and we provide most customers with our own designs. We have invested over the last decade in design institutes, while factories have invested in research and development and the hiring of designers,” said Cem Altan, board member of IHKIB and founder of Aycem Tekstil, based in Istanbul.
The digital shift has required the upskilling of workers and hiring of software engineers and specialists.
“Turkey used to buy software and technology from abroad – we still are – but the domestic software industry is taking off, and more people are joining the industry because of the opportunities to work with new techniques and innovations. Before we had just ‘blue collar’ and ‘white collar’ workers, now we also have ‘metal collar’ workers” able to work with the latest technology.
Business interactions and showcasing products has also become increasingly digital, further accelerated by the pandemic. “We used to visit our customers with big suitcases to show everything physically, now it is via a digital showroom or with a laptop. This has been a big change for the industry,” said Kaya.
Manufacturers are increasingly teaming up with technology providers to customise and develop innovative solutions. Silk, linen and cotton producer Mert Ipek, based near Izmir, produces some 40,000 metres of silk and 20,000 kilogrammes of linen per month. The company has recently invested in high-end technology that is fully automated at the factory, and has fully-integrated robotic dispensing machines at its laboratory.
“We have been working on this for two years, and are aiming to be fully Industry 4.0-integrated by the year end,” said Tahir Mert, general manager of Mert Ipek.
But for the company to successfully adopt new technologies for silk production in particular, technical cooperation has been required. “Our machinery is developed with the manufacturers to have the right modifications. It takes a lot of specialisation and knowledge,” said Mert.
Meanwhile, Turkey has become a hub for brands and retailers to experiment and develop new innovative fabrics.
The UK’s LiquidNano textile coatings brand DiOX for instance has carried out testing in Turkey on durable water repellent (DWR) coatings that use nano-scale silica dioxide technology as a finishing chemical. While efficacy testing was carried out at the UK’s Cambridge University, the tests in Turkey explored how the specialised coating works with different fabrics and how it can be processed.
With Turkish companies increasingly automated, cutting edge technology is being adopted across the country. For instance, Özak Tekstil, represented in IHKIB Board, based in Başakşehir, Istanbul, in May (2021) inked an agreement with US-based IT company Gerber to source its digital cutting technology. The Turkish ready-to-wear manufacturer cuts some 6 million pieces per year.
“By using digitalisation and technology, we don’t have quality issues, pattern issues, or second quality issues that much. With 3D technology, we are able to understand a garment’s fit better, and the new technology improves sustainability through less waste,” said Ismail Kolunsağ, CEO of Cross Textiles and IHKIB board member.
There is interlinkage between the adoption of new technology and the drive for more sustainability and circularity in the industry. “A significant part of new investment is in renewable energy and energy-saving technologies”.
Virtual catwalks have become more in vogue as well. “Once you have the design done on 3D, and present the garments on a virtual catwalk the customer better understands how a garment looks, and that can easily be converted into patterns sent via email. Most of our work is through automated management systems,” said Kolunsağ.