
Hong Kong-based yarn spinner Novetex Textiles is leading the charge towards sustainability with a HK$15m (US$1.9m) investment to help scale up a process developed by the Hong Kong Research Institute of Textiles and Apparel (HKRITA) to upcycle textile waste into yarns that can be reused to make garments. Chairman Ronna Chao explains more.
“This focus on sustainability has been perhaps the most important next step for us as a 40-plus-year-old company,” Chao tells just-style.
“In recent years, there has been increasing demand for raw materials from environmentally and socially responsible sources. With a limited supply, these types of raw materials have a relatively high price range compared to traditional sources. With the fact that our earthly resources are heavily drained, certain raw materials have become increasingly expensive as well. In this context, it makes an urgent case for us to recycle these precious materials and support the practice of a circular production system.”
Located in Tai Po, Hong Kong’s New Territories manufacturing hub, The Billie System is a mechanical recycling process that does not consume water, emit wastewater, or produce chemical waste. Located in the first textile mill to open in Hong Kong in almost half a century – and named in honour of Novetex founder Mr Kuang Piu Chao, who was nicknamed “Billy” – it has been several years in development.
“Considering the state of our environment, and how our industry contributes to the problem, The Billie System sets an example of what can and should be done. To support the circular economy as a positive way forward, we’re providing a concrete method of putting that into practice,” Chao adds.
While the concept of upcycling is not new, some methods used to create recycled yarns or fibres use considerable volumes of water and chemicals to sanitise and decolourise fabrics.
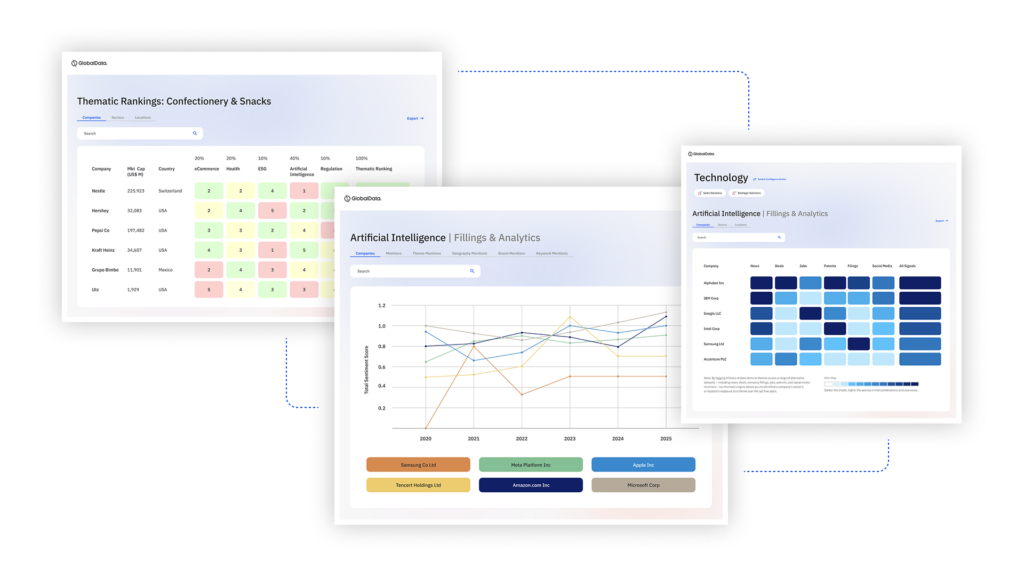
US Tariffs are shifting - will you react or anticipate?
Don’t let policy changes catch you off guard. Stay proactive with real-time data and expert analysis.
By GlobalDataNow encompassing three production lines, The Billie System combines both new and existing technologies to produce recycled fibres from textile waste. Once the rigid parts such as zippers and buttons are removed, items are automatically sorted into different colours. From here they pass through the mechanical recycling process and are broken down into fibres, passing through two stages of UV light sanitisation before being formed into slivers.
These slivers of recycled fibres are sent to Novetex’s Zhuhai facilities in Southern China where they are blended with virgin fibres to ensure the best quality yarn for garment production, before being spun into yarn.
Established in 1976 and part of the Novel Group, Novetex Textile Limited has more than 500 employees and operations in China and Asia along with its headquarters in Hong Kong. The company’s factory in Zhuhai houses four spinning mills and one dyeing mill, making a total of 30 production lines with an annual capacity of 5m kg of yarn.
The Billie System was initially conceived to tackle the textile waste generated in Novetex’s own yarn manufacturing process, but as the solution progressed, “we realised there was a potential and a need to make a larger impact.
“The Billie System supports our existing operations by offering current and potential customers an opportunity to enter a closed-loop system of production. Ideally, their textile waste is processed into upcycled fibre which can be used to spin yarn to create new products.
“As sustainability increasingly becomes more of a priority for brands, it’s important for us to be able to offer a sustainable option, and it feels purposeful that we can do this while raising awareness for the problem of textile waste.”
Challenges in closing the loop
Among the challenges encountered on the way to a more circular process is the collection of “meaningful quantities of certain qualities of textile waste to maximise efficiency of The Billie System.” Another is “reaching customers who are willing to participate.”
Chao notes: “Companies that have made public commitments to sustainability are of course, easier to work with.”
Applying textile upcycling practices also required the “shift in mindset which leads to a shift in behaviour.”
“Everyone needs to play a part in order to move the needle” – Ronna Chao
“Recycling aside, affecting change in design, production and merchandising patterns as well as consumption habits and actioning on waste reduction with different innovative solutions from various sectors are essential,” Chao explains. “Everyone needs to play a part in order to move the needle.”
Another issue is the mill’s current location in Hong Kong – and consequently, its limited capacity – versus the much larger problem of textile waste that exists in many major cities around the world.
“Expanding The Billie’s capacity so we can make a bigger difference is certainly part of our vision. In Hong Kong alone, there are over 370 tonnes of textile waste going to landfills every day. The Billie can currently process up to three tonnes per day, which means that we can only work with less than 1% of the waste.
“We want to study how to best meet the needs and business opportunities of various locations and industries, which may lead us to scale up beyond the current operation.”
Future plans
Efforts to accelerate its capabilities may also eventually lead to cross-industry collaboration, Chao adds.
“Our goal is to build and expand a collaborative network to effectively address the issue of textile waste. While we pursue natural opportunities through our current customers, we are also keen to establish new partnerships for sustainability with those beyond the textile and fashion industries.”
Chao adds Novetex has had “fruitful discussions with numerous players in the hospitality and food and beverage sectors,” noting such companies are interested in trialling programmes for their textile products such as uniforms, bedsheets and blankets.
“The Peninsula Hotels operated by The Hong Kong and Shanghai Hotels Group have provided us with 1,000kg of cotton which The Billie has processed into fibre to be further spun into yarn,” she adds, noting another luxury hotel chain has provided about 300 pieces of 100% cashmere blankets.
“The most ideal outcome for us would be a fully closed-loop lifecycle whereby textile waste is upcycled into yarns that are used to make products for the owner/producer of the original textile waste.”
Click here to read more of just-style’s coverage of The Billie System.