
The scientists from the North Carolina State University printed ink on cotton fabric to make denim fabric digitally which resembles six different styles of jeans. When they asked a team of textile experts, they found that overall, the samples made with the computer and printer were a good match on average for denim made using traditional, more labour-intensive methods.
The findings were published in the Journal of Imaging, Science and Technology.
The researchers said certain styles of jeans were easier to replicate using inkjet printing than others, and certain features, like colour, were more easily replicated. With further study, researchers said they expect digital printing will be a viable method for making new jean products in the future, with less waste.
Speaking with The Abstract, an NC State publication, study co-author Lisa Chapman, associate professor of textile and apparel technology and management at NC State, and lead author Ming Wang, a former graduate student at NC State, said the study was prompted by the water-intensive nature of jean production.
Inkjet printing, Chapman said, though considered an emerging technology with a small market share in textiles, uses less water and energy and is a print on demand process.
“So you’re eliminating some of the steps in the colouration process, and you have unlimited colours. To print using the traditional process, as you increase the number of colours, you increase the cost of the design. Inkjet printing is not like that; 200 colours is the same as two colours in cost.”
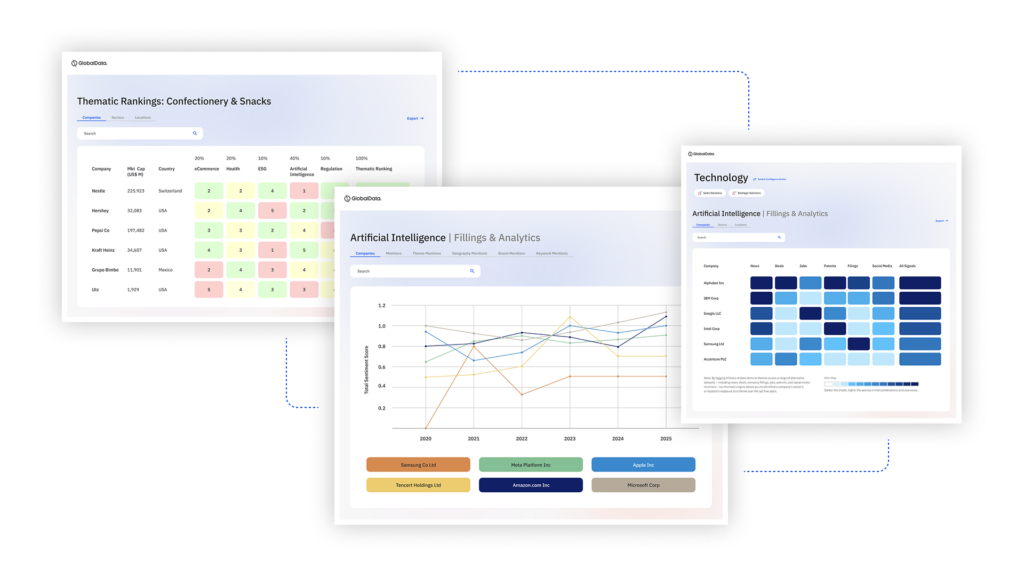
US Tariffs are shifting - will you react or anticipate?
Don’t let policy changes catch you off guard. Stay proactive with real-time data and expert analysis.
By GlobalDataThe digitally created denim samples were assessed by 12 industry experts and Wang said they were deemed to have good colour quality but the line quality and texture were difficult to achieve, possibly due to the high ink penetration of traditional dyeing.
“If someone could solve the ink penetration problem, I think we could mass-produce denim products with a high-speed printer. It could bring the cost of production down. However, since mass production is not quite realistic yet, we could use digital printing for high-end denim products like home textiles or apparel. For kids, they are growing every day, so you could have something that looks like jeans,” Wang told the publication.
Chapman added: “While there is a pretty high learning curve for digital printing, there are also advantages with reduced energy use, chemicals, and water waste when we’re comparing digital printing to screen printing. The dot-com market is also going to drive digital printing. We’ll be looking at new technologies that speed up the production cycle to get goods to consumers faster.”