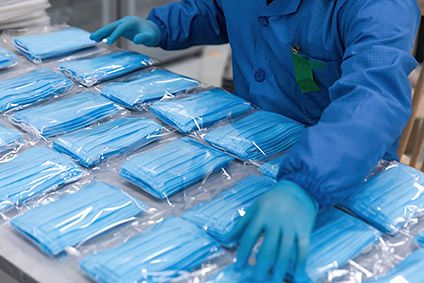
Texollini, Chargeurs*PCC Fashion Technologies, and Crystal International are among the latest fashion firms to mobilise their production facilities and supply chains to help address the global shortage of personal protective equipment (PPE), including face masks and hospital gowns, amid the coronavirus (Covid-19) pandemic.
24 July – Texollini
LA-based vertically integrated manufacturing facility Texollini has introduced the T19 Performance reusable face mask. Designed, knit, dyed, printed, sewn and packaged in the US, the mask utilises Texollini’s proprietary micro denier three-dimensional spacer fabric, which is extra thick to provide ample filtration and shape without the need for layers, according to the firm. The mask, which is intended for recreational protection, safety and general health, can be machine washed while the antimicrobial Bac-Shield textile finish helps kill odour causing bacteria and germs.
16 July – Chargeurs PCC
Chargeurs*PCC Fashion Technologies today announced the launch of its first US consumer-facing division, Lainiere Health & Wellness, as well as a direct-to-consumer e-commerce website offering the new division’s collection of protective face masks. Since the beginning of the coronavirus crisis, Chargeurs has shifted a significant portion of its global textile production toward health and wellness–related protective equipment. To support US manufacturing, Chargeurs will start producing face masks at its Troy, Ohio, factory by September.
9 July – Crystal International
Apparel manufacturing giant Crystal International Group has extended production to manufacture fabric face covers. The non-medical grade face cover has Bacterial Filtration Efficiency (BFE) standard over 95%, meeting the standard of ASTM F2101 and EN 14683, and can be hand-washed and reused up to 60 times.
7 July – Gap Inc
Gap Inc has launched a B2B product programme focused on offering large organisations high-quality reusable, non-medical grade cloth face masks to supply to employees as they return to work. The Centers for Disease Control and Prevention and the World Health Organization are still urging people to wear face masks or coverings when outside the home. For businesses that plan to re-open, Gap Inc is offering a selection of non-medical face masks in mass quantities –- starting at a minimum order quantity of 100,000 units – and in a variety of colors and swatches. To date, the programme has sold about 10m non-medical grade face masks to employers, including the City of New York and the State of California.
2 July – Eurofins Softlines & Leather
Eurofins Softlines & Leather’s Spanish laboratory (Eurofins Textile & Footwear Testing Spain) has been accredited by the European Commission as a Notified Body for PPE certification. The certification covers protective clothing, safety shoes, and protective gloves designed for different levels of risk and protection, including harmful biological agents, mechanical risks, protection against heat or fire, and static electricity among others.
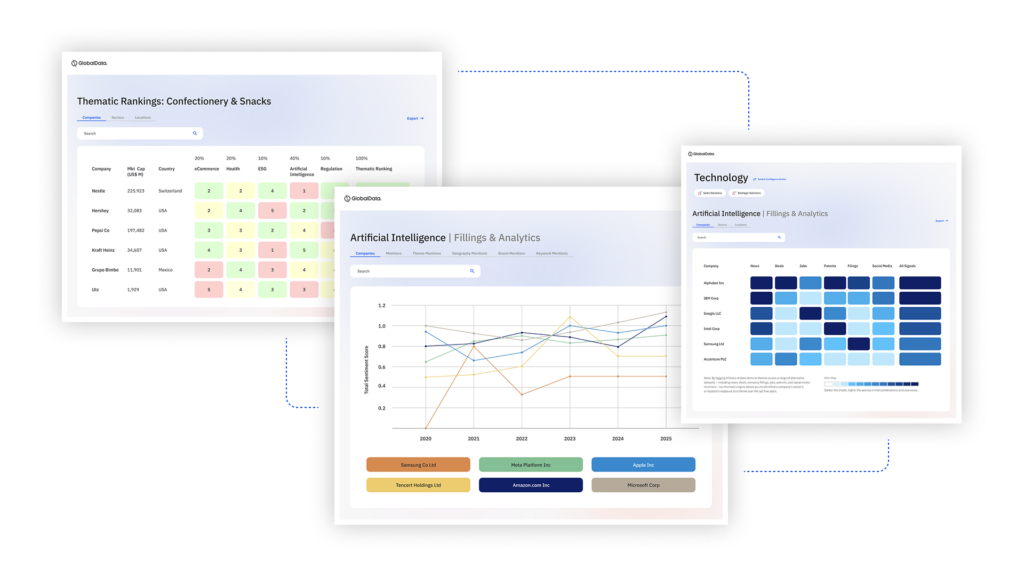
US Tariffs are shifting - will you react or anticipate?
Don’t let policy changes catch you off guard. Stay proactive with real-time data and expert analysis.
By GlobalData23 June – Epic Ethiopia mask production
Hong Kong-based garment manufacturing giant Epic Group has begun commercial production of surgical masks at a brand new facility in Ethiopia. Starting from July, Epic Ethiopia will have a production capacity of 6m of the nonwoven polypropylene fabric 3-ply masks per month. Operating out of the Hawassa Industrial Park, the company emphasises its two-step quality control process that involves raw material inspection at source, and inline visual inspection during the production process. Production takes place on fully automated machines, with no human intervention in handling the masks for superior hygiene. Manufacturing is also in a temperature, humidity, particle controlled environment adhering to ‘Clean-room class 100,0000 standard (ISO-8 equivalent).
17 June – Archroma/Liberty Textile Mills Limited
Archroma has joined hands with healthcare textiles producer Liberty Textile Mill Limited to produce PPE in Pakistan. Archroma provides a complete set of specialty chemicals required to produce PPEs, in particular in the area of antimicrobial and barrier coatings. The project will assist in enhancing medical standards in hospitals, isolation centres and intensive care units, in Pakistan and, in the longer-term, worldwide
12 June – Ciel Textile
Ciel Textile has shifted production chains and repurposed fabric on hand to produce, every month, more than 3.5m washable and reusable barrier masks in Mauritius, Madagascar, and India. With the support of its research and development teams, Ciel Textile developed a multi-layer, washable and reusable mask with an innovative waterproof outer layer and absorbent inner layer designed to minimise the spread of Covid-19. By producing masks, Ciel Textile said it supports frontline and essential workers while ensuring it can sustain salaries to employees. 20% of the firm’s workforce has been re-allocated to mask production, with the company having donated 250,000 masks to NGOs and local authorities since March. Today, more than 100 fabric designs are available for B2B clients worldwide.
4 June – Cone Denim
Cone Denim is transitioning a portion of its loom capacity to produce Maxima medical fabrics for its sister division Burlington. President Steve Maggard said: “The Cone and Burlington technical teams have been working closely to quickly transition a portion of looms in our Cone Denim Yecapixtla operation in Mexico to produce Burlington medical fabrics. Production is set to ramp up in June.”
4 June – Do The Right Thing (DTRT) Apparel
Ghanaian apparel manufacturer DTRT has partnered with the country’s government to help develop a domestic source of PPE. The firm reconfigured its factory to make it safe for workers and switched production to face masks, gowns, protective suits, and other medical garments to help protect frontline workers. To date, it has produced more than 1m masks and other PPE items to be distributed by the government. DTRT has also invested in specialised seam taping equipment to make medical-grade coveralls and plans to transition into the production of medical-grade PPE permanently, to offer alongside its core sports and lifestyle wear products. It also plans to scale up production to provide support to other African countries and wherever else there is a need.
3 June – Burlington/Tilley Endurables
Burlington and Tilley Endurables have joined forces to provide isolation gowns for healthcare workers in Canada after Tilley pivoted its idle sewing capacity from hats to medical isolation gowns. Utilising fabric from Burlington, which produces the Maxima line of medical fabrics, Tilley has produced more than 5,000 isolation gowns to date, primarily supplying long-term health facilities within the Toronto East Health Network and more recently dental facilities.
2 June – Istanbul Apparel Exporters Association(IHKIB)/Istanbul Textile and Raw Materials Exporters Association (ITHIB)
UK Fashion & Textiles Association (UKFT) members can apply for 50 free face masks per company to help the sector return to work thanks to a donation by the Istanbul Apparel Exporters Association (IHKIB) and the Istanbul Textile and Raw Materials Exporters Association (ITHIB). The masks are not PPE and have not met any performance testing but are suitable for general protection at work. The masks will be distributed on a first-come, first-served basis, with preference given to UKFT members.
1 June – Thai Son SP Ltd, Co.
Vietnamese cut and sew knit-wear company Thai Son SP Ltd, Co. has started to produce plain cloth face masks with anti-bacterial, water repellent, anti-UV fabric for personal use utilising its own in-house fabric.
29 May – Allied Feather & Down
Down supplier and processor Allied Feather & Down is entering its fourth month of mask production, with the company’s bedding division now making masks globally, manufacturing reusable cotton masks in its Los Angeles, Montreal, Czech Republic, and Asian production facilities. In April, the global supplier of down and home bedding began the conversions of its bedding manufacturing facilities in Asia, Europe, and at a new facility opening in Montreal. Allied has now gone from shipping between 10,000 to 15,000 masks a day, to providing millions of reusable cotton masks to service industry providers. By the end of May, Allied will be shipping more than 3m masks to prominent hotels and resorts, with the ability to add capacity as needed.
28 May – Eastman Staples
UK garment and textiles supplier Eastman Staples has provided vital equipment to manufacture PPE for healthcare industry after receiving a GBP300,000 (US$370,461) loan from HSBC UK through the Coronavirus Business Interruption Loan Scheme (CBILS). The firm traditionally supplies a range of equipment such as sewing machines, fabric and textile tools to clients across the garment industry but the six-figure funding package has enabled it to source and supply a range of equipment and machinery to clients. To date, Eastman Staples has provided equipment including sewing machines, chairs, garment rails and mannequins.
27 May – Beverly Knits/Brother International Corporation
US circular knitter Beverly Knits has received five Brother S7250A-403 single needle lockstitch industrial sewing machines from Brother International Corporation which will allow Creative Ticking, the cut and sew division of Beverly Knits, to significantly increase its current face mask production numbers. The face masks will be supplied directly to the US Department of Health and Human Services (HHS). Beverly Knits has currently partnered with 30 other companies in the textile industry across the US to produce face masks for HHS. The goal is to produce up to 2m masks per week.
27 May – Huntsman Textile Effects/Bao Minh Textile
Huntsman Textile Effects and Vietnamese woven fabric producer Bao Minh Textile are collaborating to produce fabric that meets the stringent performance standards required of isolation gowns. Bao Minh Textile will initially treat 760,000 metres of woven fabric with a carefully curated combination of Huntsman Textile Effects barrier effect solutions and auxiliaries. This fabric is sufficient to produce 345,000 high-grade isolation gowns.
26 March – Shima Seiki
Japanese flat knitting solutions provider Shima Seiki has produced 8,000 3D knitted masks for use at elementary schools and junior-high schools (primary and intermediate schools) in Wakayama Prefecture where the company is based. The masks are produced at Shima Seiki headquarters by request of the prefectural government of Wakayama, based on knitting data for one of several types of masks released by the company since 19 March. The knitted cotton masks can be washed and reused repeatedly. Shima Seiki noted, however, unlike common non-woven surgical masks, knit masks do not have virus- and pollen-filtration functionality. Their main purpose is to contain spray from coughing and sneezing, and for reducing exposure to allergens.
25 May – Fast Retailing
Fast Retailing will donate 1m isolation gowns, 4m masks, and Uniqlo AIRism functional innerwear items to medical institutions around Japan. Fast Retailing will enlist its manufacturing partners in procuring the medical-grade gowns and masks and will supply them directly to entities that most need them starting from early June. Gowns and AIRism items will be provided to government-designated infectious disease centres, university hospitals for the critically ill, and polymerase chain reaction test centres, among others that are helping bolster virus detection. In addition, the company has set up a dedicated desk to handle requests for masks, so it can better assess needs and offer the necessary support. On 26 March, Fast Retailing announced that it would donate a total of 10m masks to medical institutions in Japan and abroad to support the fight against Covid-19. To date, the company has provided these items to 19 countries and regions where it operates. It has donated more than 1m masks and 200,000 isolation gowns so far to medical institutions in Japan.
22 May – Nine Line Apparel
American lifestyle brand Nine Line Apparel has partnered with Gerber Technology and Top Value Fabric to develop several types of protective masks. The face coverings include a 100% reusable, medical grade mask of medical grade TPE. By leveraging two multi-ply GerberCutters and a multi-ply GerberSpreader at the Integrated Textile Solutions facility, Nine Line is able to produce 2,000 masks and 100,000 replacement filters per day with the capacity to produce up to 5m masks and 50m filters in one month. In addition to the reusable masks, Nine Line is also working with a fellow US manufacturer to provide consumers with a one-size-fits-all mask at cost.
19 May – Hyosung
South Korean fibre giant Hyosung has repurposed its facilities to increase the supply of Creora elastane to the global mask market by 20 times in a move that can make ear loops for several billion face masks per month. Elastane is primarily used for making the ear loops and head straps to make the mask fit properly and comfortably on the face. As a growing number of consumer apparel and accessory manufacturers around the world are switching gears to make face masks to help with the PPE shortage, the surge in production has made face mask component supplies, such as ear loops, scarce.
19 May – Hygiene Austria
Newly founded Hygiene Austria, of which Austrian cellulosic fibre producer Lenzing holds 50.1% and Palmers Textil AG 49.9%, has started the production of face masks in Austria. The product range includes mouth-nose safety masks, FFP2-masks as well as coloured face masks for children. In addition, the firm has decided to start producing face masks at the Lenzing site in Grimsby, UK, due to the large demand for protective items in Britain. The first production machines will be installed this month with a view to starting production at the end of May/early June with a monthly capacity of 10m pieces. The move is expected to create 60 new positions at the site within the next three months.
18 May – Dow
Dow has collaborated with nine key partners across a number of industries to develop and donate 100,000 isolation gowns to help frontline workers in Texas, Louisiana, and Mexico. The gowns are made with polyethylene nonwoven coated with a layer of polyethylene film made with resin donated by Dow and conform with ASTM and ANSI standards. They are also labeled in compliance with FDA guidance on non-surgical apparel. The 100,000 AAMI Level 2 gowns will be distributed equally to government agencies in Mexico and in the states of Louisiana and Texas.
14 May – Brandix
Sri-Lankan apparel manufacturer Brandix has exported the first consignment of 200m face masks to the US. The fabric used for the face masks was produced in Sri Lanka, while the chemicals used for the antimicrobial finish were made in the United States. The face masks have been manufactured combining the efforts of over 15,000 of the company’s associates and an extended network of several supply chain partners in the country. The face masks, produced as 3-ply and of cotton-based fabric with antimicrobial finish, are stretchable for a better fit and meet stringent hygiene standards.
14 May – Allied Feather & Down
Down supplier and processor Allied Feather & Down has tapped its bedding division to manufacture of cotton face masks. The firm’s 80,000 sq ft bedding division has switched a large portion of its production over to face masks, using the tightly woven, allergen-barrier cotton usually reserved for fine pillows and comforters to make breathable, washable face masks. Allied said it now employs more people than it did before the pandemic, and is producing approximately 10,000 masks per day, with plans to scale up in the coming weeks. The masks are designed for general use and are being sold to hospitality, retailers and direct to consumers, with Allied donating a “large portion” to shelters for the homeless and front-line personnel. The firm has also partnered with Fuze biotech to treat the masks with a proprietary fibre infusion that creates a protective barrier. The barrier remains effective if CDC guidelines on washing reusable masks cannot be observed, it said.
14 May – Bolger & O’Hearn
Speciality chemical producer Bolger & O’Hearn has donated 400 pounds of hand sanitiser to Rhode Island’s Lifespan health system. The hand sanitiser will be used throughout the Lifespan system to help reduce the spread of Covid-19. The gift is the third large donation of hand sanitiser Bolger & O’Hearn has manufactured in its Fall River, Massachusetts, plant since the crisis began. To make these donations – which now represent over 1,300 pounds of hand sanitiser and would equal 2,600 individual 8 ounce bottles, according to the firm – Bolger & O’Hearn has diverted part of its manufacturing capability and tapped the company’s supply chain. The company plans to continue sourcing materials to manufacture and donate hand sanitiser to front line workers in New England and is also working with other US textile industry players to develop medical textiles and PPE including masks, gowns, bed coverings, hospital room drapes. In addition, employees at Bolger & O’Hearn are making masks from test fabric that has been treated at the plant with the firm’s barrier DWR’s. These masks are being given to employees, family, friends, customers, and area first responders.
14 May – YKK
Fastener manufacturer YKK USA has expanded its product offering to supply US manufacturers producing PPE. Its latest offerings include a series of products designed to reduce ear discomfort hen wearing a face mask, elastic tape for face mask manufacturers, and plastic and metal snaps, hook and loop fasteners, and plastic cord stoppers for medical face shield manufacturers.
13 May – VF Corp
VF brands have donated more than US$3.2m worth of products providing warmth and protection to frontline healthcare and essential workers. Donations include 40,000 pairs of Vans shoelaces for face masks and 1,475 pairs of Timberland PRO nursing shoes. The group was also able to take advantage of the existing expertise of Dickies and VF workwear brands, which already manufacture protective gear such as scrubs, lab coats, and disposable coveralls, to help the company pivot quickly to making isolation gowns. Last month, VF and Dickies began producing medical gowns for US healthcare workers with the capacity to manufacture 3.4m gowns by September. The gowns will be distributed to communities throughout the US in cooperation with federal and state government leaders. VF teams are making other forms of PPE as well, bringing PPE production to 3.6m total pieces, including 250,000 Vans canvas face masks, 15,000 surgical masks, and 1,600 face masks.
13 May – Lucky Brand
Beginning in March, in response to the need for PPE, Lucky Brand coordinated efforts across local apparel brands and vendors to procure, produce and educate consumers on non-medical face masks. The brand first partnered with Suay Sew Shop’s mask initiative, providing denim fabric cuttings, funds and sharing DIY mask pattern templates with its consumer base. Lucky Brand next worked with one of its LA-based factory partners, New Fashion, to provide over 6,000 masks to be included, at no cost, in customer’s online orders, before launching the Give 5 Get 5 mask purchase programme that enabled customers to purchase a pack of five masks and donate an additional five to those in need. Lucky Brand said by the end of this week, it will have donated more than 20,000 masks to its charitable partners.
11 May – Bella+Canvas
Wholesale apparel manufacturer Bella+Canvas has pivoted production as a response to Covid-19, converting its cutting manufacturing floors and retooling its machines from making millions of T-shirts, to up to 100m face covers a week and is prepared to further increase production output. The face covers are made from Airlume combed and ringspun cotton, eco-dyed using Blue Sign Certified non-toxic chemicals, and 100% of the scraps are recycled. The firm has committed to donating at least 5m face covers to organisations directly serving the homeless, healthcare frontliners, first responders and underserved communities, and through a partnership with the United States Conference of Mayors, is donating 1m face covers, which allows 1,400 US mayors to obtain and distribute to their communities. It has also volunteered to join the Textile Coalition, working with the White House Coronavirus Task Force to help produce heavily engineered masks and is prepared to make 1.5m masks per week, and is partnering with the National PPE Coalition to build a supply chain for medical and non-medical PPE.
11 May – Amann Group
Thread manufacturer Amann Group is producing FFP2 certified respiratory masks that have been approved for medical personnel. The move sees Amann Group support the Hauber Group, a founding member of the FIGHT consortium, which aims to establish a resilient mask value-added network in Germany. Distribution is carried out by the state of Baden-Württemberg.
8 May – Gerber Technology/Professional Clothing Industry Association Worldwide (PCIAW)
Gerber Technology is partnering with PCIAW to increase the production of PPE in the UK. Through its PPE Task Force, Gerber has helped more than 1,200 manufacturers worldwide to convert their manufacturing capabilities to PPE production.
7 May – NC State/IFAI
NC State’s Wilson College of Textiles has partnered with IFAI — with sponsorship from IPC, SEAMS and SPESA — to create a series of webinars on PPE production and design. Webinars include an introduction to PPE production, nonwovens technology in the production of PPE, and principles of air filtration materials and design. View the IFAI list of events to learn more about the webinars and to register.
7 May – Coal Headwear
Coal Headwear has shifted its manufacturing operations to produce face masks. The company is working to support brands and small businesses by making branded masks to sell and is offering the first stage of non-surgical masks, available in packs of three, for purchase online. As safety measures ramp up, the company is also working on additional, higher-end versions of the face mask with filtering systems.
7 May – Coats Digital
Coats Digital, the software business of industrial thread maker Coats, has launched an initiative to support manufacturers switching part of their production facilities and supply chains to PPE. PPE Fast Start encompasses versions of Coats Digital’s software solutions for apparel manufacturers, including FastReactPlan production planning and control solution and GSDCost, the International Labour Organisation (ILO) accredited fact-based solution to establish and optimise accurate time and cost benchmarks for garment costing. It also includes a Fast Start for PPE version of IntelloCut, the real-time, automated fabric planning solution for optimised fabric utilisation which gives manufacturers complete control over fabric usage in the cutting room. All three of the PPE Fast Start solutions have been configured to support rapid, remote implementation and can be fully operational in a matter of weeks, the firm said. In addition, it is also launching a customer investment fund (CIF) to support manufacturers switching to PPE production which it said will “significantly” reduce the one-off implementation costs of these Fast Start for PPE projects.
6 May – Vidalia Mills
Vidalia Mills, the leading North American maker of yarns and denim fabrics, has teamed up with Keep it Here, a major Los Angeles-based manufacturer of T-shirts, jeans, and other clothing, in a new joint-venture to manufacture and distribute surgical masks, gowns, and face masks to assist medical professionals in limiting the spread of the Covid-19 virus. Vidalia Mills has purchased one automated surgical grade mask-making machine, along with two automatic N95 high-protection mask-making machines, which will be installed in a new cleanroom facility under construction at its plant in Louisiana. The machines can produce up to 100m units annually. The company has also deployed 20 high-speed weaving looms to make lightweight cotton fabrics for the production of medical gowns and consumer face masks to be cut and sewn at Keep it Here in Los Angeles. The materials will be anti-viral and anti-microbial infused, and made with BASF’s e3 sustainable cotton fabrics.
5 May – Crystal International
Apparel manufacturing giant Crystal International Group has distributed more than 180,000 fabric and medical masks from its knit, intimates and denim factories in Vietnam, China and Cambodia, as well as its Hong Kong headquarters, to workers’ families and local communities. This is in addition to the masks provided to its own employees.
4 May – Nike
Nike will partner with non-profit Good360 in the United States and local organisations across Europe to donate more than 140,000 pieces of footwear, apparel and equipment globally. Specifically, the sportswear giant is donating 30,000 pairs of Nike Air Zoom Pulse to health systems and hospitals in Chicago, Los Angeles, Memphis and New York City, and within the Veterans Health Administration. An additional 2,500 pairs are being donated to hospitals across Europe, including Barcelona, Berlin, London, Milan, Paris and in Belgium. Unveiled in November 2019, the Nike Air Zoom Pulse is the firm’s first shoe designed for medical workers. In addition, approximately 95,000 pairs of soccer socks offering mild compression will also be delivered through Good360 for healthcare workers in Los Angeles and New York City.
4 May – Style Cheat
Online women’s fashion brand Style Cheat has repurposed its factories to produce PPE. For every KN95 mask sold, Style Cheat will donate a medical-grade mask to front line workers, and customers can choose to buy masks for personal use or to donate these to staff. According to the firm, 5,000 personal masks were purchased in four days – meaning 5,000 have been donated, in addition to the 2,000 donated by consumers. Style Cheat is also manufacturing medical scrubs and gowns which are made in its factory in Romania.
2 May – Brandix
Sri-Lankan apparel manufacturer Brandix has begun to produce personal protective wear for health sector professionals on a small scale at some of its facilities in Sri Lanka.
30 April – Fast Retailing
Fast Retailing will donate 200,000 isolation gowns to medical institutions in Japan along with Uniqlo’s functional innerwear AIRism items, after receiving feedback that wearing the items under protective clothing and isolation gowns helps reducing stuffiness and discomfort.The isolation gowns have been procured from Fast Retailing’s manufacturing partners in China and will be provided to core hospitals and other institutions involved with the Covid-19 response. On 26 March, Fast Retailing said it would donate 10m medical masks, mainly for use at medical facilities and other organisations around the world, including Japan. Donations to 19 countries and regions have already been confirmed, and most deliveries completed. In Japan, the first 350,000 masks were provided to the government’s mask team in the middle of April, and the company expects to complete delivery of more than 1m masks by mid-May.
30 April – Cifra SpA
Italian textile manufacturer Cifra SpA has engineered and produced a hi-tech range of protective masks called Warp-Mask. Engineered by Cifra WKS system, Warp-Mask is a high-tech double-layer, run-proof and water repellent mask, made with polyamide (80%) and Lycra (20%) multifilament yarn. The fabric is doubled for a more compact and ultra-run-resistant structure and uses HeiQ Eco-Dry technology, which offers fluorocarbon-free durable water repellence (DWR) and makes the masks machine washable and thus reusable.
29 April – HanesBrands
HanesBrands is using its apparel design and manufacturing expertise to produce more than 20m medical gowns to be distributed by the US Federal Emergency Management Agency to hospitals and healthcare facilities. Hanes has already produced and delivered more than 60m cloth face coverings for the US government and is ahead of schedule to deliver more than 320m of the washable 3-ply all-cotton face coverings. The company is also rapidly securing additional manufacturing capacity to meet surging demand for face masks and other garments from consumers, retailers and business-to-business customers, including employers preparing to reopen business operations.
29 April – Gerber Technology
Gerber Technology has developed a new software package to help manufacturers convert their supply chains to produce PPE. The firm’s PPE Retooling Package includes an end-to-end suite of software and a specially configured PPE Edition Gerber Paragon cutter with optimised cutting parameters that allow manufacturers to produce up to 150,000 medical gowns and 6m non-medical masks per week. It also includes PPE patterns, tech packs, and a regulatory consulting package for “rapid conversion” of conventional sewn goods production to PPE.
29 April – Texollini
LA-based vertically integrated manufacturing facility Texollini has developed a T19 Eco performance unisex mask that is designed, knitted, dyed, printed, sewn and packaged in California. The mask is made with proprietary micro denier polyester/spandex 3-dimensional spacer fabric (aka scuba/neoprene) and dries quicker than cotton, according to the firm, as it holds less moisture. A portion of the firm’s profits will be donated to the American Red Cross.
28 April – Chaco Footwear
Chaco Footwear has produced and donated nearly 3,000 masks since shifting the focus of its Michigan-based ReChaco factory and mobile factory bus from sandal repairs and product customisation to the production of face masks and other critical protective equipment. Chaco is working with parent company Wolverine Worldwide and local organisations to source fabric and vet materials for production. The brand has shared its patterns, sourcing leads, and learnings as a resource for the outdoor industry, other companies, and individuals looking to contribute during the pandemic.
28 April – Late Sunday Afternoon
Apparel company Late Sunday Afternoon has partnered with mobile app developer Dogtown Media and the Schusterman Family Foundation on a 1-for-1 protective mask donation campaign. Within the first hour of launching, the campaign received hundreds of orders and saw Late Sunday Afternoon CEO Matthew Schildkret retool the company’s equipment and bring in team members to ramp up production. Within a week, the campaign scaled to thousands of placed orders per day, leading to a micro-grant of US$2,500 from the Schusterman Family Foundation. The funds will be used to send protective masks to organisations including Columbia University Medical Center in NYC, Minneapolis-based non-profit Allina Health, and Columbus Colony Elderly Care in Ohio.
27 April – John Lewis
John Lewis is reopening its textiles factory ‘Herbert Parkinson’ in Lancashire, to make protective gowns for the NHS. Partners who usually sew bespoke blinds, curtains, and pillows and duvets will this week begin making around 8,000 washable, clinical gowns for the Northumbria NHS Foundation Trust. The retailer is also donating over 20,000 metres of cotton fabric from its haberdashery departments and distribution centres to “For the Love of Scrubs” and ‘Scrubs Glorious Scrubs’, groups who now have thousands of members who are making scrubs for the NHS. The donated fabric is expected to make around 6,000 scrubs.
24 April – Lenzing AG
Austrian cellulosic fibre producer Lenzing has partnered with Palmers Textil AG to found Hygiene Austria LP GmbH. The newly founded company, of which Lenzing holds 50.1% and Palmers Textil 49.9%, will start producing and selling protective masks for the domestic and European markets from May 2020. Initially, Hygiene Austria LP GmbH will produce so-called mouth-nose protective masks (MNS) and surgical protective masks of class EN14683. The facility has a monthly production capacity of 12m pieces which is expected to increase to more than 25m masks per month over the next few weeks. There are also plans for geographic expansion.
24 April – Burberry
Burberry’s trench coat factory in Castleford is now manufacturing non-surgical gowns and supplying them to the UK National Health Service. It is also sourcing surgical masks through its supply chain and supplying them to the NHS and charities such as Marie Curie, which provides nursing care for families living with terminal illness in the UK. To date, Burberry has donated more than 100,000 pieces of PPE.
23 April – StringKing
StringKing, a sporting goods and apparel manufacturer based in Los Angeles, has pivoted to supply millions of face masks and other PPE for general use by hospital systems, essential personnel, and the general public. The company is currently producing more than 6m 3-ply disposable face masks, 3m protective gowns, and 300,000 reusable cloth face masks. The firm said its daily output this week will reach up to 300,000 3-layer face masks, 70,000 protective gowns, and 40,000 cloth face masks. StringKing will be donating the face masks to those hospice workers, nursing homes, assisted living facilities, and first responders. The company is currently increasing production to more than 20,000 units per day with the help of local sewing operators and facilities. To keep up with demand, StringKing has directly hired about 50 garment workers and indirectly employed an additional 50, and is installing more than 50 mask-specific sewing machines at a number of local facilities, adding about 200 more employees to the effort who it said “previously had little or no work during the shutdown.”
23 April – Taiwan Textile Federation (TTF)
Taiwan Textile Federation (TTF) has established a complete surgical mask supply chain by integrating upstream, midstream, and downstream textile industries and with the help of textile manufacturers including Formosa Plastic Group, Formosa Chemicals & Fibre Corporation, Far Eastern New Century Corporation, KNH Enterprise Co., Ltd., China Surgical Dressings Center Co., Ltd. and Chang Hong Machinery Co., Ltd. Non-profit TTF said Taiwan has donated 15m surgical masks to support medical staff in countries with severe coronavirus outbreaks and will continue to provide support to the international community. Under the Taiwan-US epidemic prevention cooperation framework, Taiwan has donated 2m surgical masks to the US and will continue to provide 100,000 surgical masks every week. TTF added from March to April, more than 1m units of isolation gown and 100,000 units of protective suits were manufactured in Taiwan.
22 April – Eastman
Eastman is providing materials to help make critical items needed for medical, health, and hygiene products that are in short supply. So far, the firm has donated 10,000 face shields for hospitals in Massachusetts, thanks to a collaboration with SMC Ltd.; donated copolyester resins to PRP Creation as part of an effort by cosmetics companies to produce 475,000 bottles of hand sanitiser for health organisations in France; distributed window film to Harlow College to produce 300 additional face shields for hospital workers in the United Kingdom; collaborated with the Tennessee Higher Education Commission and universities to help produce 10,000 face shields; donated copolyesters to companies in Brazil to manufacture 20,000 face shields for hospitals; and, donated critical PPE including 180 N95 masks and 4,400 nitrile gloves to first responders in Massachusetts. Eastman has also converted a pilot plant at its largest US manufacturing site to produce hand sanitiser for area schools and emergency responders.
22 April – MadaLuxe Group
Luxury fashion distributor MadaLuxe Group has delivered 2m face masks to healthcare groups across the US, including OSF HealthCare, which operates 145 locations, including 14 hospitals; Franciscan Health, a healthcare group with 12 hospitals and many medical practices in the Midwest; and Northwestern Medicine, which has hundreds of locations in and around Chicago. The company is supplying only FDA-approved respirator masks and surgical masks to these and other healthcare organisations as well as to many municipalities across the country. In the coming weeks, MadaLuxe will donate hundreds of thousands of additional masks to various groups and organisations in the US. To date, the company has committed to donating masks to UCLA, Mount Sinai, Cedars Sinai and OSF, among others. The group has created a new internal division called MLG Health to focus specifically on supplying millions of units of personal protective equipment to hospitals and other healthcare facilities. The new group is leveraging MadaLuxe’s strong global network and advanced planning capabilities to source and distribute FDA-approved masks to the healthcare sector and plans to expand its scope in the future.
22 April – NatureWorks/Nonwovens Institute (NWI)
A long-standing partnership between NatureWorks and the Nonwovens Institute (NWI) at North Carolina State University (NC State) has resulted in a new spunbond nonwoven technology enabling the production of at least 10m additional N95 surgical masks. NWI has converted the use of its research and training pilot production line to produce the face mask materials, and NatureWorks has donated the Ingeo resin needed to produce the spunbond material. NWI currently has an agreement to provide large amounts of spunbond nonwoven material to several key partners, which will make masks at their manufacturing facilities. They plan to provide the new masks to local communities in need. NC State has also ordered machines that will allow NWI to make surgical masks in its Centennial Campus facilities. Those machines should arrive in the next month.
22 April – Indorama Ventures
Indorama Ventures has donated hygiene necessities, which include 40 sets of PPE, 70 litres of liquid soap and shampoo, 500 nano-zinc fabric masks, and 30 litres of hand-cleaning gel alcohol, to key institutions handling the Covid-19 outbreak in Thailand. Along with supporting medical personnel, Indorama Ventures is supporting the communities in which the company operates. Led by volunteer employees, Indorama Polyester Industries PCL, the fibres and PET recycling facilities located in Nakhon Pathom, has helped to disinfect residential areas, bus stops, roads and footbridges and donated masks and hand sanitisers to police officers. Rayong-based TPT Petrochemicals PCL, a producer of PTA used in manufacturing PET, also distributed six sets of PPE to the Sawang Porn Kusol Foundation. In addition, IVL has contributed through its facilities worldwide.
22 April – JD.com/TUV Rheinland
JD.com has donated 5m masks, 50 invasive ventilators, and more than 600,000 pieces of protective clothing, goggles, medical gloves, and other medical supplies to the UK. TUV Rheinland Greater China (TUV Rheinland) provided qualification audit services free of charge for the protective equipment, helping JD.com to strictly control the safety and quality of the donated medical supplies and ensuring the supplies could be imported into the UK as quickly as possible. Through the joint effort, part of the supplies have arrived in the UK so that many overseas Chinese and students have received free masks, with 120 per person distributed through an application on the JD.com app. In addition, a large amount of the donated materials will be sent to the British government and local hospitals with the assistance of the Chinese Embassy in the United Kingdom, the Chinese Charity Federation, the British Embassy in China, and the National Health Service (NHS) of the UK.
21 April – Burlington/Ralph Lauren
Burlington is supporting Ralph Lauren in transitioning production to make isolation gowns for healthcare and other community workers in New York, New Jersey and North Carolina. The firm will provide the fashion company with its advanced barrier Maxima fabrics and technical expertise as part of the collaboration.
21 April – Shima Seiki
Computerised knitting machine manufacturer Shima Seiki has released additional knitting data for producing another type of 3D knit mask on its WHoLEGARMEnT knitting machines. Data is meant to be for cotton masks knitted using 3D WHoLEGARMEnT knitting technology that can produce items in their entirety without the need for sewing afterward. The mask data is intended for knitting with the use of silver-fiber yarn, which has antibacterial properties. The filterpouch that was featured on previously released WHoLEGARMEnT masks is eliminated, allowing this mask to be knit with a single layer of fabric, making it thinner and lighter. Mask data is available for download from the Shima Seiki Users’ Site, an archive featuring over 10,000 knit samples for use by Shima Seiki customers. Knitted cotton masks can be washed and reused repeatedly. Shima Seiki said it should be noted, however, that unlike common nonwoven surgical masks, knit masks do not have virus- and pollen-filtration functionality. Their main use is for prevention of spray from coughing and sneezing, and for reducing exposure to airborne particles such as pollen.
20 April – Parkdale Mills
Parkdale Mills subsidiary US Cotton, a manufacturer of cotton swabs, has joined an effort with the Food & Drug Administration (FDA), the Gates Foundation, UnitedHealth Group, and Quantigen to ramp up production of spun synthetic swabs to help the country’s frontline health care workers administering tests for Covid-19. US Cotton, based in Cleveland, Ohio, plans to leverage its large-scale manufacturing capacity to rapidly increase production of large quantities of these fully synthetic, polyester-based Q-tip-type swabs which are in short supply for testing kits across the country. This is the second major Covid-19 relief project that Parkdale has helped lead. The company has also established a supply chain that includes Hanes, Fruit of the Loom, and other US companies in the production of PPE masks.
20 April – SanMar
UPS today announced that it is operating flights to deliver 1.7m face masks made by SanMar. The firm converted its clothing production facilities in Honduras and Tennessee to support protective mask production and distribution. It is part of a coalition of American apparel brands and textile companies responding to the urgent call from the White House to fast-track the manufacturing of face masks. Since the programme began at the end of March, SanMar has manufactured more than 100,000 masks at its Tennessee production facility. When the masks are completed, UPS will ship the cargo to healthcare providers throughout the US. Production and distribution started in April of more than 1.7m masks produced at SanMar’s Honduras location for shipment to their Jacksonville, Florida, distribution centre. The masks will be shipped via UPS air freight on pallets and then repackaged to the correct quantities for distribution by UPS’s small package division to healthcare providers around the United States.
20 April – Pattern Room
Australian online pattern company, Pattern Room, plans to develop PPE patterns in the coming weeks to expand its medical supply offering. The Melbourne-based firm has recently created medical scrub patterns that can be downloaded by manufacturers worldwide. Developed in conjunction with front line medical team members caring for Covid-19 positive patients, the patterns range in size from XS-8XL for men and 6-28 for women.
20 April – Meiyume
Fung Group company Meiyume, which supplies products to the beauty industry, has transformed its Asia and UK manufacturing facilities to produce hand sanitisers and hand wash for medical facilities and their staff. Its teams in Thailand and Indonesia have converted factory equipment and are producing 80 tonnes of hand sanitiser per day and up to 6.5m retail-sized units per month. In the UK, it is working to produce hand creams that will be donated to the new NHS Nightingale Field Hospitals across the country. The Meiyume team is also helping to source surgical masks and PPE materials.
20 April – DeanHouston/Exhibit Logistics
Marketing communications firm DeanHouston, Inc has converted the large-format printing capabilities of its trade show production division Exhibit Logistics to include the manufacturing of washable, double-layered, cloth face masks. The company converted its grand format dye-sublimation printer and entire facility to begin full-scale production. Company logos or any number of designs can be printed on the face masks which are available in multiple styles and designs, including double-sheet cotton cover; single sheet polyester cover with single sheet cotton barrier and filter pocket; or single sheet polyester cover with double sheet barrier and filter pocket. Multiple filter types (not included) can be inserted into the filter pocket. Exhibit Logistics is also producing face shields that have been assembled using the CDC-compliant process. The company’s face shields include a forehead guard with thin-gauge and a flexible PVC outer shell and soft foam insert. On the company’s face shield, there is a head strap with a one-size-fits-all adjustable Velcro design for long wear and maximum comfort. The face shields have been constructed using lightweight materials, approved by the Food and Drug Administration (FDA. For every ten masks DeanHouston produces, one mask will be donated. Minimum orders of 500 masks are being accepted at this time.
17 April – Kizik
Utah-based footwear firm Kizik will immediately donate 1,000 pairs of hands-free Kizik shoes to healthcare workers after data from a new study published by the Centers for Disease Control and Prevention suggests that Covid-19 may travel on shoes and that the footwear of medical staff, in particular, could be carriers. Kizik shoes create a custom, hands-free fit for each foot by using an aerospace-grade titanium band that rebounds around the heel to hold the foot securely. CEO Monte Deere said the firm’s shoes could help front-line healthcare workers as they would not need to use their hands to put on, take off, or lace up Kizik shoes, therefore reducing the likelihood of the coronavirus travelling from shoes to hands.
17 April – Lacoste
Lacoste is to ramp up production of face masks after reaching its initial goal of producing 100,000. The fashion firm said it will intensify its production to reach 200,000 masks with two dedicated production lines in its factory in Troyes, France. Its factory in Argentina and Turkish partner, Eren Holding, has also adapted to the manufacture of medical masks and gowns. Lacoste said it will continue its efforts to produce masks beyond April and for “as long as the health situation calls for it.”
17 April – Dow
Dow has developed a simplified face shield design which it is sharing through an open-source file to help accelerate production rates. Thanks to its flexible design, the shields can be produced from a variety of readily available polymers and can be cut using several high throughput technologies, such as water, laser and die cutting techniques. It is also simple and lightweight, comprised of just two pieces – a shield and forehead cushion – which eliminates multi-component assembly that can slow production, allowing for faster distribution. In addition to sharing the open-source design, Dow is producing 100,000 face shields to be donated to the state of Michigan for distribution to hospitals. Michigan-based tinkrLAB is serving as a key development partner providing laser-cutting and assembly and has already completed an initial allotment of production. Dow is also seeking to partner with other companies with film manufacturing and cutting capabilities to continue to develop critical PPE.
16 April – Dickies/VF Corporation
Global workwear brand Dickies is leveraging parent company VF Corporation’s global supply chain and capabilities by converting several manufacturing facilities to produce PPE garments. With initial production beginning next week, VF Corp and Dickies expect to produce and deliver 50,000 gowns in May and intend to create production capacity to make up to 675,000 gowns by June and up to 3.4m by September. The isolation gowns will be made with fabric sourced from industry partner Milliken & Company, in accordance with guidelines issued by the FDA.
15 April – Mango
Mango is to manufacture 13,000 disposable polyethylene gowns for healthcare teams in collaboration with the Pablo Horstmann Foundation, which has acquired 30,000 metres of approved fabric. The company has transformed its usual process of creating garment collections to a large-scale system to manufacture gowns. More than 30 Mango employees have been working on the project since 8 April at the company’s facilities in Palau-solità i Plegamans. The Pablo Horstmann Foundation will also be responsible for distributing the 13,000 gowns among hospitals, care homes and centres for the disabled, according the greatest vulnerability and need.
15 April – Brother International Corporation
Brother International Corporation is donating up to 100 industrial sewing machines to support the efforts to manufacture PPE. The first to receive donations, Los Angeles Apparel, Beverly Knits, Inc and SanMar, are part of a coalition of American apparel brands and textile companies responding to the urgent call from the White House to fast-track the manufacturing of face masks. Separate from the coalition, Brother will also be donating industrial sewing machines to Brooks Brothers to support its manufacturing efforts. The apparel companies are receiving Brother industrial sewing machines free of charge as a donation in support of their efforts to manufacture much-needed personal protective equipment.
15 April – DuPont
DuPont has launched a new programme, #TyvekTogether, to increase the overall availability of Tyvek personal protective garments, which at full capacity, could deliver 6m additional non-surgical isolation gowns per month. DuPont has invested in equipment and technology to significantly increase its production of Tyvek and Tychem garments globally. Since January it has increased production of Tyvek garments by more than 9m garments per month specifically for Covid-19 response, which is more than double the amount produced for any prior crisis. #TyvekTogether will introduce a new specialised Tyvek fabric to help drive production to 15m garments a month. As part of the initiative, DuPont will provide garment designs—including patterns and virtual manufacturing support—for a non-surgical isolation gown and a coverall that are optimised for simple and productive manufacturing. With these patterns and technical assistance, DuPont aims to accelerate the speed that new converters are able to begin producing PPE.
14 April – Lectra
Lectra has launched a volunteer effort to address the shortage of PPE and is making the full resources of its company and experts available. The firm is opening the Technology Center at its Atlanta headquarters, which includes a fully operational cutting room usually used for tests and demonstrations, but needs volunteer partners to provide fabric, sewing, and distribution. In addition to producing PPE at the Technology Center, the company is also providing its experts to help clients pivot manufacturing technology to the production of PPE across Lectra’s service lines.
14 April – Delta Apparel
Activewear and lifestyle apparel maker Delta Apparel will leverage its manufacturing facilities to begin producing cotton face masks. The firm has joined a coalition of apparel brands that are responding to urgent calls for companies to help produce face masks during the Covid-19 global pandemic. Once fully ramped up, the coalition, inclusive of Delta Apparel, expects to produce up to 10m face masks per week in the United States and in Central America. In addition to the production of face masks with the coalition, Delta Apparel is also producing and selling non-medical grade face coverings.
14 April – Beverly Knits
The Beverly Knits group of US textile and garment manufacturers continues to work together to provide face masks for the US Department of Health and Human Services. The number of companies in the group continues to grow, with 31 firms currently on the team. Fabric is now in production in factories in North and South Carolina, while cutting and sewing of the masks has begun across the US. Production started the week of 3 April after all facilities were qualified. The production goal is 200,000 masks during the first week and ramping up to 2m masks produced per week shortly thereafter.
14 April – Chargeurs*PCC Fashion Technologies
Chargeurs*PCC Fashion Technologies has launched a new brand called Lainière Santé that will offer a full line of personal protective products for consumers. The products will be available for sale on Amazon.com. Since the beginning of the coronavirus crisis, interlinings supplier Chargeurs has shifted a significant portion of its textile production toward healthcare-related personal protective items. As well as manufacturing more than 10 million face masks per week, the company is also developing scrubs, protective gloves, protective bactericidal films, advanced textiles with antimicrobial properties, and intelligent fabrics.
13 April – Adidas & Carbon
Adidas has partnered with digital manufacturing platform Carbon to produce 3D printed face shields using the same material, Elastomeric Polyurethane, co-created for its 4D midsoles. Through the quick production turnaround that 3D printing enables, Carbon has been able to scale production from 18,000 face shields a week to upwards of 50,000. To scale even further, the firm is also sharing print files with its entire global network so anyone with access to a Carbon printer and material will be able to create face shields to address needs in their local areas.
13 April – Eastman
Eastman has donated 600sq ft of material to Purdue University to produce protective lenses and face shields for medical personnel. More than 40 volunteer faculty and staff members are using the school’s laser cutting system to produce up to 3,000 lenses and 4,000 face shields. The protective equipment will be distributed to hospitals across Indiana. Eastman has also donated material to organisations in Tennessee, Virginia, and Brazil for the production of face shields. In Europe, the company has donated resins to customers that are making hand sanitiser instead of cosmetics.
9 April – Tapestry
Tapestry has launched an initiative to manufacture medical equipment for healthcare workers by repurposing its existing 3D printing capabilities in New York. The group has also announced an employee-initiated volunteer programme that is coordinating with 3D printing industry bodies to repurpose its existing 3D printers to support healthcare professionals. This will include the printing of disposable parts required for respirators and ventilators, test swabs, and face shields. Resources will also be made available to create 3D printed parts for R&D prototypes needed by engineers and specialists working on Covid-19 related development projects. The initiative is being coordinated with various 3D printing industry bodies, along with the NIH 3D Print Exchange and 3D printing companies.
9 April – Delta Galil
Delta Galil’s European Brands subsidiaries Schiesser and Eminence recently retrofitted selected factories to produce reusable fabric face masks that are machine washable. Schiesser is to provide face masks to European governments, police and fire departments, NGOs and social services organisations, including more than 1m masks for the Czech and Slovakian governments and a German protective equipment company. The Eminence subsidiary in France has begun providing face masks to local emergency services personnel and will be producing 400,000 masks per month to meet the needs of police and fire departments, the French military, NGOs and social services organisations. Delta Galil will also be producing masks in its facilities in Thailand to meet the needs of local security and medical personnel.
8 April – Elevate Textiles
Elevate Textiles’ Burlington and American & Efird (A&E) brands will participate in the recently launched Gerber PPE Task Force. The industry-wide effort combines resources and expertise to support manufacturing operations and brands as they increase their production or transition their operations to produce PPE. Elevate’s Burlington, A&E, and Gütermann brands provide critical barrier fabric and thread components used in the manufacturing of lifesaving PPE products including masks, isolation gowns and other medical garments.
8 April – Gildan Activewear
Gildan Activewear is working with one of its customers in the imprintables channel to support a cooperative consortium of apparel and textile companies to help produce non-medical face masks to be distributed to support hospitals and health care workers. Both the design and fabric are being provided by partners of the consortium. In addition, Gildan is working with retail partners to produce non-medical face masks and isolation gowns. The Canadian apparel maker said it has received authorisation from the Honduras government to partially reopen one of its textile facilities to produce the fabric needed for the masks and gowns, and one of its sewing facilities for assembly.
8 April – Supima
Non-profit Supima has donated hundreds of yards of Supima fabric to its Supima Design Competition alumni network, which includes designers and design students from across the US, that has since been used to create thousands of homemade masks for medical personnel. Relief programs Supima has donated fabric to include Sew4lives and Operation COVID-19 Garment Revival.
8 April – Coats
Industrial thread maker Coats has joined a dedicated task force set up by Gerber Technology to help manufacturers convert their production to PPE. Joining as a coalition partner, Coats plans to draw on its extensive network of apparel manufacturers to work as an “industry matchmaker” to rapidly mobilise the work of the task force.
8 April – Jeanologia
Jeanologia has repurposed its ozone-based G2 technology, which it uses for the sustainable treatment of jeans, into an innovative method for sanitisation and disinfecting face protection masks.
8 April – SEAMS
SEAMS, the National Association for the US Sewn Products Industry, has established a new resource offering a range of patterns that can be used to make PPE from home creations to approved medical products. The ‘Pattern Hub’ includes face masks, medical gowns, and non-clinical face masks, with guidance including how-to videos.
7 April – Nike
Nike has developed full-face shields and powered, air-purifying respirator (PAPR) lenses, made with elements of the brand’s footwear and apparel. Nike’s version of the full-face shield utilises collar padding once destined for shoes, cords originally earmarked for apparel, and the TPU component of Nike Air soles. The three parts of the full-face shield come together in a nine-step process, formalised through a collaborative effort between Nike’s Innovation teams and manufacturing groups at Nike’s Air Manufacturing Innovation (Air MI) facilities in Oregon and Missouri. TPU will also be employed to create new lenses for PAPR helmets. Nike’s PAPR lenses take the same TPU as the face masks and have welded segments to fit the specifications of PAPR helmets. To serve the current response, Air MI is rapidly adapting its capacities, while also adopting new production line procedures in keeping with rapidly-changing government guidelines. Nike delivered the first shipment of donated full-face shields and PAPR lenses to Oregon Health & Science University (OHSU) on 3 April.
7 April – HanesBrands
HanesBrands is ramping up additional production to make more than 320m FDA-approved all-cotton face masks over the coming weeks. The company is part of a consortium of apparel makers that are converting production capacity to the making of reusable and washable 3-ply face masks for the US Department of Health and Human Services. Of the more than 320m masks the company expects to make, about 10m have been delivered and the company is ramping production to make approximately 40m per week. The masks, designed by the company’s product development team to meet technical specifications, including fabric chemistry, are intended for everyday wear to help mitigate the spread of the novel coronavirus and serve in healthcare settings where N95 respirator masks and surgical masks are not required.
7 April – Archroma
To address the global shortage of the thickener typically used in the production of hand sanitising gels and other home care and personal care products, Swiss colour and speciality chemicals maker Archroma has introduced an alternative. Mowiplus HPC 9600 offers good performance and cost levels and does not require the 12-hour hydration process traditionally required. Mowiplus HPC 9600 is currently available in Brazil.
7 April – La Sportiva
La Sportiva has converted its production facility from manufacturing outdoor mountaineering equipment to producing medical laboratory coats and protective masks, with an initial commitment to supply 55,000 protective masks to hospitals and the Civil Protection Department. It has also applied for the certifications to provide the equipment directly to hospitals. Production is well underway on an initial 1,000 masks a day with manufacturing increasing to 3,000 pieces per day shortly.
6 April – TechniTextile Québec, CTT Group and Vestechpro
Canada’s technical textile materials and clothing industry, represented by TechniTextile Québec, CTT Group and Vestechpro, has established a local supply chain capable of supplying the Québec and Canadian governments with disposable and washable protective uniforms. As of today, Logistik Unicorp is taking over the coordination of the manufacturing of protective Level 1, 2 and 3 gowns in collaboration with Duvaltex, Soleno Textile, Stedfast, Texel Technical Materials, Textiles Monterey, Maxime Knitting and CTT Group.
6 April – Alpargatas
Alpargatas, parent company of the Havaianas beach sandal brand, is spearheading the ‘Goodwill Partnership’ network to unite partners and volunteers who want to contribute in the fight against Covid-19. Initially, Alpargatas will produce 250, 000 N95 masks to be donated to the public health services in the Brazilian states of Paraiba, Pernambuco, Minas Gerais, and Rio de Janeiro, where the company’s factories are installed. In addition, the company will donate 18,000 pairs of shoes suitable for healthcare environments to São Paulo hospital professionals, made in the Havaianas factories which have been temporarily repurposed and adapted.
6 April – Kontoor Brands
Kontoor Brands has begun producing about 50,000 Level 1 patient gowns and 10,000 disposable isolation gowns for clinicians. The gowns will be produced by Kontoor at its owned and operated manufacturing facilities with patient gown fabric donated by Copen United Limited and Cotswold Industries, Inc, zippers from YKK (USA) In., and disposable protective fabric for the isolation gowns from Precision Fabrics Group, Inc, based in Greensboro. The gowns will be donated to North Carolina-based hospitals, including Wake Forest Baptist Health.
3 April – Industrial Sewing And Innovation Center (ISAIC)
ISAIC, the national sewn goods manufacturing and training non-profit based in Detroit, is centralising one of the area’s most substantial responses in the production of PPE. ISAIC has been working with the City of Detroit, the Michigan Economic Development Corp’s Pure Michigan Business Connect, Carhartt, Rock Family of Companies and Empowerment Plan on a two-pronged approach: First, to mobilise local apparel manufacturing to produce standardised, centralised PPE and second, automated, mass production of pleated surgical masks. It said millions of pleated medical-grade masks and thousands of sewn surgical masks and isolation gowns will be available.
2 April – Levi Strauss & Co
LS&Co is donating medical-grade masks it had stored for employee safety to hospitals around the globe (nearly 10,000 to date) and is connecting employees to resources to donate any extra N95 masks and other PPE they might have to their local hospitals. The denim giant is also exploring what is possible from both a manufacturing and innovation perspective, with employees across the company having already volunteered to sew homemade masks for medical workers not directly treating suspected Covid-19 patients and other community members in less high-risk situations.
2 April – Target Corp
Following Target’s previous donations of anti-viral and N95 respirator masks to first responders and healthcare professionals at more than 50 organisations across the country, the retailer also announced that it will donate an additional 2m KN95 respirator masks to the medical community.
2 April – Jockey International
On a national level, Jockey will supply health care workers on the front lines with critically needed Tier 3 Isolation Gowns. In partnership with Encompass Group, Jockey will immediately restart manufacturing Tier 3 Isolation Gowns and is expecting to initially donate 250,000 gowns at a pace of 30,000-50,000 units per week. As production begins, Jockey will assess the ability to significantly increase output. On a local level, Jockey will supply the Kenosha Fire Department, Wisconsin, with 10,000 N95 masks and 10,000 Level 1 surgical masks. It will also be donating 10,000 units of scrubs to the front-line doctors and nurses at the Jacob K Javits Convention Center in New York City. The Javits Center has been transformed into a temporary hospital to handle patient overflow caused by Covid-19.
2 April – Milliken & Company
Global textile manufacturer Milliken & Company is manufacturing critical barrier protection fabrics to be used in gowns and headcovers for healthcare professionals. Milliken is also researching and developing materials for incorporation into N95-grade masks. These new innovations complement the firm’s existing range of products that can be used for temporary shelters in situations where it’s deemed necessary to set up transitory field hospitals.
1 April – RadiciGroup
RadiciGroup is to deliver the first 5,000 gowns to Papa Giovanni XIII hospital in Bergamo, Italy, after calling on local garment makers to establish an approved production chain to manufacture protective equipment for medical personnel.
1 April – QIMA
Supplier compliance service provider QIMA will begin offering its inspection services free of charge in China for productions of disposable filtering face masks and medical protective gear. QIMA quality inspections are performed before shipment and consist of sending qualified inspectors to production sites to check workmanship quality, assess quantities, packaging, labeling and ensure factories have the required certificates and export licenses.
March – Hugo Boss
Hugo Boss has dedicated its clothing production site at its global headquarters in Metzingen to the manufacture of face masks, which will be donated to public facilities. In the coming weeks, the company will manufacture about 200,000 masks. Crafted in a cotton-blend material that can be washed and reused at least 50 times, the masks are not for clinical use but they can be used in other settings, such as in nursing homes, fire departments, and by police. In addition, Hugo Boss’s license partner for fragrances Coty will also manufacture hand sanitisers.
31 March – Mango
Mango is to donate 2m face masks to the Spanish Ministry of Health. The face masks arrived at Saragossa airport today, from where Mango will now start to distribute them to hospitals throughout Spain, using its own logistics network. The company is also making its logistics capacity available to the authorities in order to help mitigate the grave social, economic and public health consequences caused by Covid-19, in the manner the authorities consider most appropriate.
31 March – Under Armour
To support the University of Maryland Medical System’s (UMMS) 28,000 health care providers and staff, Under Armour has begun to manufacture and assemble face masks, face shields and specially equipped fanny packs, and is also exploring fabricating hospital gowns for the statewide medical system. The brand will also begin providing face masks to LifeBridge, a regional health care organization based in Baltimore. Additionally, Under Armour is currently discussing the needs for supplies with Johns Hopkins Medicine, MedStar and other local medical institutions.
31 March – Tukatech
Fashion technology provider Tukatech is providing patterns for sewn medical products like face masks, hospital gowns, shoe covers, coveralls, blankets, for manufacturers shifting their focus to manufacturing PPE.
31 March – Tailored Brands
Tailored Brands’ factory in New Bedford, Massachusetts, in conjunction with a leading privately-held manufacturer and distributor of medical supplies, will begin the production of cotton washable face masks that can be used when an FDA approved mask is not available. The factory will use the manufacturer’s material and specifications and provide the sewing. Tailored Brands will bring back furloughed employees to make 50,000 masks over the next few weeks.
31 March – Burlington Barrier Fabrics
Burlington Barrier Fabrics, a division of Burlington Industries LLC, and part of Elevate Textiles, has increased production of its Maxima Medical Barrier collection, a line of reusable, fluid resistant surgical fabrics, in response to the pandemic.
30 March – PVH Corp
PVH Corp has started shipping more than 2m units of PPE that includes isolation gowns, masks and face shields to the Montefiore Health System in New York to support healthcare workers.
30 March – Shima Seiki
Computerised knitting machine manufacturer Shima Seiki has released knitting data for another version of knitted mask to be produced on its machines. This is in addition to mask data released on two previous occasions earlier this month. Knitted cotton masks can be washed and reused repeatedly. Shima Seiki said it should be noted, however, that unlike common nonwoven surgical masks, knit masks do not have virus and pollen filtration functionality. Their main use is for prevention of spray from coughing and sneezing, and for reducing exposure to allergens.
30 March – Chargeurs & Noble Biomaterials
French interlinings specialist Chargeurs*PCC Fashion Technologies has partnered with Noble Biomaterials to produce face masks and gowns using Noble Biomaterials’ silver-based technologies.
30 March – Dow
Dow is to expand hand sanitiser production at additional sites in North America, Europe and Latin America. The firm said its manufacturing sites in Auburn, Michigan; South Charleston, West Virginia; Seneffe, Belgium; and Hortolândia, Brazil possess the necessary raw material handling, mixing and packaging capabilities to do so and will join its site in Stade, Germany in production. When all of these locations are at full production, Dow’s collective output is expected to reach more than 440,000 pounds (200 metric tonnes), or the equivalent of more than 880,000 eight-ounce bottles.
30 March – Brooks Brothers
US apparel retailer Brooks Brothers is in the process of converting its New York, North Carolina and Massachusetts factories from manufacturing ties, shirts and suits to making masks and gowns. Brooks Brothers plans to use these facilities to produce up to 150,000 masks per day on an ongoing basis, to help increase access to protective gear for health care workers.
29 March – Bangladesh Garment Manufacturers and Exporters Association (BGMEA)
BGMEA is making about 20,000 substitute PPE suits for donation to healthcare personnel including doctors, nurses and hospital workers in Bangladesh. While the suits are not certified to the level required for doctors treating patients with symptoms of Covid-19, they are waterproof and will mostly be worn by support workers and doctors.
28 March – New Balance
Footwear firm New Balance has engaged a portion of its US manufacturing workforce to develop face masks to address the significant demand for these supplies. The company is producing prototypes for face masks in its Lawrence, MA manufacturing facility and hope to scale production using its other New England factories soon. “We are coordinating our efforts with our government officials and local medical institutions as well as other US consortiums and testing facilities,” the company says.
28 March – Burberry
UK fashion brand Burberry is working to facilitate the delivery of surgical masks, non-surgical masks and gowns for use by medical staff and patients. The company is utilising its global supply chain network to fast-track the delivery of over 100,000 surgical masks to the UK National Health Service, for use by medical staff. Burberry is also retooling its trench coat factory in Castleford, Yorkshire, to make non-surgical gowns and masks for patients. Production and distribution will be subject to approval from the Medicines and Healthcare Products Regulatory Agency (MHRA).
26 March – Chaco Footwear
The outdoor lifestyle footwear brand has shifted the focus of its Michigan-based ReChaco factory and mobile factory bus from sandal repairs and product customisation to the production of face masks and other critical protective equipment needed by healthcare and other first responders working through the Covid-19 pandemic.
26 March – YKK
Fastener manufacturer YKK is working to produce various PPE across its four main US manufacturing facilities in Georgia, California, Alabama and Kentucky. Among the items the firm is producing are airtight/watertight and moisture repellant zippers for isolation chambers and Level B Hazmat suits and fastening products for medical masks, hospital gowns, and medical beds and bedding.
26 March – Chargeurs Group
Fabric and interlinings manufacturer Chargeurs Group is refocusing its production capabilities on protective masks and hydro-alcoholic gel in industrial quantities.
Best-known as one of the world’s leading suppliers of narrow fabrics and elastics for end-uses including lingerie, intimate apparel, sports and activewear, Stretchline is joining the fight against coronavirus by switching its production to elastics that can be used in medical face masks.
25 March – Canada Goose
Canada Goose has committed to producing medical gear at two of its manufacturing facilities, starting in Toronto and Winnipeg, with the opportunity to extend production across additional facilities as needed. With production set to begin early next week, about 50 employees per facility will work to manufacture scrubs for healthcare workers and patient gowns with an initial goal of producing 10,000 units. The gear will be donated locally at no cost.
25 March – Allbirds
Sustainable footwear firm Allbirds has so far donated US$500,000 worth of shoes, and is asking its customer for help too. From 24 March, and running while supplies last, shoppers can bundle any shoe purchase with a donation to immediately supply a pair of Wool Runners to a healthcare professional who’s already reached out to the company.
25 March – Crocs
Crocs will offer healthcare workers across the United States the opportunity to get a free pair of shoes while supplies last, choosing from select Crocs Classic Clogs and Crocs At Work styles, with free shipping through its website. In addition, the company has also committed to donating up to 100,000 pairs of shoes to be distributed across a number of select healthcare facilities and organisations.
25 March – Gerber Technology
Apparel software maker Gerber Technology has launched a dedicated task force to help manufacturers convert their production to produce PPE.
Nike CEO John Donahoe told analysts on the firm’s third-quarter earnings call the company’s innovation and manufacturing teams are exploring designs for personal protective equipment to support doctors, nurses and others “on the frontline of this outbreak.”
25 March – Kering
Kering-owned luxury fashion labels Balenciaga and Yves Saint Laurent are preparing to manufacture surgical masks in their French workshops.
25 March – Huntsman Corporation
Chemicals manufacturer Huntsman Corporation is to begin making hydro alcoholic solution to produce hand sanitiser at its manufacturing site in Monthey, Switzerland, in response to an urgent appeal by Swiss authorities.
23 March – H&M Group
Swedish fashion retailer H&M Group is mobilising its supply chain to produce PPE to be delivered to hospitals and health care workers to help tackle widespread shortages during the Covid-19 pandemic.
23 March – A coalition of US apparel and textile firms has joined forces to build a supply chain to fast-track the manufacturing of medical face masks for hospitals, health care workers and citizens battling the spread of Covid-19. Responding to an urgent call from the White House for medical supplies, yarn spinning giant Parkdale helped lead efforts with Hanesbrands, Fruit of the Loom and six other companies to set up a manufacturing supply chain and begin ramping up production of the masks. American Giant, Los Angeles Apparel, AST Sportswear, Sanmar, America Knits, Beverly Knits and Riegel Linen also form part of the coalition.