
While the return of inflation means that rising supply chain costs are starting to erode earnings for many US companies, implementing a more integrated approach to cost management can help firms become more resilient.
“Deflation has allowed companies to improve their margins in recent years without significantly cutting costs,” according to consultants at Bain & Co. But with inflation now rising, executives realise they need to take stronger measures to meet their productivity targets.
“Successful leadership teams combat inflation before it takes its toll,” explain Peter Hanbury, David Schannon and Caperton Flood. “They’ve learned that bringing down costs as prices rise requires a more integrated approach to cost management. These leaders search across organisational boundaries for cost savings that hide in the seams between functions – the areas where responsibilities intersect.”
And the consultants say the prize is huge for those that get it right. Bain & Co research shows companies that take an integrated approach to cost management can double the typical savings from silo-based initiatives, to 10% to 20% of total costs. Under normal conditions, those additional gains bolster the bottom line, but when costs are rising, they can provide a lifeline.
“As inflation and shifting trade relations begin to affect historically stable supply chains, an integrated approach to cost management can help companies build organisations that are more resilient while developing a significant competitive edge,” they explain.
Cost reduction is a first step for most companies bracing for inflation, the consultants say, with savings usually sought in procurement, manufacturing, transportation and warehousing.
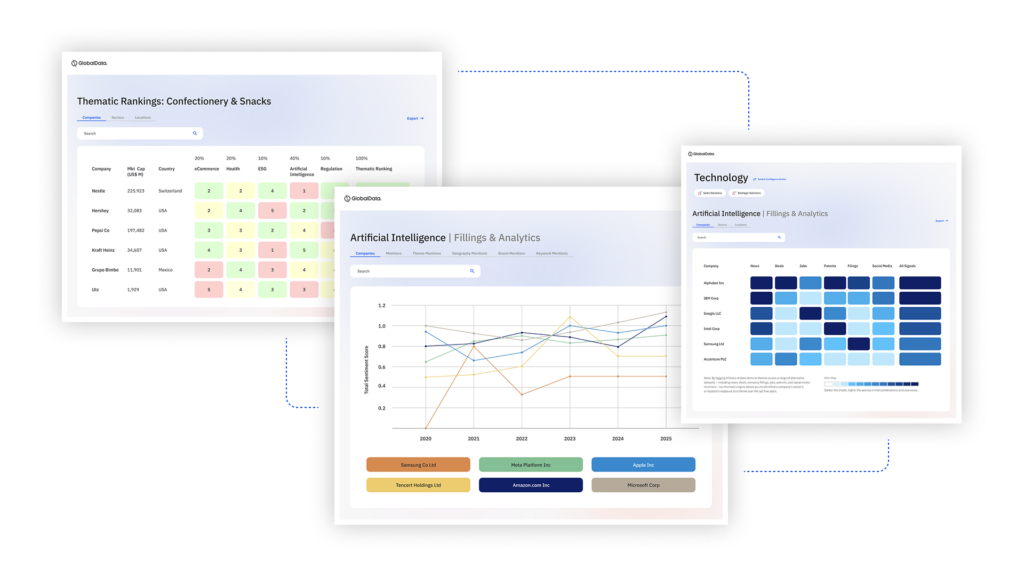
US Tariffs are shifting - will you react or anticipate?
Don’t let policy changes catch you off guard. Stay proactive with real-time data and expert analysis.
By GlobalDataBut while a smart move, they point to the risk of companies pruning unnecessary features in product design, renegotiating procurement contracts, limiting expedited shipping and deploying automation to improve manufacturing efficiency.
“The more companies reduce costs, however, the tougher it gets,” they explain. “Leadership teams that already have implemented cost initiatives year after year in each silo have to redouble their efforts to generate new productivity gains. It’s even harder to hit these efficiency targets in the face of rising inflation. In that situation, an integrated approach offers leadership teams a new and untapped source of savings.”
According to Bain & Co, reducing model variations can create a stream of savings across purchasing, manufacturing, and supply chain. Shifting the location of finished goods manufacturing could also generate cross-functional savings by reducing inventory costs or decreasing freight.
The consultants add: “Since many companies rely on silo-based organizational structures, seeking savings in the seams between individual business units or functions is not a natural process. Functional leaders tend to look only at data relevant to their function, and silos often hoard data. Taking an integrated approach to cost reduction involves changing people’s behaviour. Leadership teams need to produce and analyse data holistically to understand how costs flow across different functions.”
They offer three guidelines they believe can help companies deliver savings beyond silos:
Establish clear ownership and accountability. A “cost czar” and cross-functional teams comprise the missing accountability for cost outcomes throughout the organisation. The cost czar has the mandate to form cross-functional teams with managers from product design, procurement and manufacturing; develop a programme; and weigh the trade-offs of cross-functional cost initiatives. Often, cross-functional teams help identify costly practices and processes that erode competitiveness and otherwise wouldn’t come to executives’ attention.
Create incentives to identify savings between silos and functions. If incentives for manufacturing employees reward quality, for example, the manufacturing leader will be reluctant to find ways to lower costs, even in areas in which customers do not value the level of quality provided. Well-designed incentives may be financial or linked to broader company goals.
Use data and advanced analytics to make the business case. Individual silos lack data and analytics showing how costs flow across the organisation and where savings could lie. Developing and analysing data holistically across silos is key to identifying the opportunities within individual functions and building an integrated cost initiative.