
A new chemical recycling process has been developed that recovers viscose filaments from cotton and polyester and produces three circular outgoing product streams.
Developed by Mistra Future Fashion and described as a “breakthrough” following six years of research, Blend Re:wind turns cotton into new high quality viscose filaments and polyester into two pure new monomers.
The company says the development is an important milestone towards the future of global textile recycling systems necessary to enable circularity for fashion and textiles.
“Our separation process, Blend Re:wind, is developed having existing industrial processes in mind, and our aim is to integrate as much as possible to minimise both environmental and economic costs, while boosting businesses,” says Dr Hanna de la Motte of Mistra Future Fashion and research scientist at RISE.. “Scaling up from lab scale is the biggest challenge at the moment, and it is also costly. The integration possibilities of the Blend Re:wind process would however address these challenges in feasible ways.
“There are many brilliant recycling innovations in progress globally at the moment, highly needed for successful future recycling systems. Different processes will most probably be needed and we hope that Blend Re:wind is one of these on the global market in the future.”
The project focuses on chemical recycling of polyester/cotton (polycotton) fibre blends with the objective to separate and generate relevant outputs for future industrial use; polyester monomers and a cotton pulp suitable for regeneration into cellulosic textile fibres (such as viscose fibres).
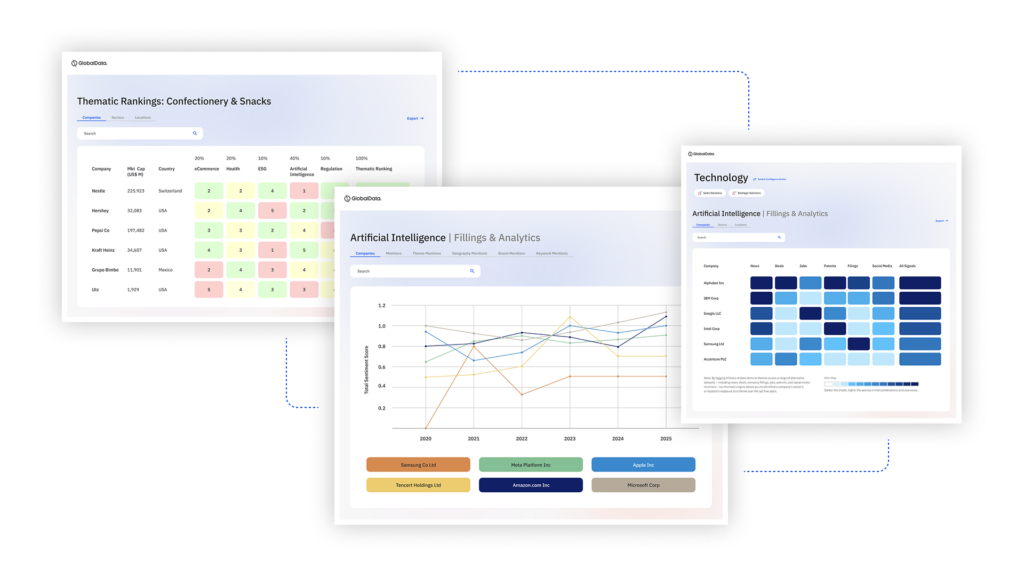
US Tariffs are shifting - will you react or anticipate?
Don’t let policy changes catch you off guard. Stay proactive with real-time data and expert analysis.
By GlobalDataMistra says the key focus has been on the cotton recycling stream and to produce high quality viscose filaments from the separated cotton residue, which it says is crucial for further industrial processing towards recycled fabrics.
The filaments have the same quality as filaments made from commercial dissolving pulp used in existing viscose production. The separated polyester residue, polyester monomers, can be re-polymerized into high quality polyester. The monomers are suitable for integration with existing chemicals processes, and Mistra says partnerships have been established and experiments performed.
The company says a strong benefit with this process is that the separation takes existing industries into consideration, and the aim is integration with existing forest and chemical industries, or other recycling options. The separation uses chemicals already utilized in the Swedish forest industry, and in the viscose industry, to facilitate possible integrations.
Additionally, the process has a strong environmental performance as it is water based and uses only common, cheap bulk chemicals and a catalyst.