
The researchers, led by Helen Zha, assistant professor in the Isermann Department of Chemical and Biological Engineering, have received the grant from the National Science Foundation (NSF). They will look at developing textiles made from fungi, plants, and artificial silk protein.
The fashion industry is responsible for immense amounts of waste. In response to consumer demand for inexpensive clothing, manufacturers rely on textiles derived from crude oil and methane: polyesters, polyurethanes, and nylons, the researchers say. Many of the products are worn minimally before being disposed. The result? The clothes are incinerated or sent to landfills and because these materials never biodegrade, they remain as pollutants in the environment for hundreds of years. The fashion industry now accounts for 5-10% of all global greenhouse gas emissions, and that figure is expected to grow.
With this grant, Zha and the Rensselaer team will develop processes for manufacturing renewable fossil-free yarns, dyes, and leather-like fabrics made from fungi, plants, and artificial nature-inspired proteins. These biodegradable textiles perform as well or better than the fossil-derived materials that they will replace. The team will also develop leather alternatives using the same ingredients, since current leather manufacturing is not sustainable.
“Materials sustainability is currently one of the biggest challenges facing society,” said Zha. “While research in my lab works to address a broad range of technological challenges such as materials for enhanced drug delivery or tissue regeneration, reducing recalcitrant waste and developing new materials that are made from renewable resources are also top priorities.”
Zha will work with Daniel Walczyk, professor of mechanical, aerospace, and nuclear engineering; Johnson Samuel, associate professor of mechanical, aerospace, and nuclear engineering; Kenneth Simons, associate professor of economics; and Mattheos Koffas, Dorothy and Fred Chau ʼ71 Career Development Constellation Professor in Biocatalysis and Metabolic Engineering. Walczyk and Samuel will develop new manufacturing processes for hemp and mycelium-based materials that incorporate artificial silk protein as an additive. Simons will examine the dynamics of industrial organization and technological change. Koffas and Zha will engineer microorganisms to produce artificial silk proteins and textile dyes.
“Making sustainable materials is a big challenge,” said Shekhar Garde, dean of the School of Engineering. “I am pleased to see that convergence of ideas from different disciplines focused on biomolecules, processes, and materials is helping address this challenge.”
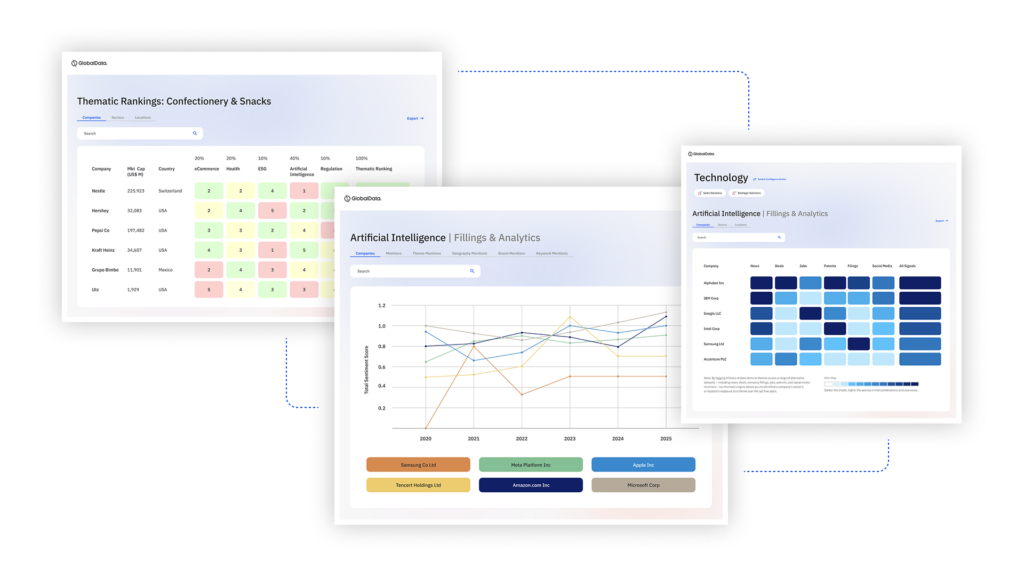
US Tariffs are shifting - will you react or anticipate?
Don’t let policy changes catch you off guard. Stay proactive with real-time data and expert analysis.
By GlobalData“Natural spider silk is one of the most robust materials found in nature,” Zha added. “However, farming spiders is impossible due to their cannibalistic nature. Instead, we engineer bacteria to produce an artificial version. It is a commercially scalable and green manufacturing process, similar to brewing beer or making yogurt. One of our most exciting bacteria strains uses waste polyethylene as a food source to produce the recombinant spider silk protein.”
The project is one of 16 funded under NSF’s Convergence Accelerator programme, Track I: Sustainable Materials for Global Challenges, which aims to converge advances in fundamental materials science with materials design and manufacturing methods. This programme will couple end-use and full life-cycle considerations to make environmentally and economically sustainable materials and products that address global challenges.
“The Convergence Accelerator is a relatively young NSF programme, but our unique programme model is focused on delivering tangible solutions to address societal and economic challenges,” said Douglas Maughan, head of the NSF Convergence Accelerator program. “We are excited to have selected teams focused on developing use-inspired solutions to address complex societal and economic challenges.”
“This exceptional research team is not only innovating much-needed eco-friendly materials, but they are priming their innovations for market,” said Deepak Vashishth, Yamada Corporation professor and director of the Shirley Ann Jackson, PhD Center for Biotechnology and Interdisciplinary Studies (CBIS). “I’m looking forward to seeing the advances made possible thanks to this funding from the NSF.”
A lot of brands and institutions are working on sustainable solutions in the industry. Last week, BRAIN Biotech and AMSilk said the two companies were collaborating to optimise the specific properties of structural proteins for various high-performance-oriented fields of application in the textile sector.