
The Renewcell facility will repurpose over 120,000 metric tonnes of textile waste next year, otherwise destined for landfills, and turn it into new viscose for fashion.
Renewcell 1 is claimed to be the first of a new generation of climate-friendly mills that shift viscose production from being a linear extractive supply chain, with significant impact on the world’s forests, biodiversity, and climate, to low-impact, circular production.
As the global effort to combat climate change and environmental degradation accelerates there is a growing need to make fashion circular and preserve critical forest ecosystems. Over 200 million trees, many from the world’s most vital forests, are currently cut down every year to make fabrics like viscose and rayon. Renewcell’s new mill uses textile waste rather than trees to make these fabrics, sourcing from worn-out jeans and production scraps.
“We’re delighted to be the first mill in the world that is dedicated to circular manufacturing for the viscose fashion sector,” said Patrik Lundström, CEO of Renewcell. “It hasn’t always been easy but the commissioning of this facility marks the dawn of a new circular era for global fashion.”
Renewcell says strong market demand has played a key role in it coming to market at scale. Through Canopy’s work in the fashion sector, more than 500 fashion brands, designers and retailers are committed to prioritizing use of Next Generation Solutions, including viscose made from old textiles and agricultural residues, along with not sourcing from Ancient and Endangered Forests. Clear market signals of support and offtake agreements from brands and conventional viscose producers helped Renewcell unlock their financing for this first commercial-scale facility.
“As we strive to turn around the climate and biodiversity crises, we need dozens of these low-impact mills to replace unsustainable forest-based viscose production,” said Nicole Rycroft, Executive Director of Canopy. “Renewcell, their investors and off-takers have stepped up to make this first Next Gen mill a reality. We’re excited to continue to work with the marketplace and financiers to transform this supply chain at a pace and scale that’s proportional to the ecological requirements of our time.”
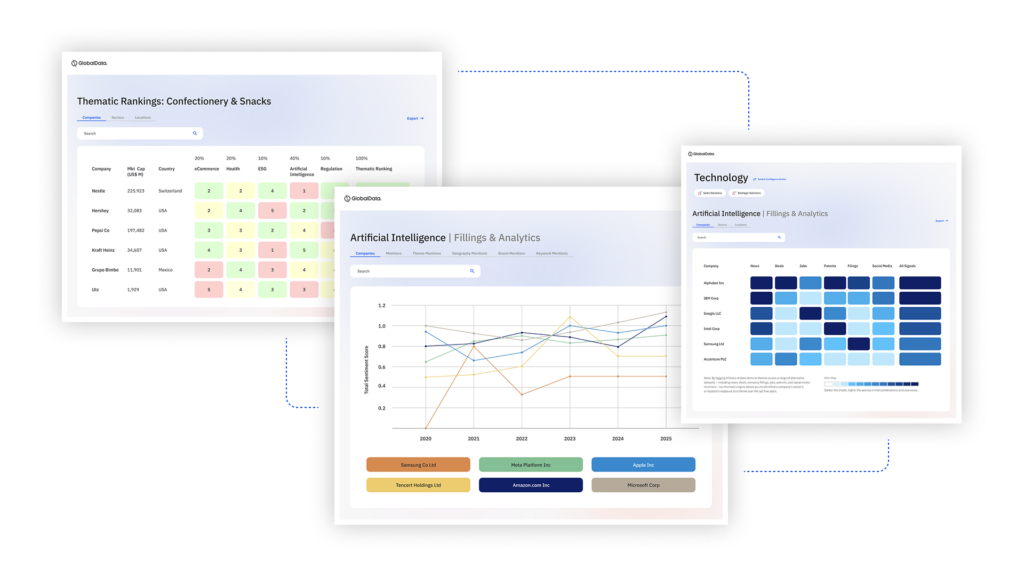
US Tariffs are shifting - will you react or anticipate?
Don’t let policy changes catch you off guard. Stay proactive with real-time data and expert analysis.
By GlobalDataIt is estimated that over 90 million tonnes of apparel waste accumulate in landfills each year — the equivalent in weight to 18 Great Pyramids. Using recycled waste textiles to make viscose rather than forest fibre saves up to 15 tonnes of CO2e per tonne of product.