
Last year, the United States enacted its Uyghur Forced Labor Prevention Act (UFLPA), which bans goods made wholly, or in part, in China’s Xinjiang region on the presumption of forced labour, while countries ranging from Germany and Canada have moved forward with their own supply chain due diligence laws.
Driven by mounting concern from consumers, more than 80% of whom say they consider sustainability when making purchases, the number of these laws is certain to continue to grow.
In December, the European Union approved a law banning the sale of products linked to deforestation, and a more sweeping EU supply chain law is anticipated to pass as soon as this year.
In the United States, the government has stressed that forced labour is now a “top-tier compliance issue.” In November, US Customs began withholding imports from the largest sugar producer in the Dominican Republic due to concerns about inhumane working conditions, and for its 2023 fiscal budget, the agency has requested funds to hire 300 additional workers to enforce the UFLPA. That’s likely to translate to more Withhold Release Orders (WROs) and delays that could deeply cut into businesses’ bottom lines.
So governments’ commitment to a sustainable supply chain is clear. What’s less certain is brands’ and retailers’ ability to meet these new requirements, since many lack the systems they need to manage and monitor large and multi-tiered supplier bases. Supply chain management software platforms can help businesses by providing both visibility and automated safeguards against social and environmental risks. Here’s how.
Responsible sourcing starts with visibility
Any responsible sourcing strategy needs to start with visibility, because you can’t fix what you can’t see and understand. To ferret out human rights and environmental violations, businesses must take responsibility for mapping their supply chain partners, from the top tier to the Nth tier. It’s no longer enough to simply rely on tier one suppliers to self-report regarding the relationships they have with their own supply chain partners. Additional steps must be taken by businesses to vet and validate the information they’re provided.
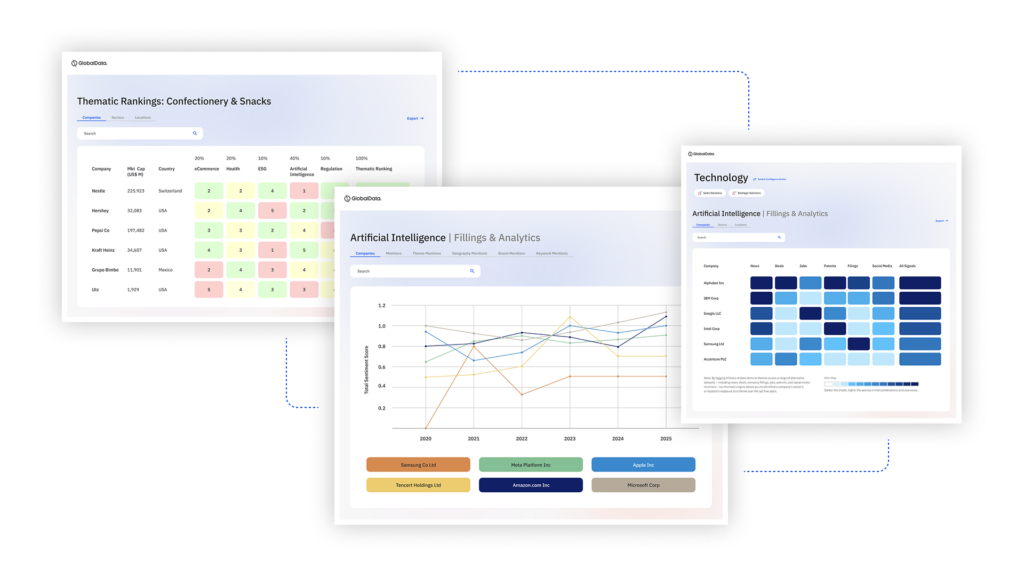
US Tariffs are shifting - will you react or anticipate?
Don’t let policy changes catch you off guard. Stay proactive with real-time data and expert analysis.
By GlobalDataSupply chain mapping software creates that visibility, exposing gaps that a business can then act on in reconciliation and improvement. Through mapping, businesses are granted a fuller understanding of their environmental footprint. For the apparel industry, that would include where their yarns and fabrics come from, how much carbon they’re emitting, and whether they’re making progress toward reducing water usage and pollution.
While the specific requirements of recent global supply chain laws vary, the practical implications of many of them are the same: Brands and retailers must have complete documentation of their suppliers, from raw materials to finished goods, and they need to be able to chart the chain of custody of materials, including where they were shipped from, where they were made, and where they were stored.
With that visibility in place, businesses can take the next step to understand where help is needed and where action must be taken. It should be noted that not all actions must be punitive. There are cases where more modern and innovative thinking provided by the business can be shared with their supplier partners, inviting collaboration to jointly address challenges and identify opportunities for efficiencies.
Through closer strategic planning, for instance, businesses and their suppliers can consolidate shipments, reduce the number of molds they press, and save water by dying clothing in combined batches. These efficiencies reduce pollution while increasing profits. Meeting ambitious ESG targets requires participation from your supplier partners, and supply chain management platforms facilitate the collaboration necessary to work toward common goals.
Automation creates crucial safeguards
Vetting suppliers is an ongoing process. Long after onboarding, brands and retailers must continue to execute due diligence to ensure their suppliers live up to all standards and requirements.
That’s an enormous task, but supply chain management platforms make it significantly easier. Many non-profit and for-profit organisations maintain databases of vetted suppliers, but those databases still need to be cross-checked by buyers, merchandisers and compliance managers. A cutting-edge supplier relationship management system can integrate with databases such as Amfori, Higg, WRAP and others directly into sourcing workflows, allowing compliance teams to manage by exception.
Such a platform doesn’t just streamline workflows. It prevents lapses that could do incalculable damage to a company’s reputation. Many compliance officers I’ve spoken with say that one of the biggest challenges to enforcing ESG standards is that it’s too easy for merchandisers to make exceptions when it’s convenient. They may book an order, for instance, from a questionable vendor or a factory with expired certificates under the logic that “it’s just one time,” or that nobody else will notice.
Supply chain management software protects against these exceptions by preventing merchandisers from booking orders with non-compliant suppliers and preventing shipping departments from booking shipments with these vendors. The software also automatically alerts buyers and merchandisers whenever certifications have expired or there are other potential compliance issues. The ability to vet factories thoroughly and quickly is crucial when brands are determining who they trust to produce their branded products.
Good intentions alone aren’t enough for businesses that are serious about responsible sourcing. Brands and retailers need sophisticated, automated tools to organise their efforts and to track where their products and downstream materials come from. Especially amid heightened consumer scrutiny and ever-tightening regulations, these systems are key to ensuring companies live up to their obligation to eliminate ethical abuses from the supply chain.
About the author: Eric Linxwiler is senior vice president of TradeBeyond. He has over 30 years of experience in enterprise software and cloud-based platform companies with a specialty in supply chain optimization and workflow management.